Batterie-Recycling-Technologien – Verfahren, Trends und Marktchancen
Lithium-Ionen-Batterien stellen eine große Herausforderung für die Abfallwirtschaft dar. Gleichzeitig können Batterieabfälle auch eine interessante Geschäftsmöglichkeit bieten.
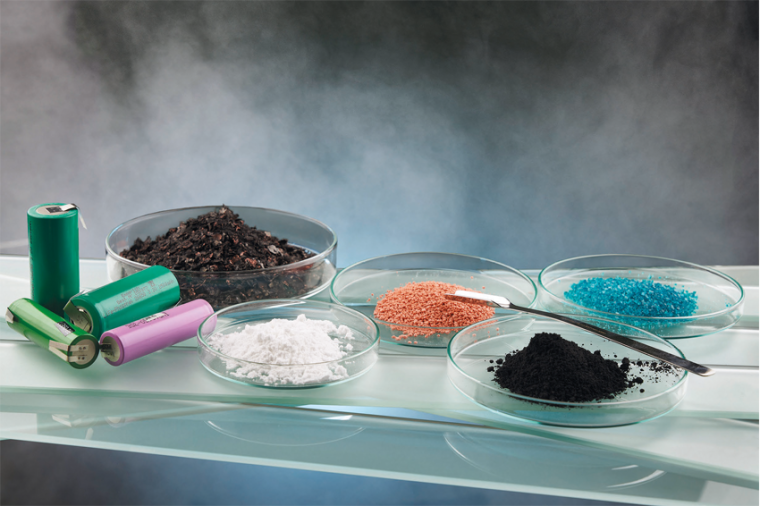
Sie stellen eine wertvolle Sekundärquelle von LIB-Materialien dar und können durch deren Nutzung die starke Abhängigkeit von Rohstofflieferanten zumindest in Teilen reduzieren.
Existierende Recyclingtechnologien wie Pyrometallurgie, Hydrometallurgie oder direktes Recycling werden durch Kooperationen zwischen Forschung und Industrie ständig weiterentwickelt. In diesem Artikel werden aktuelle Ansätze zum LIB-Recycling skizziert und die Beteiligung des KIT bei der Entwicklung geeigneter Technologien im Rahmen von drei Verbundprojekten (LiBinfinity, RHINOCEROS und LICORNE) beschrieben.
Die Entwicklung der Lithiumionenbatterie begann in den 1970er Jahren und hat im Jahr 2019 mit der Verleihung des Nobelpreises einen Höhepunkt erlebt. Sie kann als eine der bemerkenswertesten Erfolgsgeschichten moderner Technologieentwicklung angesehen werden. Die hohe Energie- und Leistungsdichte, die Zyklenstabilität und das geringe Gewicht machen LIBs zu einer idealen Energiespeicherkomponente für tragbare Elektronik und Elektromobilitätsanwendungen. Allerdings führt die zunehmende Verwendung von LIBs zu einem Anstieg der Abfallmengen in Form von Produktionsschrott und End-of-Life (EoL) Batterien. Es wird prognostiziert, dass die Zahl der recyclingfähigen LIBs zwischen 2020 und 2040 um das 700-fache ansteigen wird. Kritische Rohstoffe wie Lithium, Graphit und Kobalt sowie strategische Metalle wie Nickel und Mangan machen mehr als 50% der Batteriekosten aus. Das wirtschaftliche und umweltfreundliche Recycling dieser Komponenten stellt sowohl eine Herausforderung für die Wissenschaft als auch eine attraktive Chance für die Industrie, insbesondere den Abfallwirtschaftssektor, dar.
Handelsübliche LIBs bestehen in der Regel aus einer Graphitanode, aufgebracht auf einer Kupferfolie als Stromabnehmer, und einer Metalloxidkathode auf Aluminiumfolie (Grafik unten). Anode und Kathode sind durch einen Separator aus Polymermaterial getrennt und dadurch vor Kurzschlüssen geschützt. Alle Komponenten sind mit einem nichtwässrigen flüssigen Elektrolyten aus Lithiumsalzen und einer Mischung aus organischen Lösungsmitteln und verschiedenen Zusätzen getränkt.

Im Gegensatz zur Standard-Graphitanode kann die Kathode aus sehr unterschiedlichen Übergangsmetalloxiden verschiedenster Zusammensetzung bestehen. Diese Zusammensetzung hat unmittelbaren Einfluss auf Kosten, Sicherheit, Leistung und anderer Parameter der Batterie und muss beim Recycling entsprechend berücksichtigt werden.
