Leistungsprüfungen an Flüssigkeitskühlern
Gerade in jüngster Zeit gewinnt die Frage der Energieeffizienz durch den Anstieg der Energiepreise zusätzlich massiv an Fahrt. Der Industrie kommt bei der Einsparung von Energie neben den Privathaushalten, dem Gewerbe und dem Verkehrssektor eine besondere Bedeutung zu. Welche Bedeutung hat die Energieeffizienz von Prozesskühlern für die chemische Industrie? Und wie wird sie gemessen?
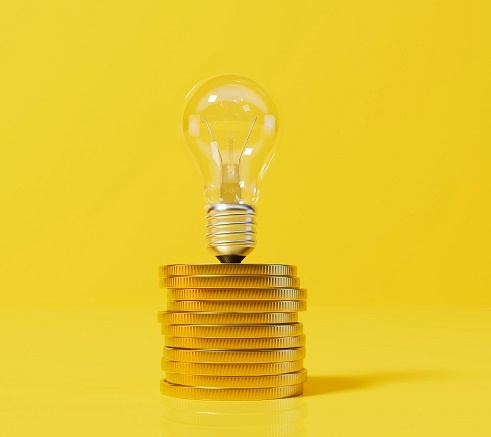
Die Kühlung von Prozessen ist in der chemischen Industrie oft unerlässlich für effiziente Betriebsabläufe und ist eine maßgebliche Voraussetzung für die Betriebssicherheit. Geräte und Werkzeuge werden mittels Kühlmedien vor Überhitzung und daraus entstehenden Schäden geschützt und stellen eine kontinuierliche, unterbrechungsfreie Herstellung von Produkten sicher. Je nach gefordertem Temperaturniveau werden verschiedene Technologien eingesetzt, um die Kühlmedien rückzukühlen, bspw. Trockenkühler, Kühlturme und Flüssigkeitskühler (sog. Chiller). Während die beiden erstgenannten Technologien bei eher höheren Vorlauftemperaturen verwendet werden, lassen sich mit Chillern auch Temperaturen weit unter dem Gefrierpunkt realisieren. Um diese tiefen Temperaturen zu erzeugen, wird Sole, meist aus Ethylenglykol und Wasser, als Medium verwendet. Im Gegensatz zu Trockenkühlern und Kühltürmen, welche allein mit Ventilatoren und Pumpen betrieben werden, erbringen Chiller ihre Kühlleistung durch einen kältetechnischen Kreisprozess.
Die zu kühlende Sole wird dabei in einem Wärmeübertrager (Verdampfer) durch verdampfendes Kältemittel bei niedrigem Druck auf die Zieltemperatur gebracht. Das verdampfte Kältemittel wird von einem Verdichter angesaugt und verdichtet, um sodann in einem weiteren Wärmeübertrager (Verflüssiger, im Beispiel luftgekühlt) bei höherer Temperatur und höherem Druck wieder verflüssigt zu werden. Durch das Expansionsventil wird der Druck des Kältemittels wieder auf das ursprüngliche Niveau gesenkt und das Kältemittel wieder in den Verdampfer geleitet. Der Kreislauf schließt sich. Naturgemäß ist der Energiebedarf dieses Kreisprozesses höher als bei Trockenkühlern und Kühltürmen.

Energieeffizienzkennwerte: EER und SEPR
Auf dem Markt sind Chiller für jegliche Kälteleistungen und Temperaturbereiche erhältlich. Die Energieeffizienz (Energy Efficiency Ratio, kurz EER), definiert als Quotient aus Kühlleistung und elektrischer Leistungsaufnahme, wird von den Herstellern in technischen Datenblättern angegeben. Bei außen aufgestellten, luftgekühlten Geräten – der Einfachheit halber sollen hier nur diese betrachtet werden – ist der EER maßgeblich von der Temperatur abhängig, bei der das Kältemittel wieder verflüssigt wird. So ergibt sich je nach Außentemperatur ein anderer EER. Je geringer der Druckunterschied – und der daraus resultierende Temperaturunterschied – zwischen dem verdampfenden und dem kondensierenden Kältemittel ist, desto effizienter kann die Kältemaschine arbeiten. Um Chiller über einen breiten Temperaturbereich unterschiedlicher, über das Jahr hinweg auftretender Betriebsbedingungen besser miteinander vergleichen zu können, wurde der Kennwert Seasonal Energy Performance Ratio (SEPR) eingeführt. Nachzulesen sind die Grundlagen für die Messung des SEPR in der DIN EN 14825.
Labormessungen von Chillern
Die zu prüfenden Chiller werden im Labor festgelegten Betriebsbedingungen ausgesetzt. Bei luftgekühlten Chillern liegen die Temperaturen bspw. bei 5, 15, 25 und 35 °C Umgebungstemperatur.
Gleichzeitig wird davon ausgegangen, dass bei sinkenden Außentemperaturen auch die Kühllast aufseiten der Produktionsanlage fällt – von 100 % der Maximallast bei 35 °C auf 80 % bei 5 °C. Die Chiller müssen bei geringeren Außentemperaturen somit eine geringere Kühlleistung aufbringen und gleichzeitig steigt die Effizienz aufgrund des geringeren Druckunterschiedes zwischen Verdampfungs- und Kondensationsseite. Bei der Messung werden nun an jedem Betriebspunkt die Kühlleistung und die elektrische Leistungsaufnahme dokumentiert, sodass sich der EER berechnen lässt. Der SEPR wird ermittelt, indem der EER für jede Temperaturstufe mit einer festgelegten jährlichen Stundenanzahl gewichtet wird. Für nicht gemessene Temperaturstufen, also z.B. bei 4 °C und darunter oder zwischen 6 und 14 °C, wird der EER durch Inter-/Extrapolation bestimmt. Schlussendlich werden die unterschiedlich gewichteten EER zum SEPR zusammengefasst. Nach den Messungen im Labor steht damit ein Kennwert zur Verfügung, der die Energieeffizienz des Gerätes bei unterschiedlichsten, im Jahresverlauf auftretenden Betriebsbedingungen abbildet.
Die jeweilige Gewichtung der Temperaturstufen ist dabei nicht repräsentativ für einen beabsichtigten Aufstellungsort – hier sind konkrete Rechnungen auf Basis der örtlichen Jahrestemperaturstunden und lokaler Gegebenheiten wie z. B. schattige oder sonnige Aufstellungsorte erforderlich. Allerdings können anhand der SEPR verschiedene Geräte unter dem Aspekt der Energieeffizienz verglichen werden, unter Beachtung eines realistischen Betriebs.

