Druckluft, die sich gewaschen hat
B. Braun Avitum Saxonia setzt auf ölfreie, wassereingespritzte Schraubenkompressoren mit Wärmerückgewinnung von ALMiG.
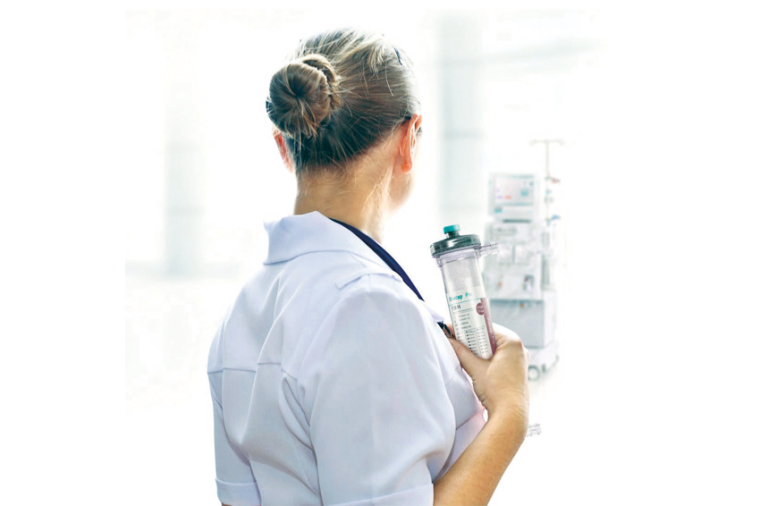
„Der Dialysator spielt in der Dialysetherapie von Patienten und Patientinnen mit Niereninsuffizienz eine zentrale Rolle. Er fungiert als „künstliche Niere“ und übernimmt wichtige Funktionen des natürlichen Organs.“, erklärt Dirk Hagen. Er ist Leiter Facility Management bei B. Braun Avitum Saxonia am Standort Dresden im Werk Radeberg, das mit rund 600 Mitarbeitern und Mitarbeiterinnen der größte Arbeitgeber im Ort ist. Die B. Braun Avitum Saxonia gehört seit 2004 zu B. Braun Melsungen und zählt zu den Weltmarktführern in der Herstellung von Dialysefilter. Neben Radeberg bilden die Werke im benachbarten Wilsdruff und Berggießhübel den Standort Dresden.
„Patienten und Patientinnen mit Niereninsuffizienz müssen drei bis viermal pro Woche für mehrere Stunden zur Dialyse. Dort werden mit Hilfe des Dialysators durch verschiedene physikalische Prozesse sowohl Gifte aus dem Stoffwechsel als auch überschüssiges Wasser aus dem Blut entfernt“, führt Hagen weiter aus. Dazu wird das Blut der Patienten durch bis zu 15.000 Hohlfasern im Dialysator geleitet, deren Wände aus einer dünnen semipermeablen Membran bestehen. Diese besitzt passgenaue Porengrößen, durch die die Giftstoffe und überschüssiges Wasser entfernt und essenzielle Blutbestandteile zurückgehalten werden. Für das Wohlbefinden der Patienten und Patientinnen sind dabei die Leistungsfähigkeit und die Blutverträglichkeit der Dialysatoren entscheidend. Je biokompatibler die Materialien des Dialysators sind und je schärfer essenzielle von toxischen Stoffen im Blut getrennt werden können, umso effektiver ist die Dialysetherapie. Die Hightech-Fasern fertigt der Hersteller in Berggießhübel, die Montage der Dialysatoren erfolgt im benachbarten Radeberg.
Absolut ölfreie Luft
Ohne Druckluft läuft in Radeberg nicht viel: Der Energieträger versorgt die pneumatischen Regelungen, treibt Zylinder an und steuert Ventile – Anwendungen, bei denen eine hohe Druckluftqualität gefordert ist, da in Reinräumen produziert wird. „Wir setzen Druckluft auch für die Nassdichteprüfung der Dialysatoren nach der Montage ein. Und weil die Dialysatoren durch das Verfahren dabei nass werden, müssen wir sie anschließend mit Druckluft trocknen“, beschreibt Hagen zwei typische Beispiele. „In diesen Fällen muss die Druckluft frei von Öl und Keimen sein sowie äußerst partikelarm.“ Für die unterschiedlichen Qualitäten stehen dem Werk verschiedene Druckluftnetze zur Verfügung.