Recyclingtechnologie steht noch am Anfang
Trotz großer Fortschritte und intensiver Suche steht die Recyclingtechnologie noch sehr am Anfang. Viele Unternehmen sind dabei, ihre Prozesse zu optimieren, um Umweltbelastungen zu verringern, die Ausbeute an Recyclingmaterial zu erhöhen, die Prozesse großtechnisch anwendbar zu machen und den wirtschaftlichen Wert zu steigern.
Die wichtigsten Technologien lassen sich in drei Kategorien unterteilen:
- direktes Recycling,
- Pyrometallurgie,
- Hydrometallurgie.
In einigen Fällen werden auch pyrometallurgische und hydrometallurgische Verfahren kombiniert. Wie in der Abbildung unten dargestellt, beginnt der industrielle Recyclingprozess in der Regel mit Sortierung, Entladung, Deaktivierung und mechanischer Zerlegung der Batterien und anschließender magnetischer Trennung der Materialien. Manche Unternehmen beschränken sich dabei auf die Herstellung sogenannter Schwarzmasse (black mass), die dann zur pyro- oder hydrometallurgischen Gewinnung der Wertstoffe weitergereicht wird. Diese Schwarzmasse enthält die Metalloxide der Kathode, das Graphit der Anode und die Stromableiter. Sowohl Kunststoffe und Stahl des Batteriegehäuses als auch Elektrolyt und Separator wurden bereits vorher abgetrennt.

Beim direkten Recycling bleiben Struktur und Eigenschaften der Elektrode größtenteils intakt, wodurch mehrere energieintensive und kostspielige Verarbeitungsschritte vermieden werden. Gleichzeitig ist in diesem Verfahren die Menge an recyceltem Lithium und an Übergangsmetallen maximal (Grafik unten). Derzeit wird das direkte Recycling hauptsächlich für Produktionsabfälle bei der Herstellung von LCO und LFP-Kathodenmaterialien eingesetzt. Bei EoL-Batterien ist allerdings der Automatisierungsgrad der Elektrodentrennung, die Gewinnung von Elektrodenmaterialien und deren Regeneration in Umfang und Volumen noch sehr begrenzt, sodass direktes Recycling nicht wirklich in Betracht kommt.
Deutlich einfacher in der Anwendung ist das pyrometallurgische Recycling. Bei dieser Art der Metallrückgewinnung wird ein Hochtemperaturofen verwendet, um die Metalloxide durch „Schmelzen“ zu Legierungen aus Co, Cu, Fe und Ni zu reduzieren. Vorteilhaft ist dieses Verfahren bei vollkommen unsortiertem Eingangsmaterial. Da der Schmelzprozess auch für die metallischen Stromkollektoren funktioniert, hat die Technik den entscheidenden Vorteil, dass sie auf ganze Zellen oder Module angewendet werden kann, ohne dass ein erster Passivier- und Sortierschritt erforderlich ist. Durch den Schmelzprozess können jedoch nur Ni, Co und Cu als Übergangsmetall-Legierungen zurückgewonnen werden. Lithium- und Graphitbestandteile gehen in der Schlacke und in den gasförmigen Abgasen verloren. Die werthaltigen Metalle können dann durch hydrometallurgische Verfahren aus den Legierungen und teilweise auch aus der Schlacke abgetrennt werden. Ein weiterer großer Nachteil der Pyrometallurgie ist, neben Materialverlust und Erzeugung giftiger Abgase, der große Energieverbrauch. Trotz dieser Nachteile bleibt die Pyrometallurgie das bislang am häufigsten verwendete Verfahren zur Extraktion hochwertiger Übergangsmetalle wie Kobalt und Nickel.
Rückgewinnnung von Lithium
Wegen der steigenden Nachfrage auch nach den sekundären Wertstoffen haben viele Unternehmen mittlerweile ein hydrometallurgisches Verfahren zur Rückgewinnung sowohl von Lithium als auch hochreiner Übergangsmetalle etabliert. Bei dieser Methode werden wässrige Lösungen verwendet, um die gewünschten Metalle aus dem Kathodenmaterial auszulaugen. Traditionell sind dies starke anorganische Säuren wie Salzsäure (HCl), Schwefelsäure (H2SO4), Salpetersäure (HNO3) und Phosphorsäure (H3PO4). Die wichtigsten Prozessgrößen sind Temperatur, Säure- und Reduktionsmittelkonzentration, Reaktionszeit und Feststoff/Flüssigkeit Verhältnis. Das bei weitem häufigste Reagenz ist H2SO4, das mit einem Zusatz von Wasserstoffperoxid (H2O2) kombiniert wird. Dabei wirkt H2O2 als Reduktionsmittel und wandelt das unlösliche Co(III) in der Oxidationsstufe +3 in das lösliche Co(II) um: 2LiCoO2 + 3H2SO4 +H2O2 → 2CoSO4 + Li2SO4 + O2↑ + 4H2O
Der Einsatz der Säuren führt zur chemischen Lösung der Wertmetalle. Anschließend kann in einer mehrstufigen Ausfällung jede Kathodenkomponente einzeln extrahiert werden. Am Ende dieses Prozesses erhält man sowohl Salze der Übergangsmetalle als auch Lithiumsalze in geeigneter Qualität für eine neuerliche Elektrodenherstellung.
