Effizient Energie sparen mit modernen Spalttöpfen in magnetgekuppelten Pumpen
Mit den steigenden Energiekosten und dem dringenden Bedarf zur Reduzierung von CO₂-Emissionen wird die Energieeffizienz in industriellen Prozessen immer wichtiger. Magnetgekuppelte, dichtungslose Pumpen mit nicht-metallischen Spalttöpfen bieten eine innovative und bewährte Lösung zur Reduktion von Energieverlusten und ermöglichen erhebliche Einsparungen. Erfahren Sie, wie diese Technologie nicht nur die Umwelt schont, sondern auch Kosten reduziert, und welche Mythen um sie auf den Prüfstand gehören.
Autor: Ralf Schienhammer, Sales Director Pumps & Projects, Klaus Union
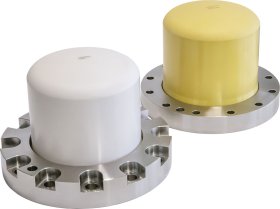
Der erste Schritt hin zu einer energieeffizienteren Flüssigkeitsförderung war und ist heute noch die Energieeffizienz der Pumpenantriebe zu erhöhen. Für Elektromotoren sind immer höhere Wirkungsgrade gefordert, um aktuelle und zukünftige Vorschriften zu erfüllen (ohne Berücksichtigung des Ressourcenbedarfs, da zur Erreichung derer immer mehr Kupfer benötigt wird). Für das Beispiel eines typischen 45-kW-2-Pol-Motors gelten folgende Mindestwirkungsgrade:
- IE2: 92,9 %
- IE3: 94,0 %
- IE4: 95,0 %
Gemäß diesen Anforderungen und unter der Voraussetzung, dass die Pumpe so ausgelegt werden kann, dass der Motor unter oder nahe der Volllasst läuft sowie die Pumpe das ganze Jahr über 24 Stunden am Tag in Betrieb ist, würde die Differenz zwischen einem IE2- und einem IE3-Motor etwa 4.965 kWh betragen, während die Differenz zwischen einem IE3- und einem IE4-Motor etwa 4.414 kWh betragen würde.
Die EAA-Website gibt folgende aktuelle CO2-Äquivalente für das Jahr 2021 an: ein durchschnittliches Äquivalent für alle 27 europäischen Mitgliedstaaten von 275 g CO2 e/ kWh, wobei einige stark industrialisierte Länder deutlich höhere Werte aufweisen (Deutschland 402 g CO2 e/kWh, Niederlande 418 g CO2 e/ kWh) und andere natürlich deutlich niedriger liegen (Frankreich 67 g CO2 e/ kWh oder Schweden mit nur 9 g CO2 e/ kWh). Der durchschnittliche Strompreis für Nicht-Haushaltskunden in der EU wurde für die zweite Jahreshälfte 2022 auf 0,21 EUR/kWh festgelegt, wobei auch hier je nach Land eine große Bandbreite besteht. Wenn wir diese Zahlen verwenden, erhalten wir folgende Ergebnisse für einen 45-kWMotor, der das ganze Jahr über mit Spitzenlast betrieben wird: Der Einbau eines IE4-Motors anstelle eines IE3-Motors spart also im günstigsten Fall 927,15 EUR und etwa 1,2 t CO2-Äquivalente pro Jahr.
Inhalt:
- Der einfachste Schritt – direktes Handeln
- Ein Schritt weiter
- Mythos 1: Dichtungslose Pumpen sind weniger effizient
- Mythos 2: Dichtungslose Pumpen haben mehr Verschleißteile
- Mythos 3: Gleitlager sind für niedrige Viskositäten nicht geeignet
- Mythos 4: Gleitlager können Feststoffe nicht vertragen
- Mythos 5: Dichtungslose Pumpen sind empfindlich gegenüber Bedienungsfehlern
- Mythos 6: Mehraufwand für den Einsatz in explosionsgefährdeten Bereichen
- Die Technologie kann nicht für jede Anwendung die ideale Lösung sein
- Ralf Schienhammer
Der einfachste Schritt – direktes Handeln
Unternehmen haben viel Zeit und Geld in die Modernisierung der installierten Elektromotoren investiert und dabei eine oftmals viel einfachere und wirkungsvollere Möglichkeit, die Energieeffizienz ihrer dichtungslosen Pumpen zu verbessern, außeracht gelassen: Die Spalttopftechnologie. Durch den Einsatz nicht-metallischer Spalttöpfe aus Hochleistungs-Industriekeramik kann der Wirkungsgrad von dichtungslosen Pumpen bei kleinen Hydrauliken um fünf bis 10 % sowie bei größeren Hydrauliken um 10 bis 20 % gesteigert werden. Die Technologie hat sich seit mehr als 25 Jahren in der Praxis bewährt und wird für anspruchsvollste Anwendungen eingesetzt.
