Explosionsrisiken präzise erkennen
Durch die spezielle Beprobung entfällt eine aufwendige und fehleranfällige Gasaufbereitung, sodass der CO.Pilot weniger störanfällig und wartungsfreier ist.
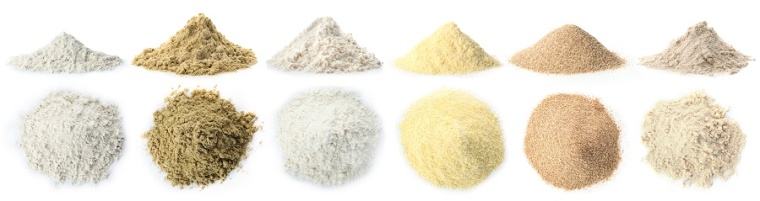
Das Thema „Explosionsschutz“ ist für Anlagenbetreiber und Maschinenhersteller allgegenwärtig, sobald es um die Bearbeitung oder den Transport von brennbaren und/oder explosionsfähigen Stäuben geht. Im Gegensatz zur weitverbreiteten Annahme, wonach erhöhte Explosionsrisiken nur bei Gasen besteht, können auch bei brennbaren Stäuben durchaus enorme Kräfte freigesetzt werden.
Um das Explosionsrisiko bei der Handhabung brennbarer Feststoffe und Stäube zu minimieren, werden im Folgenden die Voraussetzungen für eine Explosion und die jeweiligen Staub-Charakteristiken beschrieben.
Grundsätzlich wird hierbei das so genannte Zündfünfeck betrachtet: Um eine Explosion in einer Produktionsanlage oder einer Maschine zu erzeugen, müssen folgende Voraussetzungen erfüllt sein:
- Brennstoff
- (brennbarer Staub oder Gase),
- Sauerstoff,
- Staubverteilung,
- Zündquelle (z. B. Funken, heiße Oberflächen, Elektrostatik),
- geschlossener Behälter.
Wird eine der oben genannten Voraussetzungen eliminiert, wurde so gesehen bereits Explosionsschutz praktiziert. Ist dies jedoch nicht zu jeder Zeit und jedem Zustand im Betrieb möglich, bleibt die Explosionsgefahr bestehen, was die Einteilung explosionsgefährdeter Bereiche in Zonen und darüber systematisch abgeleitete Schutzmaßnahmen erfordert. Gerade Trocknungsprozesse sind von der Lebensmittel- und Getränkeindustrie bis hin zur Agrartechnik angesiedelt, um Ausgansstoffe, Vor-, Zwischen- und Endprodukte für eine vereinfachte Verarbeitung, Lagerung, einen effizienteren Transport und eine längere Haltbarkeit vorzubereiten. Der Feuchtigkeitsentzug und die hohen Temperaturen sorgen jedoch für ein gesteigertes Brand- und Explosionsrisiko. Kommt es in solchen, meist groß ausgelegten, Trocknungsanlagen zu einem Brand und/oder zu einer Explosion, ist die Situation nicht nur für Anlagen, Maschinen und Betrieb, sondern auch für die Menschen vor Ort höchst riskant.
Speziell die Betreiber von Sprühtrocknern kämpfen mit einer besonderen Zündquellenart: mit Glimmnestern die bei zu starken Materialanbackungen zu einer Selbstentzündung führen können. Durch eine nicht optimale Trocknung des Materials und der anfangs hohen Feuchtigkeit im Produkt, kommt es zu Anbackungen, welche von außen durch immer mehr feuchtes Material isoliert werden. Die hohen Temperaturen sorgen für ein stetiges Erhitzen der Anbackungen bis hin zu einer vielstufigen chemischen Reaktion, ausgehend von Aminosäuren (aus Peptiden oder Eiweißen) und reduzierenden Kohlenhydraten unter Wasserabspaltung. Sie wird als Maillard-Reaktion bezeichnet und setzt Hitze frei, die aufgrund der isolierenden Schicht der Verklumpung nicht abgeführt werden kann. Der Vorgang steigert sich, bis es schlussendlich zu einer Selbstentzündung kommt.
Solche Anbackungen können sowohl an den Düsen der Sprühtrockner als auch an deren Innenwand entstehen. Kommt es zu einer Fehlfunktion der Düse können Tropfen hinab in das Fließbett fallen und dort weitere Verklumpungen erzeugen. Wird das Stadium eines Glimmnests erreicht, kann dieses die explosionsfähige Atmosphäre im inneren des Trockners oder der nachgeschalteten Maschinen zünden.