Gravierende Abweichungen möglich
In der EU-Verordnung 2016/2281 ist für unterschiedliche Chiller-Leistungsklassen je ein SEPR-Mindestwert vorgegeben. Bei den oben besprochenen luftgekühlten Geräten und einer Nennkälteleistung von unter 400 kW wird beispielsweise ein SEPR von mindestens 5 gefordert: Mit 1 kWh elektrischer Energieaufnahme müssen also im Jahresmittel mindestens 5 kWh Prozesswärme abgeführt werden. Bei niedrigeren Werten der Jahresenergieeffizienz darf das Gerät auf dem europäischen Markt nicht verkauft werden. Der SEPR wird von den Herstellern selbst ermittelt; eine Verpflichtung zu unabhängigen Messungen besteht nicht. Hier kann es unter Umständen zu Abweichungen kommen, die auch gravierende Ausmaße annehmen können. Für Kunden gilt es daher, auf Gütesiegel, wie z.B. „Eurovent Certified Performance“, zu achten oder gezielt nach Prüfberichten aus unabhängigen Laboren zu fragen.
Ausstattung als Anhaltspunkt
Auch die technische Ausstattung der Flüssigkeitskühler kann Anhaltspunkte geben: Geräte mit stufenloser Leistungsregelung der Verdichter sind in der Regel effizienter als Geräte mit Stufenregelung oder ganz ohne Regelung. Die erstgenannten Geräte mit stufenloser Leistungsregelung lassen sich kontinuierlich der aktuellen Lastanforderung anpassen, während ungeregelte Geräte lediglich aus- und wieder eingeschaltet werden können. Ähnliches gilt für die Regelung der Verflüssigerventilatoren: Ungeregelte Ventilatoren arbeiten in der Regel druckgesteuert und schalten ein, wenn das gasförmige, verdichtete Kältemittel eine bestimmte Temperatur und den entsprechenden Druck überschreitet.
Dadurch sinken Temperatur und Druck und die Ventilatoren schalten wieder aus. Die schwankenden Drücke im Kältekreislauf führen dazu, dass sich kein stationärer Betriebszustand einstellen kann, in dem der Kältemittelkreislauf optimal arbeitet. Ein weiteres Bauteil mit maßgeblichem Einfluss auf die Energieeffizienz ist das Expansionsventil.
Moderne elektronische Expansionsventile basieren zwar auf demselben Regelkreis wie klassische thermostatische Expansionsventile, sind aber in der Lage, die zur Verfügung stehende Verdampfungsstrecke optimal auszunutzen.

Mehrkosten durch abweichende Herstellerangaben
Was reale Leistungsabweichungen gegenüber den Herstellerangaben für den Betreiber bedeuten, soll ein kleines Rechenbeispiel veranschaulichen. Angenommen ein Industrieprozess benötigt ganzjährig (24 Stunden an 365 Tagen im Jahr) eine Kühlleistung von 100 KW. Ein entsprechender luftgekühlter Flüssigkeitskühler darf laut EU-Verordnung im Jahresschnitt nicht mehr als 20 kW elektrische Leistung aufnehmen. Bei einem Strompreis von 30 ct/kWh ergeben sich Kosten von gut 52.000 EUR. Die Energieeffizienz ist als Quotient aus Kühlleistung und elektrischer Leistungsaufnahme definiert. Sollte das Gerät nun eine Jahresenergieeffizienz von 20 % weniger aufweisen, führt das zu zwei möglichen Szenarien: Wird die Kühlleistung nicht erreicht, drohen im schlimmsten Fall Produktionsausfälle. Wird hingegen die Kühlleistung trotz der geringeren Effizienz erreicht, ist die elektrische Leistungsaufnahme deutlich höher. Im betrachteten Beispiel steigen die jährlichen Kosten auf 63.000 EUR an, es ergeben sich also Mehrkosten von über 10.000 EUR. In großen Chemieparks werden deutlich höhere ganzjährige Kühlleistungen benötigt – das Rechenbeispiel lässt sich entsprechend übertragen. Es kann deshalb durchaus finanziell lohnend sein, bei größeren Investitionsvorhaben die Leistung der anzuschaffenden Geräte bei festgelegten Bedingungen unabhängig nachmessen zu lassen.
Autoren: Timo Reisner, stellv. Technischer Leiter der Prüfstelle für Kälte-, Klima- und Lüftungstechnik,
Maike Strebel, Sachverständige der Prüfstelle für Kälte-, Klima- und Lüftungstechnik, TÜV Nord Systems