Von der Simulation bis zur virtuellen Inbetriebnahme
Die Realisierung von Industrie 4.0-vernetzten Anlagen ist eng mit dem digitalen Zwilling verknüpft.
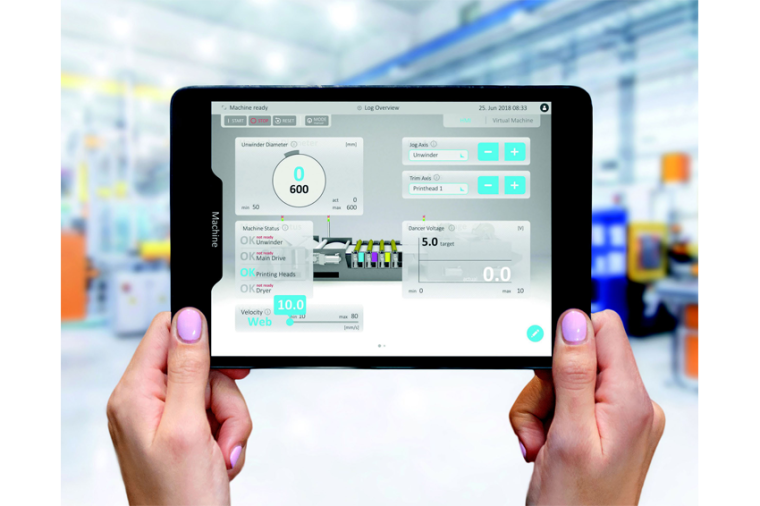
Da der Standardisierungsgrad der einzelnen Entwicklungswerkzeuge jedoch noch gering ist, klaffen bei der Durchgängigkeit erhebliche Lücken. Im Bereich der Simulation können einige von ihnen jetzt geschlossen werden. Durch das digitale Engineering von Prozessanlagen sind damit erhebliche Effizienzgewinne möglich.
Die digitale Transformation der Wirtschaft macht auch vor den Entwicklungsabteilungen des Maschinenbaus nicht halt. CAD (Computer-Aided Design), CAE (Computer-Aided Engineering) und CAM (Computer-Aided Manufacturing) werden zunehmend durch smarte Tools erweitert, die Abläufe automatisieren, Zeit- und Ressourceneinsatz reduzieren sowie die Qualität der Entwicklungsschritte laufend kontrollieren und verbessern. Effizientere Prozesse und ein verbessertes Time-to-Market sind wesentliche Faktoren, um sich im weltweit härter werdenden Wettbewerb behaupten zu können.
Mit dem digitalen Zwilling bzw. der Asset Administration Shell (AAS), auch bekannt als Verwaltungsschale, hat die Industrie ein Konzept entworfen, das diese Entwicklung entscheidend vorantreibt. Das Ziel ist ein durchgängiger Informationsstrom über den gesamten Life-Cycle der Maschinen und Anlagen hinweg: von den Daten aus Modellen der frühen Entwicklungsphase, über Maschinendaten aus der Produktionsphase bis hin zu Asset Management, Wartung und Instandhaltung.
Wege zur digitalen Simulation
In der Realität klaffen jedoch noch Lücken bei der Durchgängigkeit, da der Standardisierungsgrad der Entwicklungswerkzeuge noch gering ist. Auf Entwicklerseite besteht demzufolge eine fortwährende Unsicherheit, ob der Lieferant von Komponenten und Geräten die jeweiligen Entwicklungstools mit passenden Datenformaten unterstützt.
Schon sehr früh hat Lenze die Digitalisierung im Maschinenbau und das Konzept der Verwaltungsschale begleitet und gefördert. Jetzt geht das Unternehmen noch einen Schritt weiter und dehnt die Unterstützung für Partner auf Simulation und virtuelle Inbetriebnahme aus. Damit schließt der Automatisierungsanbieter einige kritische Lücken. OEM profitieren von erweiterten Möglichkeiten des digitalen Engineerings bei Entwurf, Entwicklung und Produktion von Maschinen und Anlagen.
Den entscheidenden Grundstein legt bereits ein 3D-Simulationsmodell, das ein vergleichsweise allgemeines Modell einer Maschine liefert. Darauf baut eine einfachere Diagnostik komplexer Maschinen auf. Geht man einen Schritt weiter und verfeinert das 3D-Modell, lassen sich bereits konkrete Aussagen über das Verhalten der Maschine vorhersagen, wie etwa der zu erreichende Durchsatz im Betrieb. Wird das Modell noch detaillierter an die spezifische Maschine angepasst, kann damit das Verhalten und auch der gesamte Fertigungsprozess auf der Maschine simuliert werden – inklusive der Logiken der Maschine und einschließlich Fehlermanagement, Wechsel von Betriebsmodi und Parametrierung. In diesem Entwicklungsstadium ist dann auch eine virtuelle Inbetriebnahme der Maschine möglich.
Belange der OEMs unterstützen
Das Unternehmen nutzt für die Simulation die Software SimulationX von ESI ITI und für die virtuelle Inbetriebnahme ISG-virtuos von ISG. Das System Virtual Teachware von Forward TTC ist für Anwendungen mit Augmented & Virtual Reality für HMI und Maschinendiagnose sowie Lernsoftware für virtuelles Training im Einsatz.
Die Anforderungen von Maschinenbauern umfassen erfahrungsgemäß Themen wie bessere Diagnose, kürzere Entwicklungszeiten oder eine präzisere Planung bei der Dimensionierung der Antriebe. Maschinenbauer können diese Anwendungen bei sich selbst einsetzen. Der Hersteller von Automatisierungstechnik berät bei der Auswahl der passenden Tools und kann bei der Modellierung von Simulationen und virtueller Inbetriebnahme unterstützen, sodass diese Anwendungen direkt beim Auftraggeber in Betrieb genommen werden können.
Entwicklung geht weiter
Während heute noch unterschiedliche Datenmodelle für die verschiedenen Anwendungen benötigt werden, sollen in Zukunft standardisierte Formate und Schnittstellen Verwendung finden. Entsprechende Konzepte sind bereits unter dem Namen FMU (Functional Mock-up Units) bzw. FMI (Functional Mock-up Interfaces) entwickelt. Das Unternehmen unterstützt die gängigen Tools, die auf dem Markt verfügbar sind und entwickelt zudem seine Toolchain für das digitale Engineering kontinuierlich weiter.
Ob bessere Diagnose, kürzere Entwicklungszeiten oder eine präzisere Planung bei der Dimensionierung der Antriebe: durch Simulation im digitalen Engineering und paralleles Engineering lassen sich Maschinenkonzepte effizient und schnell umsetzen sowie kostenintensive Nacharbeiten vermeiden. Möglich wird dies durch eine interdisziplinäre Entwicklung, indem vor allem Steuerungs- und IoT-Software an einer virtuellen Maschine bereits in frühen Konzept- und Entwicklungsphasen geprüft und validiert werden kann.
Die Autorin
Ines Oppermann, Corporate Communications, Lenze