Prävention
Wie kann solchen in der Praxis häufig anzutreffenden Anlagenzuständen vorgebeugt werden? Alles beginnt mit dem Faktor Mensch, demnach also entsprechend geschultem Personal für den jeweiligen Prozess. Ebenso bedarf es einer optimalen Prozesssteuerung, um Verklumpungen gar zu vermeiden. Doch ohne präzise und zuverlässige Informationen/Messungen ist dies selbst für Spezialisten kaum möglich. Als Indikator für einen reibungslosen und somit sicheren Prozess dienen heutzutage die Luftfeuchtigkeit und ein Beiprodukt von Selbstentzündungen – Kohlenmonoxid (CO). Problematisch ist jedoch, dass kombinierte Messsysteme nicht klar zwischen diesen beiden Indikatoren unterscheiden können und somit die Messung ungenau wird.
Der Rembe CO.Pilot macht genau diese genaue Unterscheidung präzise möglich! Durch einen permanenten Abgleich erfasster Daten mit einer Datenbank von hinterlegten Referenzgasen, die als Fingerabdrücke der selektierten Gase dienen, ist eine einmalige Echtzeitkontrolle und somit eine permanente Überprüfung auf Messgenauigkeit möglich. Gleichzeitig wird mit Hilfe der Echtzeit-Fingerprint-Analyse die Querempfindlichkeit zu anderen im Messspektrum liegenden Gasen ausgeschlossen, die bei handelsüblichen Gasanalysatoren anzutreffen ist.
Zur zuverlässigen Messung des Betriebszustandes, werden Proben im sehr hohen Vakuum aus allen relevanten Zu- und Abluftkanälen des Trockners gesaugt. Aus den daraus absolut gemessenen Werten der einzelnen Messpunkte, bildet Rembe den Delta-CO-Wert. Dieser Wert ist die mathematische Differenz aus dem CO-Gehalt der Abluft – zum CO-Gehalt der Zuluft. Somit werden nur Ereignisse erkannt, die tatsächlich im Prozess entstehen. Störfaktoren, die dem Prozess von außen zugetragen werden, können hiermit ausgeblendet werden.
Der speziell entwickelte Auswerte-Algorithmus ermöglicht einen Abgleich der gemessenen Zu- und Abgasluftwerte in Echtzeit und erlaubt es als erstes System am Markt die Alarmgrenzen und Gaslaufzeiten der einzelnen Messstellen ohne Verzögerungen an die verschiedenen Luftdurchsätze des Trockners anzupassen. Die Ratio-Verhältnisse der verschiedenen Zu-Lüfte und das Gleitzeitverhalten werden über die Software ausgeglichen und entsprechend in der SPS berechnet.
Wird also ein Anstieg der Kohlenmonoxid Konzentration durch eine Selbstentzündung im Prozess erkannt, kann unverzüglich mit Gegenmaßnahmen eingegriffen werden.
Fazit
Was bedeutet das für die betriebliche Praxis? Durch die spezielle Beprobung fällt eine aufwändige und fehleranfällige Gasaufbereitung weg, sodass der CO.Pilot weniger störanfällig und wartungsfreier ist. Das Messverfahren ermöglicht es, auf wiederkehrende Kalibrierungen zu verzichten. Aufgrund der präzisen Messtechnik und den daraus reproduzierbaren Ergebnissen können Fehlalarme und Stillstände vermieden werden. Kombiniert mit der Feuchtigkeitsmessung kann der Trocknungsprozess optimal gesteuert werden, wodurch die Energieeffizienz der Anlage erheblich erhöht wird.
Autoren:
Alexander Kemmling, Sales Executive Explosion Prevention, Key Accounts DACH;
Gerrit Fikse, Senior Consultant Explosion Safety
Global Sales Explosion Safety;
Marcus Kendik, Senior Consultant Explosion
Prevention, Global Sales Explosion Safety
__________________
Das Unternehmen
Rembe Safety+Control bietet Kunden branchenübergreifend Sicherheitskonzepte für Explosionsschutz und Druckentlastung in Anlagen und Apparaturen. Sämtliche Produkte werden in Deutschland gefertigt und erfüllen die Ansprüche nationaler und internationaler Regularien. Das ingenieurtechnische Know-how basiert auf fast 50 Jahren Anwendungs- und Projekterfahrung. Die kurzen Abstimmungswege des inhabergeführten Familienunternehmens erlauben schnelle Reaktionen und kundenindividuelle Lösungen vom Standardprodukt bis zur Hightech-Sonderkonstruktion.