„Bis 2017 haben wir für die Drucklufterzeugung öleingespritzte Kompressoren eingesetzt“, erzählt Hagen. „Um die Druckluft ölfrei zu halten, hatte jede Anlage eine eigene Aufbereitungskette aus Zyklonenabscheider, Vorfilter, Trockner, Nachfilter und Aktivkohlefilter. Dabei bestand trotzdem immer das Risiko einer Kontamination.“ Das wollte der Hersteller komplett ausschließen. Als dann noch das Thema Energieeffizienz im Unternehmen immer wichtiger wurde, sahen sich die Verantwortlichen verschiedene Konzepte diverser Anbieter an. Überzeugen konnte schließlich Almig Kompressoren aus dem schwäbischen Köngen in der Nähe von Stuttgart.
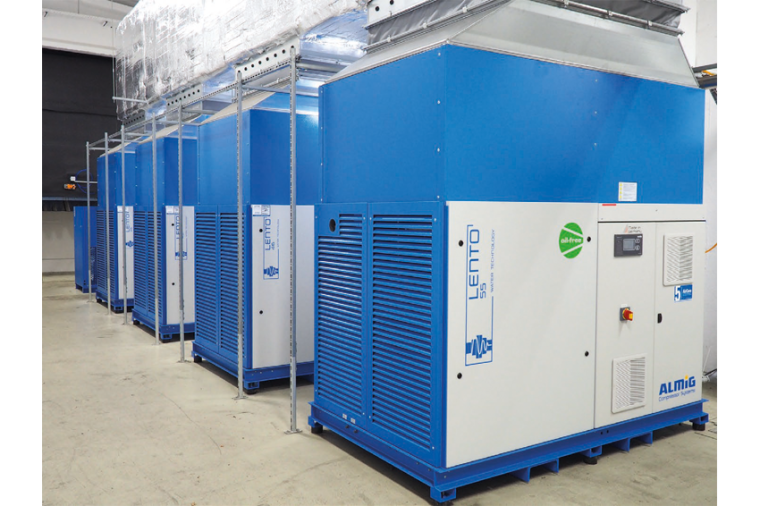
Uwe Herrmann ist Geschäftsführer der KFA Drucklufttechnik aus Zwenkau südlich von Leipzig. Mit seiner Firma bietet er Wartung und Service sowie Projektmanagement und Verkauf von Kompressoren an. Er ist zudem Vertriebspartner von Almig. „In einem ersten Gespräch war schnell klar, dass wir sowohl die Druckluftversorgung als auch alle erforderlichen Komponenten aus einer Hand liefern können und der Kunde somit nicht mit verschiedenen Anbietern zusammenarbeiten muss“, erläutert Herrmann und geht mit Dirk Hagen voran zum Kompressorraum. „Wir haben ein Energiebilanzierungssystem aufgebaut. Damit können wir sowohl den Druckluftverbrauch als auch die Stromaufnahme messen“, beschreibt Herrmann. Die Software analysiert die Ergebnisse und erstellt verschiedene Simulationen. Dazu werden gezielt Kompressoren ausgetauscht, bis der Experte das für den Kunden energetisch optimale Ergebnis erzielt. Die Messungen fanden sowohl in Schwachlastzeiten als auch unter Vollauslastung statt. Nach eingehender Analyse empfahl der Experte die wassereingespritzten Schraubenkompressoren Lento 46 von Almig mit einem Volumenstrom von 8,6 m3/min. Die Anlage kann in der Stunde bis zu 600 m3 Druckluft bereitstellen. Um den Druckluftbedarf abzudecken, kamen bis dahin drei Maschinen dieser Baureihe zum Einsatz.
Genug Platz für Erweiterung
Die bisherigen Anlagen waren überall im Werk verteilt. Die neue Druckluftstation sollte an einem zentralen Platz aufgestellt werden. Dafür trennte B. Braun Avitum Saxonia in der Halle einen Bereich für einen Raum ab, der groß genug ist, um die Druckluftstation bei Bedarf zu erweitern. Vom Spatenstich bis zum Einschalten vergingen gerade mal drei Monate.