Der Hauptvorteil hydrometallurgischer Verfahren liegt im reduzierten Energieverbrauch durch niedrige Prozesstemperaturen, eine hohe Effizienz bei der Rückgewinnung aller werthaltigen Metalle und eine gute Anwendbarkeit auf unterschiedlichste Elektrodenmaterialien. Eine wesentliche Herausforderung bei der Hydrometallurgie ist jedoch die starke Abhängigkeit von der Vorbehandlung der Materialien, insbesondere der Notwendigkeit, das Kathodenpulver für die Auslaugung vorher abzutrennen. Die Verarbeitungsbedingungen und -kosten können je nach den in den Vorbehandlungsschritten eingesetzten Technologien enorm variieren.
Die vom EU-Umweltrat im Rahmen der EU-Batterieverordnung vorgeschlagenen Ziele sollen eine nachhaltigere Nutzung von Batterien entlang der gesamten Wertschöpfungskette in der EU sicherstellen. Dies führt zu erheblichen Investitionen in neue Recyclingkapazitäten und -technologien unter Einbeziehung gemeinsamer Anstrengungen von Industrie und Forschung. Infolgedessen haben sich bereits zahlreiche F&E-Konsortien gebildet, in denen Partner aus EU-Ländern ihre Anstrengungen zur Verbesserung bestehender und zur Entwicklung neuer Technologien zum Batterierecycling bündeln.
Entwicklung des LIB-Recyclings am KIT
Das Karlsruher Institut für Technologie (KIT) ist an drei Konsortien zum Batterierecycling maßgeblich beteiligt. Das LiBinfinity-Projekt konzentriert sich auf ein ganzheitliches Konzept für das Recycling von LIBs unter Verwendung energiearmer mechano-hydrometallurgischer Prozesse mit verbesserten Recyclingraten. Sieben Partner aus Forschung und Industrie werden diese Konzepte von der Logistik bis hin zur Wiederverwendung des recycelten Materials im Lebenszyklus der Batterie entwickeln. Die im Rahmen dieses Projekts entwickelten Methoden sollen dann vom Labor- in einen industrierelevanten Maßstab übertragen werden. Zu den Partnern von LiBinfinity gehören das KIT, Mercedes-Benz, Daimler Truck, Primobius, SMG Group, LICULAR, die TU Clausthal und die TU Berlin. Die Aufgabe des KIT in diesem Konsortium ist die Analyse der recycelten Materialien im Hinblick auf ihre Eignung für die Herstellung neuer Batterien. Die wichtigste Komponente werden Kathodenmaterialien sein, da diese die Effizienz, Zuverlässigkeit, Lebensdauer und Kosten von Batterien weitgehend bestimmen. Das Bundesministerium für Wirtschaft und Klimaschutz (BMWK) fördert LiBinfinity für vier Jahre, beginnend im Juli 2022, mit knapp 17 Mio. EUR. Davon gehen rund 1,2 Mio. EUR an das KIT.
