Optimierung von Produktionsprozessen: Kosten senken und Emissionen reduzieren
Das Verständnis und die Beherrschung von Produktionsprozessen sind unerlässlich, um Kosten zu senken und Emissionen zu reduzieren. Eine strukturierte Herangehensweise, bei der der Gesamtprozess in Unterprozesse untergliedert wird, ermöglicht eine effektive Prozessanalyse. Daten aus dem Prozessleitsystem werden gesammelt, aufbereitet und visualisiert, um sie gemeinsam mit dem Kunden zu bewerten. Moderne Simulationswerkzeuge helfen, das hydraulische Verhalten präzise zu bewerten und Optimierungspotentiale zu identifizieren. Ein Beispiel zeigt, wie Energieeinsparungen und Prozessoptimierungen in einem Stahlwerk erreicht wurden.
Autor: Lukas Zapf, Entwicklungsingenieur, Prof. Dr. Jaberg & Partner
Effektive Prozessanalyse und numerische Strömungssimulation zur Verbesserung industrieller Anlagen
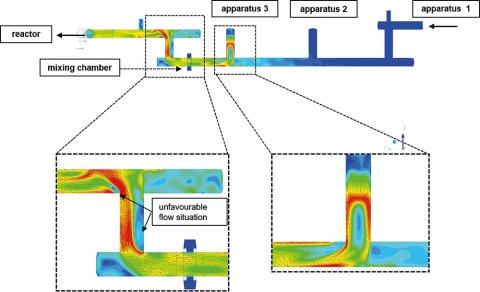
Das Verständnis und die Beherrschung von Produktionsprozessen sind gerade in der heutigen Zeit unerlässlich, insbesondere wenn es darum geht, Kosten zu senken und Emissionen zu reduzieren.
Auf den ersten Blick mag dies zwar selbstverständlich erscheinen, doch in der Praxis zeigt sich schnell, dass Produktionsprozesse eine oft unterschätzte Komplexität aufweisen.
Für eine effektive Prozessanalyse ist eine strukturierte Herangehensweise erforderlich, bei der der Gesamtprozess, je nach Größe und Komplexität, in einzelne Unterprozesse untergliedert wird. Zu Beginn werden Daten aus dem Prozessleitsystem gesammelt, aufbereitet und visualisiert, um sie gemeinsam mit dem Kunden zu bewerten. Durch diese Methode können die Einflüsse von Betriebsparametern und die Wechselwirkungen zwischen den Teilprozessen besser nachvollzogen werden, was eine wichtige Grundlage für weitergehende Untersuchungen darstellt.
Für die detaillierte Analyse von Anlagenteilen oder Einzelkomponenten kommen moderne Simulationswerkzeuge zum Einsatz, mit denen das hydraulische Verhalten präzise und zuverlässig bewertet werden kann. Ein anschauliches Beispiel für eine solche Prozessanalyse bietet die umfassende Untersuchung an einem komplexen Erzeugungsprozess in einem Stahlwerk, wobei der Fokus neben dem Aufzeigen von Energieeinsparungspotenzial durch konstruktive Maßnahmen an Rohrleitungen und Verfahrenstechnischen Apparaten auch auf der Analyse der Prozessführung lag.
Inhalt:
- Effektive Prozessanalyse und numerische Strömungssimulation zur Verbesserung industrieller Anlagen
- Erste Schritte in der Prozessanalyse
- Analyse der Sammelleitung und Optimierung der Strömungssituation
- Benefits einer umfassenden Prozessanalyse
- Untersuchung der Abgasstrecke und Optimierung der Partikelabscheidung
- Lukas Zapf
Erste Schritte in der Prozessanalyse
Der Gesamtprozess wurde in Abstimmung mit dem Auftraggeber in technisch sinnvolle Einzelabschnitte unterteilt, welche anschließend mittels numerischer Strömungssimulation in verschiedenen Modellierungstiefen untersucht wurden. Prozessparameter aus dem Leitsystem wurden ausgewertet und aufbereitet, sodass sie als Randbedingung, wie auch als Validierungsgrößen für die Simulationen verwendet werden konnten. Da es sich bei der Anlage um einen teils Jahrzehnte alten Bestand handelte, welcher über die Zeit mehrfach verändert bzw. erweitert wurde, waren 3D CAD-Daten relevanter Anlagenbauteile nur spärlich vorhanden. Deshalb erfolgte zunächst eine CAD-Modellierung dieser Komponenten anhand gering verfügbarer technischer Zeichnungen in Kombination mit Fotos und Vorortbesichtigungen.