Die Kompressoren laufen auffallend ruhig. Seit Sommer 2020 befindet sich nun auch eine vierte Maschine im Raum, eine Lento 55 mit einem Volumenstrom von 8,19 m3/min, die in der Stunde bis zu 600 m3 Druckluft bereitstellen kann. „Wir sind in den vergangenen Jahren gewachsen, und damit nahm auch der Bedarf an Druckluft weiter zu“, berichtet Hagen. „Wir arbeiten hier rund um die Uhr an sieben Tagen die Woche. Damit es unter keinen Umständen zu einem Ausfall der Druckluft kommen kann, haben wir uns entschlossen, in eine weitere Maschine als Redundanz zu investieren.“
Niedrige Drehzahl, lange Lebensdauer
Die Lento-Anlagen weisen deutlich geringere Wartungskosten im Vergleich zu alternativen Technologien auf, wie etwa die trockenlaufenden Schraubenkompressoren. „Das ist hauptsächlich durch ihren einfachen Aufbau bedingt“, beschreibt Almig-Experte Herrmann. „Die Verdichterstufen arbeiten bei wassereingespritzten Schraubenkompressoren mit vier- bis fünffach geringerer Drehzahl als die trockenlaufende Variante. Das wirkt sich positiv auf die Lebensdauer der Lager und somit auf die Betriebssicherheit aus.“ Wasser besitzt zudem im Vergleich zu Öl eine sehr viel bessere Wärmeaufnahmekapazität. „Wir haben bei diesen Kompressoren sehr niedrige Verdichtungsendtemperaturen von deutlich unter 60 °C. Der Prozess ist nahe an der isothermen Verdichtung, das sorgt für einen besseren Wirkungsgrad und damit für eine höhere Wirtschaftlichkeit“, erklärt Herrmann.
Überzeugen konnte auch die Drehzahlregelung. Damit kann das Werk auf den wechselnden Bedarf an Druckluft reagieren. Die Kompressoren produzieren immer die Menge, die gerade benötigt wird – und verbrauchen damit auch nur die entsprechende Menge an Energie. Im Leerlauf benötigen Standard-Kompressoren ohne Drehzahlregelung etwa 25–40 % der Energie, die unter Volllast aufgenommen wird – ohne dabei Druckluft zu produzieren. Die Last-Leerlauf-Regelung eines Standardkompressors in Verbindung mit einem schwankenden Druckluftbedarf verursacht deshalb teure Leerlaufzeiten. Indem Schraubenkompressoren gleicher Größe zum Einsatz kommen, ist eine gleichmäßige Auslastung der Anlagen durch ständigen Grundlastwechsel möglich. Da sich die Maschinen immer im optimalen Drehzahlbereich befinden, sind sowohl der Energiebedarf als auch die Geräuschemission geringer.
„Von Haus aus sind die Steuerungen mit einem Bilanzierungs-Monitoring-System ausgestattet und haben einen Webserver“, erläutert Herrmann. „Darüber können wir alle relevanten Daten online auslesen – z. B. das Laufverhalten der vergangenen Betriebstage oder -wochen, wie stark die Kompressoren ausgelastet sind und wann die nächste Wartung ansteht.“ Zusätzlich zeichnet er die verbrauchte Luftmenge und den Energieverbrauch auf. „Wenn wir merken, dass sich das Betriebsverhalten erheblich verändert, können wir sofort reagieren“, sagt Hagen. „Mit den alten Maschinen hatten wir durch die übergeordnete Steuerung einen Netzdruck von etwa 8 bar. Die Energierelevanz konnten wir in der Gesamtleistung um 1,5 bar senken.“ Bei einer Antriebsleistung der Anlagen von 80–135 KW ist das eine Reduktion um 7 % – ein wichtiger Schritt, um CO2 einzusparen. Das findet auch das Bundesamt für Wirtschaft und Ausfuhrkontrolle (BAFA). Mit Herrmanns Unterstützung konnte das Werk in Radeberg beim Bundesamt Fördergelder beantragen. Ein weiterer triftiger Grund für das Unternehmen, warum sich die Investition in die neuen Anlagen gelohnt hat.