Ein weiteres Konsortium wurde im September 2022 für vier Jahre im Rahmen des neuen Horizon Europe Program mit dem Titel ‚Rhinoceros‘ gegründet (GA No 101069685) und wird von der Europäischen Climate, Infrastructure and Environment Executive Agency (CINEA) mit 8,9 Mio. EUR finanziert. Die Bemühungen von 16 Partnern aus neun verschiedenen Ländern konzentrieren sich auf die Entwicklung und Verbesserung wirtschaftlich und ökologisch tragfähiger Verfahren für die Wiederverwendung, Wiederverwertung, Aufbereitung und das Recycling von EoL-LIBs und deren Demonstration in einem industriell relevanten Umfeld. Mit Partnern wie Technalia (ES), Accurec (DE), Hydrometal (BE), Eco Recycling (IT), Arkema (FR), TES Recupyl (FR), Watt4Ever (BE), Leitat (ES), VITO (BE), KIT (DE), Technische Universität Chalmers (SE), Universität Agder (NO), Sapienza Universität Rom (IT), PNO (BE), Levertonhelm (UK) und Ford (TR), wird Rhinoceros Prozesse entwickeln, die mit einem intelligenten Sortier- und Demontagesystem und dem Wiederzusammenbau von noch funktionsfähigen Batterien für Second-Life-Anwendungen beginnen. Falls die Wiederverwendung von LIBs nicht mehr möglich sein sollte, wird ein Recyclingweg für alle Komponenten verfolgt, der den Materialkreislauf schließen soll. Durch Produktqualifizierung soll Rhinoceros die direkte Herstellung von Hochleistungselektrodenmaterialien zu wettbewerbsfähigen Kosten aus dem Batterierecycling demonstrieren. Mit Mitteln in Höhe von 400.000 EUR wird das Institut für Angewandte Materialien – Energiespeichersysteme (IAM-ESS) am KIT ein neu entwickeltes und patentiertes reaktives Mahlverfahren (High-Energy-Ball-Milling) zur Gewinnung von Lithium aus Schwarzmasse einsetzen. Dieser innovative Ansatz wird die Effizienz bei der Rückgewinnung wertvoller Materialien aus LIB-Abfällen und deren Umwandlung in Feststoffe in Batteriequalität deutlich erhöhen. Diese Methode hat sich bereits im Labormaßstab als wirksam erwiesen und soll nun in größerem Maßstab angewandt und auf ihre wirtschaftliche Durchführbarkeit geprüft werden.

Gewinnung von Lithium aus Erzen und Solen
Im Verbundprojekt LiCORNE (GA No 101069644) bearbeitet das IAM-ESS zwei weitere Themen mit Recyclingbezug. Das von CINEA mit 6,8 Mio. EUR finanzierte Projekt startete im Oktober 2022 für vier Jahre und zielt darauf ab, eine erste vollständige Li-Lieferkette in Europa zu etablieren. An diesem Konsortium sind insgesamt 16 Partnern aus zehn Ländern beteiligt: Technalia (ES), ECM Lithium (AT), EnBW (DE), ÉS Géothermie (FR), VITO (BE), SINTEF (NO), Fraunhofer ICT (DE), Nationale Technische Universität Athen (GR), Delft University of Technology (NL), KIT (DE), AdMiRIS (GR), PNO (BE), UMICORE (BE), SQM (CL) und Levertonhelm (UK). Während der vier Jahre sollen die Grundlagen für eine Erhöhung der europäischen Kapazitäten zur Verarbeitung und Veredelung von Li gelegt werden. Das Lithium soll hierfür aus Erzen, Solen, Abraum und nicht spezifikationsgerechten Batteriekathodenmaterialien in Batteriequalität gewonnen werden. Mit Mitteln in Höhe von 630.000 EUR wird das KIT sowohl Arbeitspakete für die elektrochemische Extraktion von Li aus kontinentalen und geothermischen Solen und desorbierten Li-Lösungen bearbeiten als auch die mechanisch-chemische Extraktion von Lithium aus Produktionsresten von Batterien untersuchen. Die bei der Batterieproduktion anfallenden Reste in Form von nicht spezifikationsgerechten Batteriekathodenmaterialien sind eine bedeutende Quelle von Wertstoffen, die mittelfristig recycelt werden müssen und können je nach Prozessentwicklung des Unternehmens bis zu 30 % der Produktion ausmachen.
Große Marktchancen für das Batterierecycling
Verglichen mit der weltweiten Produktion von LIBs gibt es derzeit nur eine geringe Zahl von Unternehmen, die sich um das Recycling von Produktionsresten oder Altbatterien kümmert. Glaubt man den Vorhersagen über die Anzahl der in den Verkehr gebrachten Batterien, wird deren Recycling in wenigen Jahren einen erheblichen Marktanteil ausmachen. Während sich die industrielle Umsetzung der LIB-Recyclingtechnologie noch in einem relativ frühen Stadium befindet, werden von Forschungseinrichtungen, wie z.B. dem KIT, ständig neue technische Entdeckungen und Verbesserungen gemacht und immer mehr Recyclingunternehmen nehmen die Herausforderung einer wirtschaftlichen Umsetzung an. Die gemeinsamen Anstrengungen von Wissenschaft und Industrie unterstützen die schnell wachsende Recyclingindustrie, um Ressourcen zu schonen und letztlich für globale Nachhaltigkeit zu sorgen.
Autoren: Oleksandr Dolotko, wissenschaftlicher Mitarbeiter IAM-ESS, Michael Knapp, stellvertretender Direktor IAM-ESS, Helmut Ehrenberg, Institutsleiter, Institut für Angewandte Materialien (IAM-ESS), Karlsruher Institut für Technologie (KIT)