Nicht-metallische Spalttöpfe sind nicht elektrisch leitend. So übertragen sie den Strom ohne Wirbelstromverluste und arbeiten verlustfrei, was sich direkt auf den Stromverbrauch auswirkt. Dadurch können kleinere und effizientere Motoren eingesetzt werden, was sich wiederum direkt auf die bestehenden Pumpenanlagen auswirkt, ohne dass neues Equipment installiert werden muss. Im Hinblick auf das zuvor genannte Beispiel ergeben derart große Einsparpotenziale, dass es keine Rolle spielt, auf welcher IE-Motorklasse die Zahlen basieren: 17,7 t CO2 oder 13.554,90 EUR Stromkosten pro Jahr.
Ein Schritt weiter
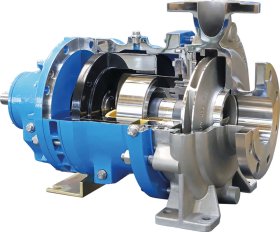
- Es wäre jedoch ein Irrtum, die Anwendbarkeit der nicht-metallischen Spalttopftechnologie nur auf Anlagen zu beschränken, die bereits heute dichtungslos sind. Dichtungslose Pumpen machen immer noch eine große Minderheit der installierten Pumpen aus, obwohl sie im Vergleich zu mechanisch abgedichteten Pumpen signifikante Vorteile bieten, wenn man den gesamten Pumpenbestand in jeder Art von Anlage bzw. Installation betrachtet:
- Gleitringdichtungen haben eine begrenzte Lebensdauer – sind die Dichtungen verschlissen, müssen die Pumpen entsprechend zur Wartung abgeschaltet werden.
- Dichtungen weisen stets eine gewisse Leckage auf, sei es in die Atmosphäre (bei einfachwirkenden Dichtungen) oder in das Produkt (bei doppeltwirkenden Dichtungen). Das bedeutet wiederum einen Verlust an Produkt oder Produktqualität und eine Verunreinigung der Umwelt durch das Produkt oder die Sperr- bzw. Quenchflüssigkeit.
- Doppeltwirkende und/oder gequenchte Dichtungen erfordern zusätzliche Betriebsmittel wie Sperrflüssigkeiten, Dampf, Stickstoff oder Sauerstoff, deren Vorbereitung und Bereitstellung Energie und zusätzliche Ausrüstung erfordern. Eine naheliegende Lösung wäre die Verwendung von dichtungslosen Pumpen (magnetgekuppelt oder mit Spaltrohrmotor). Jedoch werden diese aufgrund einiger weit verbreiteter Mythen und Vorurteile noch immer nicht als mögliche Lösung in Betracht gezogen.
Mit den technischen Entwicklungen der letzten Jahrzehnte gibt es jedoch für nahezu jeden Punkt, für den dichtungslose Pumpen heute noch kritisiert werden, praxiserprobte Lösungen.
Mythos 1: Dichtungslose Pumpen sind weniger effizient
Dies ist ein typischer Kritikpunkt und zugleich einer der komplexesten, da der Wirkungsgrad einer Pumpe von verschiedenen Faktoren abhängt:
- Hydraulischer Wirkungsgrad der Pumpe
- Wirkungsgrad des Antriebs
- Einfluss der Leistungsübertragung
Dazu gehört auch die Annahme, dass eine dichtungslose Pumpenhydraulik einen schlechteren Wirkungsgrad als die abgedichtete Hydraulik habe. Doch bei den meisten Herstellern ist die verwendete Hydraulik bei abgedichteten und dichtungslosen Ausführungen die gleiche – ohne nennenswerte Energieauswirkungen. Hinsichtlich der Effizienz ist festzuhalten, dass bei einer Magnetkupplungspumpe die gleichen Normmotoren verwendet werden wie bei einer mechanisch abgedichteten Pumpe. Es gibt somit keinen Unterschied. Der elektrische Wirkungsgrad von Spaltrohrmotorpumpen hängt hingegen von der Qualität des Elektromotors und damit vom Hersteller ab, da sie keine Normmotoren verwenden können.