Doch auch wenn der Lento-Kompressoren optimal mit niedrigen Temperaturen arbeiten, einen Großteil der eingesetzten Energie wandeln sie in Wärme um. Damit diese nicht einfach verpufft, sind die Anlagen ab Werk mit einem integrierten Wärmerückgewinnungssystem ausgestattet. „Wir nutzen diese Wärme, um unser Lager in den kalten Monaten zu heizen“, sagt Hagen und zeigt nach oben an die Decke. Dort wird über ein Rohr die warme Luft in die Halle geblasen.
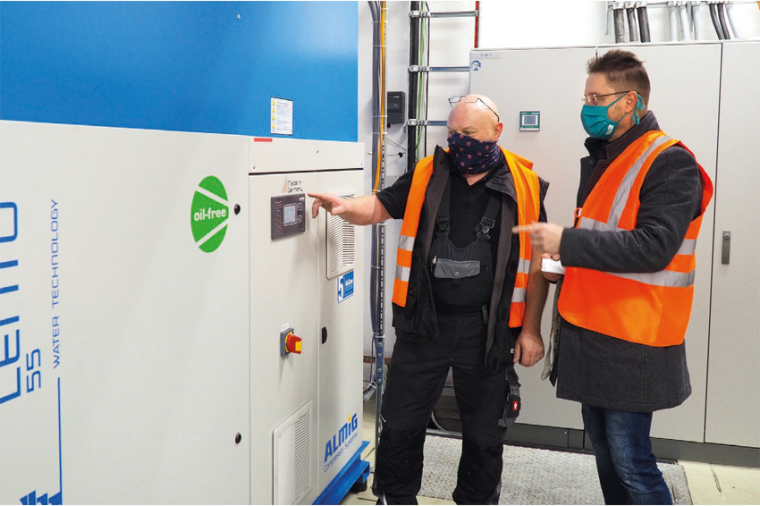
Immer frisches Wasser
Doch besonders überzeugte die Verantwortlichen von B. Braun Avitum Saxonia das Prinzip der gewaschenen Druckluft, wie es bei den wassereingespritzten Lento-Schraubenkompressoren zum Einsatz kommt. „Die Druckluft ist sauberer als die zur Verdichtung angesaugte Frischluft, weil die darin enthaltenen Fremdbestandteile durch das Kreislaufwasser wirksam ausgewaschen werden“, erläutert Herrmann. Das haben mehrere unabhängige renommierte Institute bestätigt – unter anderem Fresenius.
Dazu ist in der Lento-Anlage ein Kältetrockner integriert, der ein wesentlicher Teil der Wasseraufbereitung ist. „Der Kompressor wird bei der Inbetriebnahme mit normalem Leitungswasser befüllt“, beschreibt der Druckluftexperte. „Das angefallene Kondensat wird am Kondenstableiter des Kältetrockners gesammelt und als Frischwasser in den internen Kühlkreislauf zurückgeführt.“ Im Schnitt wird einmal pro Schicht auf diese Weise die komplette Wassermenge getauscht. Die Anlage arbeitet somit immer mit frischem Wasser. Eine aufwendig installierte Wasseraufbereitung fällt weg. „Das so produzierte Frischwasser ist kalkfrei. Viren, Bakterien oder Algen haben keine Chance. Es kann ohne Aufbereitung in die Kanalisation eingeleitet werden“, sagt Herrmann. „Vor kurzem wurde ich gefragt, was passiert, wenn der Kompressor Coronaviren ansaugt.“ Der Almig-Experte zieht seine Maske zurecht: „Allein die Temperatur des Kompressors würde sämtliche Viren schon im Verdichtungsprozess vernichten.“
B. Braun Avitum Saxonia hat mit den vier Kompressoren von Almig auch in Hochlastphasen immer genügend Druckluft parat und ist zudem für weiteres Wachstum gerüstet. „Wir erhalten damit genau die Qualität an Druckluft, die wir benötigen. Sie ist sauberer, als die Luft, die wir einatmen“, sagt Hagen.
Der Autor
Ralph Jeschabek, Marketingleiter, Almig