Acoustic Testing (AT) setzt neue Maßstäbe in der Instandhaltung chemischer Anlagen. Durch den Einsatz fortschrittlicher Sensortechnik und Datenanalyse können Betreiber frühzeitig Schäden und Fehlfunktionen von Druckbehältern erkennen. Dies ermöglicht eine gezielte und effektive Planung von Instandhaltungsmaßnahmen, das Testverfahren reduziert Prüfnebenkosten und minimiert Produktionsausfälle. Erfahren Sie, wie AT die Effizienz und Nachhaltigkeit Ihrer Anlage steigern kann.
In Chemieanlagen kommen zunehmend spezielle, z. B. piezoelektrische Sensoren zum Einsatz, die direkt am Equipment angebracht werden. Diese reagieren empfindlich auf Schallwellen und Vibrationen, die bereits durch kleinste Materialveränderungen unter Belastung entstehen. Ein wesentlicher Vorteil der Schallemissionsprüfung liegt darin, dass sie im laufenden Betrieb vorgenommen werden kann. Das Verfahren kann frühzeitig Materialermüdung oder Risse erkennen, sodass Instandhaltungsmaßnahmen gezielter und effektiver geplant werden können. Moderne Prüfsysteme bieten zudem erweiterte Diagnosemöglichkeiten: Sie erfassen nicht nur den Zustand der Anlagenkomponenten, sondern liefern auch wertvolle Informationen über veränderte Strömungs- und Mischverhältnisse sowie mögliche Ablagerungen im System.
Inhalt:
- Einsparungen durch Ersatzprüfungen
- Fallbeispiel: Herstellung von Polymerharzen
- Stillstand durch Wasserbefüllung vermieden
- Kosten für Dichtungen und deren Einbau reduziert
- Früher erkannte Materialermüdung verbessert Wartungsplanung
- Gleichzeitige Prüfung mehrerer Anlagenteile
- Integration in bestehende ZfP-Verfahren
- Verlängerte Lebensdauer von Anlagenteilen
- Erhebliche Einsparungen erzielt
- Autor: Rainer Semmler,
Einsparungen durch Ersatzprüfungen
TÜV Süd nutzt Acoustic Testing für die von der BetrSichV geforderten wiederkehrenden Prüfungen an Druckbehältern und Tanks. Als Ersatzprüfung im Rahmen eines Prüfkonzepts ersetzt AT bspw. eine visuelle Innenbesichtigung, aber auch hydrostatische Festigkeitsprüfungen. Behälter und Tanks lassen sich so ohne vorheriges Entleeren oder Befüllen mit Wasser schneller, wirtschaftlicher und risikoärmer und sogar unter betrieblichen Bedingungen beurteilen. Das reduziert die Gesamtkosten für die Betreiber. Die Ingenieurinnen und Ingenieure nutzen AT bei der Prüfung von Komponenten verfahrenstechnischer Anlagen wie Druckgeräte, Wärmetauscher sowie Maschinen. Vor allem sogenanntes Rotating Equipment ist hier bei den Maschinen gemeint. Das umfasst vor allem Pumpen, Turbinen, Kompressoren und Motoren. Mit einem einfachen Tool berechnet TÜV Süd die wirtschaftlichen Vorteile des AT gegenüber klassischen Prüfungen von Druckgeräten nach BetrSichV schon im Vorfeld.
Fallbeispiel: Herstellung von Polymerharzen
Eine Chemieanlage produziert Polymerharze für die Automobil- und Verpackungsindustrie. Sie besteht aus einer Reihe von Behältern und Reaktoren, in denen chemische Reaktionen unter kontrollierten Bedingungen ablaufen. Typische Prozesse umfassen das Erhitzen, Kühlen und Mischen von Rohstoffen unter Druck, sodass die Anlagenteile, besonders die Druckgeräte, regelmäßigen Prüfungen unterliegen. Ziel der Prüfungen ist es, strukturelle Integrität zu gewährleisten und Produktionsunterbrechungen zu minimieren. Die Betreiber haben jährlich rund 1 Mio. EUR für Prüfleistungen kalkuliert.
Stillstand durch Wasserbefüllung vermieden
Durch AT entfällt die Wasserbefüllung der Behälter, um den Prüfdruck aufzubauen. Das reduziert das Risiko von Korrosionsschäden, die durch Restfeuchte entstehen können. Zudem spart der Betreiber rund 20 % der jährlichen Prüfkosten, was etwa 200.000 EUR entspricht. Der Entfall der Trocknung nach einer hydrostatischen Prüfung verkürzt zudem die Stillstandszeiten um durchschnittlich zwei Tage. Bei einem Tagesumsatz von geschätzten 80.000 EUR bedeutet dies für die Anlage 160.000 EUR weniger Umsatzausfall.
Kosten für Dichtungen und deren Einbau reduziert
Da beim AT die Behälter nicht geöffnet werden müssen, entfallen auch die Kosten für das Austauschen und das Einsetzen neuer Dichtungen. Dies beläuft sich bei Reaktoren, die alle zwei Jahre geöffnet werden, auf etwa 25.000 EUR jährlich, was rund 2,5 % der Gesamtprüfkosten ausmacht. Gleichzeitig sinkt das Risiko von Leckagen und damit verbundener ungeplanter Stillstände, weil die Originaldichtungen belassen werden können.