Ein weiterer Kritikpunkt bezieht sich auf den Nutzen von Hilfs- bzw. Betriebsmitteln, der durch Übertragungsverluste wieder aufgefressen werde. Üblicherweise bezieht sich diese Behauptung auf die Übertragungsverluste, die mit dem metallischen Spalttopf einhergehen, oder es wird sogar noch auf die Flüssigkeitsreibung bei Dichtungslosenpumpen im Bereich des Spalttopfes bzw. Spaltrohrs hingewiesen.
Zunächst zum letzten Punkt: Mit einem sorgfältig kontrollierten Flüssigkeitsspalt im Spalttopfinnenraum kann der Flüssigkeitswiderstand für Kreiselpumpen praktisch eliminiert werden. Selbst bei hohen Viskositäten, bei denen üblicherweise Verdrängerpumpen zum Einsatz kommen, können die Reibverluste durch die Flüssigkeit durch eine gewissenhafte Betrachtung und ggf. Anpassung des Flüssigkeitsspaltes und der Pumpendrehzahl minimiert werden.
Ersteres trifft seit 25 Jahren nicht mehr zu, insbesondere nicht für magnetgekuppelte Pumpen. Nichtmetallische Spalttöpfe, idealerweise aus Hochleistungs-Industriekeramik, ermöglichen eine verlustfreie Leistungsübertragung. Mit modernen Magnetantriebstechnologien können je nach Anwendung und anderen Faktoren Leistungen von bis zu 1 MW übertragen werden, sodass dem Einsatz von Magnetkupplungen in Bezug auf Größe, Pumpenart oder Anwendung praktisch keine Grenzen mehr gesetzt sind.
Mythos 2: Dichtungslose Pumpen haben mehr Verschleißteile
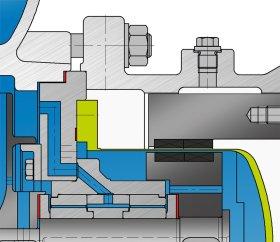
Auch hier hängt es von der Konstruktion der Pumpe und den Kundenspezifikationen ab. Eine magnetgekuppelte Blockpumpe, die bei sehr niedrigen bis sehr hohen Temperaturen (-200 bis +400 °C) zuverlässig eingesetzt werden kann, hat nicht mehr, sondern weniger Verschleißteile als eine mechanisch abgedichtete Pumpe. Bei der Blockausführung wird der Magnettreiber direkt auf die Welle des Standardelektromotors gesetzt. Somit gibt es weniger Verschleißteile, da sie ohne dynamisches Dichtelement, ohne Kupplung und ohne zusätzlichen Lagerträger auskommt. Der Wartungsaufwand sowie die Kosten werden im Vergleich zu mechanisch abgedichteten Pumpen signifikant reduziert. Die Gleitlager sind ohnehin wartungsfrei, sofern die Pumpe ordnungsgemäß und in sauberen Flüssigkeiten betrieben wird oder die Lager entsprechend ausgewählt wurden.
Mythos 3: Gleitlager sind für niedrige Viskositäten nicht geeignet
Das war lange Zeit der Fall. Aber mit heute verfügbaren zuverlässigen High-Tech-Materialien ist es möglich, selbst Flüssiggase mit Viskositäten unter 0,1 cP selbst mit den größten Hydrauliken problemlos zu fördern. Lösungen für hochviskose Flüssigkeiten gibt es schon seit Jahrzehnten und der Betrieb mit niedriger Viskosität ist selbst ohne Hilfsmittel zur Kühlung und/oder Spülung unproblematisch.