Analyse der Sammelleitung und Optimierung der Strömungssituation
Im ersten Betrachtungsabschnitt der Anlage wurde eine Sammelleitung untersucht an dessen Beginn Gas aus drei zyklisch alternierend zu- und wegschaltbarer Apparate einströmt. In weiterer Folge wird das Medium in einer Mischkammer durch Beimengung desselben Mediums mit jedoch unterschiedlicher Temperatur auf das für den späteren Prozess gewünschte Temperaturniveau gebracht. Das gemischte Fluid strömt anschließend durch ein Doppel-T-Stück in Richtung eines Reaktors. Erste Simulationen zeigten hohe lokale Fluidgeschwindigkeiten und ungünstige Strömungssituationen in T-Stücken und Bögen, welche zu einem erhöhten Druckverlust in der Sammelleitung führten (siehe Abb. 1). Mithilfe der umfassenden Simulationsmodelle konnten die in den Einzelkomponenten auftretenden Verluste genau bestimmt werden, was für die darauffolgende Optimierung unerlässlich war. Durch eine konstruktive Umgestaltung der Rohrleitungskontur kann zum einen der Druckverlust erheblich reduziert und zum anderen die Vermischung des Mediums verbessert werden. Die parallel zu den Strömungssimulationen durchgeführte Analyse der Prozessdaten ergab ein Energieeinsparungspotenzial in der zyklischen Schaltung der drei Apparate. Die Prozesssicherheit darf durch Optimierungsmaßnahmen keinesfalls negativ beeinflusst werden.
Benefits einer umfassenden Prozessanalyse
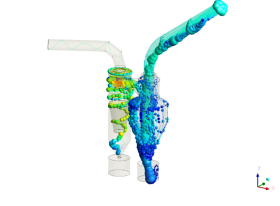
Diese systematische Analyse ermöglicht nicht nur eine präzise Bewertung komplexer Prozessabläufe, sondern auch die Identifikation eventuell vorhandener Schwachstellen und die zielgerichtete Erarbeitung von Optimierungsmaßnahmen, die zur Reduktion von Kosten und Emissionen sowie zur Steigerung der Effizienz und Zuverlässigkeit industrieller Anlagen beitragen.
Unumgänglich für eine effiziente Systemanalyse ist das Zusammenwirken geeigneter Simulationswerkzeuge und das tiefgehende Verständnis für die prozesstechnische Problemstellung.
Untersuchung der Abgasstrecke und Optimierung der Partikelabscheidung
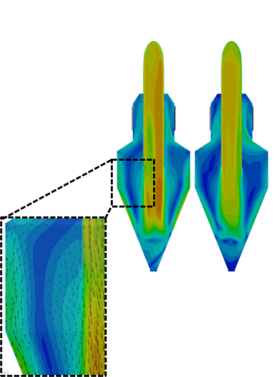
Der nächste Untersuchungsabschnitt widmete sich der Rohrleitungsstrecke nach dem Reaktor, in welcher Abgas gesammelt, gereinigt und in einen anderen Prozessabschnitt übergeführt wird. Der Fokus lag dabei auf den zur Partikelabscheidung verbauten Staubsäcken und Zyklonabscheidern. Hier wurde neben einer einphasigen Strömungssimulation eine Mehrphasenströmung bestehend aus Rauchgas und Partikeln untersucht. Dabei wurde auf die beim Auftraggeber vorhandenen Messdaten der Staubbeladung im Rauchgas und dessen Korngrößenverteilung zurückgegriffen. Mithilfe dieser Daten und modernster Simulationssoftware war es möglich, die Abscheideleistungen der einzelnen Apparate genau zu bestimmen. Eine detaillierte Visualisierung der Strömung offenbarte eine hydraulisch ungünstige Auslegung des Staubsackes. Zum einen bildet sich im Abscheideraum eine ausgeprägte Strömungswalze aus (siehe Abb. 2 und Abb. 3), was die Sedimentation der Partikel erschwert, zum anderen wirbelt das mit relativ hoher Geschwindigkeit einströmende Rauchgas bereits abgeschiedene Partikel wieder auf. Besonders ungünstig kam hinzu, dass die Austragung der abgeschiedenen Stäube nicht kontinuierlich, sondern zyklisch erfolgte. Dabei wurde dieses Aufwirbeln mit zunehmender Betriebsdauer seit der letzten Entleerung immer wirksamer und die Abscheideleistung verschlechterte sich. Auch hier konnte mit geeigneten konstruktiven Maßnahmen an der Geometrie des Abscheiders eine deutliche Verbesserung erzielt werden.
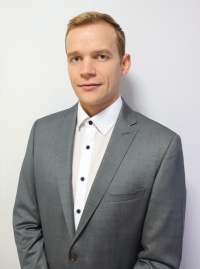
Lukas Zapf
Entwicklungsingenieur, Prof. Dr. Jaberg & Partner
© Prof. Dr. Jaberg & Partner