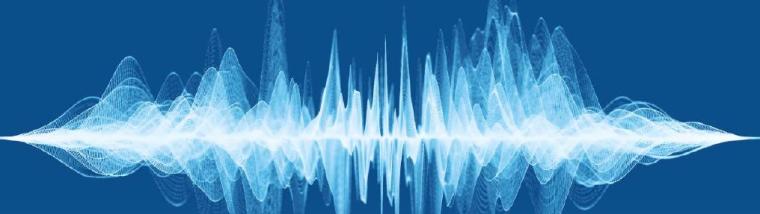
Früher erkannte Materialermüdung verbessert Wartungsplanung
Eine der Stärken des AT liegt darin, Materialschwächen wie Risse oder Korrosion im Frühstadium zu erkennen. Dadurch können Betreiber auf mögliche Schäden reagieren und Wartungsmaßnahmen gezielt planen, anstatt auf kostenintensive Notfallreparaturen zurückgreifen zu müssen. Für die Beispielanlage, in der pro Jahr durchschnittlich 50.000 EUR für ungeplante Wartungsarbeiten aufgewendet werden, bedeutet das 80 % an potenziellen Einsparungen – also 40.000 EUR weniger Kosten. Die nun nur noch gezielt geplanten und vorgenommenen Wartungen erhöhen darüber hinaus die Lebensdauer der betroffenen Komponenten, was langfristig zusätzliche Kosten spart.
Gleichzeitige Prüfung mehrerer Anlagenteile
Ein oft übersehener Vorteil von AT ist die Möglichkeit, mehrere Druckkreise gleichzeitig zu überprüfen. Im vorliegenden Fallbeispiel kann die Polymerharzanlage etwa 10 % der jährlichen Prüfkosten einsparen, indem mehrere Druckbehälter und Reaktoren gemeinsam getestet werden. Durch die gleichzeitige Prüfung lassen sich Personaleinsatz und Prüfzeiten optimieren. Die Einsparungen: rund 100.000 EUR jährlich. Da weniger Prüfpersonal benötigt wird, verkürzt sich auch die Prüfzeit erheblich und erleichtert die Planung und den Ablauf der Inspektionen.
Integration in bestehende ZfP-Verfahren
AT kann nahtlos in andere zerstörungsfreie Prüfverfahren (ZfP) integriert werden, was eine gezielte Nachprüfung erlaubt, ohne aufwändige und kostenintensive Prüfprozeduren. So können Anlagenteile, bei denen Auffälligkeiten festgestellt wurden, im Rahmen der bestehenden ZfP-Verfahren weiter untersucht werden. Durch die Möglichkeit, direkt und gezielt zu überprüfen, kann die Anlage im Beispiel weitere 5 % der jährlichen Kosten einsparen, was 50.000 EUR entspricht. Diese integrative Prüfstrategie reduziert den Ressourcenverbrauch und trägt zu einer nachhaltigen Anlageninstandhaltung bei.
Verlängerte Lebensdauer von Anlagenteilen
Das AT kann auch im laufenden Betrieb erfolgen. Dadurch entfallen alle für eine herkömmliche Prüfung notwendigen Ab- und Anfahrprozesse, die durch Druck- und Temperaturwechselvorgänge Stress auf das Material der Anlage bzw. einzelner Komponenten bewirken, was zu einer Verringerung der Lebensdauer führt. Im Fallbeispiel führt das zu einer Einsparung von etwa 5 % der jährlichen Investitionen in Ersatzteile, Material und Komponenten, was etwa 200.000 EUR umfasst, die Kosten also jedes Jahr um 10.000 EUR senkt.
Erhebliche Einsparungen erzielt
Für die Beispielanlage summieren sich die Einsparungen durch den Einsatz von AT auf insgesamt 585.000 EUR pro Jahr. Die Einsparungen betreffen allerdings nicht die Kosten für das AT, das für sich alleine betrachtet nicht günstiger ist als herkömmliche Prüfverfahren. Die Einsparungen werden – im Vergleich zu herkömmlichen Prüfverfahren – mit dem Vermeiden von Prüfnebenkosten (Vorbereitung, Nachbereitung und ggf. Entsorgungskosten einer Wasserdruckprüfung) und Produktionsausfällen erzielt. Hinzu kommt ein reduzierter Materialbedarf. Da nicht immer alle Potenziale vollständig realisiert werden, würde eine vorsichtige Kalkulation maximal 70 % ansetzen und somit auf jährlich etwa 409.500 EUR kommen.
Langfristig verbessert das nicht nur die Wirtschaftlichkeit und Verfügbarkeit, sondern auch die Nachhaltigkeit der Anlage. Gerade für Betreiber in einem wettbewerbsintensiven Marktumfeld bietet das nicht zu unterschätzende strategische Vorteile: Eine verbesserte Nachhaltigkeit lässt sich wirksam nach außen dokumentieren und kommunizieren – was Kunden immer wichtiger wird.
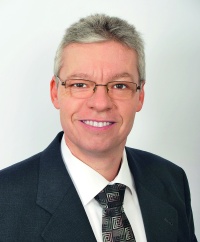
Autor: Rainer Semmler,
Process Safety Management, TÜV Süd Chemie Service