Mythos 4: Gleitlager können Feststoffe nicht vertragen
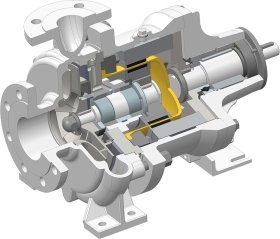
Entscheidend ist eine offene und ehrliche Kommunikation mit dem Pumpenlieferanten. Moderne Werkstoffe ermöglichen extrem hohe Belastungen ohne Beschädigung der Gleitlager. Die heute verfügbaren hochverschleißfesten Spalttöpfe aus Industriekeramik verbessern die Festigkeit weiter und ermöglichen Anwendungen, bei denen traditionelle dynamische Wellendichtungen an ihre Belastungsgrenzen kommen. Darüber hinaus ermöglichen Magnetfilter bei Bedarf sogar die Förderung von Flüssigkeiten, die eisenhaltige Feststoffe wie Eisenoxide enthalten.
Mythos 5: Dichtungslose Pumpen sind empfindlich gegenüber Bedienungsfehlern
Neben der Art der Pumpe ist auch hier eine offene und ehrliche Kommunikation zwischen Kunde und Hersteller entscheidend. Die heutige Technologie nicht-metallischer Spalttöpfe ermöglicht Gleitlager, die weit über den normalen Betriebsbereich hinaus agieren können und einen Trockenlauf über eine überraschend lange Zeit überstehen. Klaus Union hat die Trockenlauffähigkeit für mehr als eine Stunde ohne nachteilige Auswirkungen auf die Lagerleistung nachgewiesen. Das konnten Anwender im laufenden Betrieb bestätigen.
Mythos 6: Mehraufwand für den Einsatz in explosionsgefährdeten Bereichen
Auch hier gilt: Mit dem Einsatz nicht-metallischer Spalttöpfe ist das nicht mehr der Fall. Bei Verwendung eines solchen Spalttopfes kann eine magnetgekuppelte Pumpe ohne zusätzliche Instrumentierung in einem explosionsgefährdeten Bereich betrieben werden, sofern der Anwender den Betrieb innerhalb der vorgegebenen Grenzen sicherstellt.
Die Technologie kann nicht für jede Anwendung die ideale Lösung sein
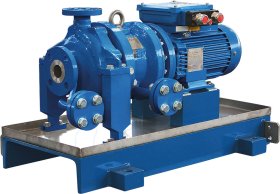
Doch es gibt viele Anwendungen, bei denen ihre Fähigkeiten zur Verbesserung der Effizienz und zur Verringerung des Wartungsaufwands auch heute noch verkannt werden. Das mag auch daran liegen, dass sich Ingenieure und das Wartungspersonal an die Situation gewöhnt haben, wie sie sich in den vergangenen Jahrzehnten entwickelt hat oder dass sie in der Vergangenheit durch falsch ausgewählte Pumpen gebrandmarkt wurden.
Doch dichtungslose Pumpen sowohl Kreisel- als auch Verdrängerpumpen, die mit nicht-metallischen Spalttöpfen aus Hochleistungs-Industriekeramik ausgestattet sind, bieten enorme monetäre wie energetische Einsparpotenziale. Direkt, indem eliminierte Wirbelstromverluste den Bedarf an Instrumentierungen obsolet machen und indirekt, da sie den Wartungsaufwand und die Anzahl der Verschleißteile reduzieren und die Zuverlässigkeit im Vergleich zu herkömmlichen Pumpendichtungen erhöhen.
Sie können für verflüssigte, natürliche Gase, kryogenes CO2, hochgefährliche chemische und petrochemische Produkte und darüber hinaus für schwer abzudichtende Produkte wie Vakuumrückstände, Teer, Bitumen und Asphaltene sowie Polymere eingesetzt werden. Dabei kann der Betreiber mit Ausnahme der Stromversorgung weitgehend auf Hilfsmittel verzichten. Das vereinfacht die Anlagen und senkt sowohl die Investitions- als auch die Betriebs- und Wartungskosten.
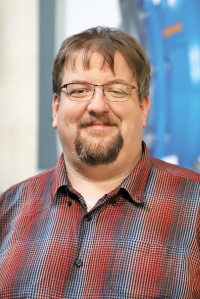
Ralf Schienhammer
Sales Director Pumps & Projects, Klaus Union
"Der Schlüssel ist hier die gezielte Anwendung bewährter, zuverlässiger und robuster Technologien."