Bionische Optimierung im Druckbehälterbau
Bei der mechanischen Auslegung von chemischen Prozessapparaten sind bionische Leichtbaumethoden bisher nicht weit verbreitet. Die bionische Topologieoptimierung von Behälter-Stutzen-Verbindungen soll eine höhere Festigkeit der Geometrien bei gleichzeitig geringerem Gewicht ermöglichen. Die Ergebnisse der Optimierung ergeben mithilfe von FEM Simulationen eine Spannungsreduktion von ca. 5 %, während das Gewicht um 59,9 % verringert werden konnte. Prototypen der optimierten Geometrien werden anschließend in 3D-Druckverfahren produziert.
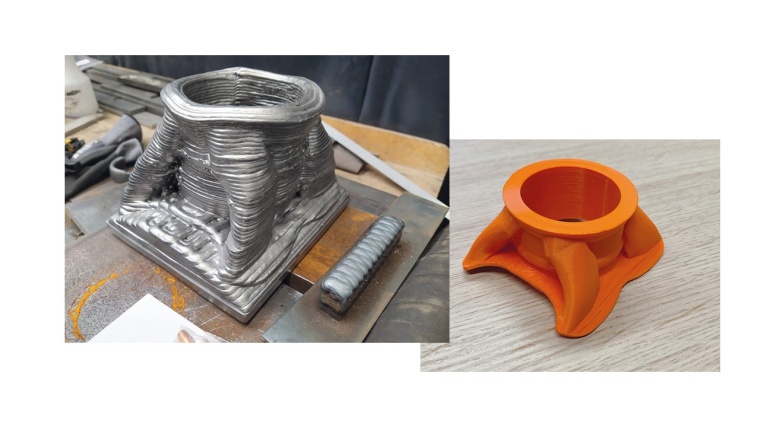
Das hohe Potenzial für Material- und Kostenreduzierung macht bionische Leichtbauweisen für den chemischen Apparatebau interessant[1]. Um bionische Strukturen im Druckbehälterbau zu etablieren, bedarf es eines neuen Herstellungsverfahrens und neuartiger bionischer Designkonzepte. Ziel des AiF-Projektes „Bionischer Druckbehälter“ (FKZ ZF4595601LL8) war es Apparateelemente, die nach bekannten Regelwerken wie den AD2000 Merkblättern ausgelegt wurden, mit bionisch optimierten Apparateelementen zu vergleichen. Um dem Design möglichst viele Freiheitsgrade zu geben, werden additive Fertigungsverfahren betrachtet.
Topologieoptimierung
Ein bekannter bionischer Optimierungsansatz ist die Topologieoptimierung, die sich am lastgerechten Wachstumsverhalten von Knochenstrukturen orientiert[1]. Das Ziel einer Topologieoptimierung ist die Identifikation einer mechanischen Struktur mit der günstigsten Materialanordnung innerhalb eines definierten Volumens unter Einhaltung von Randbedingungen. Als Randbedingungen werden dabei Lasten, Lagerungen, Bauraumgrenzen oder auch Fertigungsrestriktionen betrachtet [2]. Die Masse des Bauteils und die resultierenden von-Mises-Vergleichsspannungen im Bauteil stellen die Zielgrößen der Optimierung dar. Durchgeführt wird die Optimierung mithilfe der Berechnungssoftware ANSYS 19.1. Während der Optimierung werden gering belastete Materialbereiche iterativ entfernt, wodurch sich eine differenzierte Struktur ausbildet. Das am weitesten verbreitete Verfahren ist die Solid Isotropic Material with Penalization (SIMP) Methode [2]. Als Zielfunktion wird dabei die Minimierung der reziproken Steifigkeit des Modells verwendet und als Randbedingung eine Zielmasse vorgegeben. Als Abbruchkriterium der Optimierung wird die Konvergenz der Zielfunktion verwendet.
Anwendung der Topologieoptimierung auf Behälterstutzen-Verbindungen
Ein beispielhafter Anwendungsfall für eine Topologieoptimierung im Druckbehälterbau stellen Behälter-Stutzen-Verbindungen dar, bei denen eine Schwächung der zylindrischen Behälterwand durch das Aufbringen einer Verstärkungsscheibe kompensiert wird. Zur Untersuchung wird ein in der x,z-Ebene halbierter Zylinder mit einem Innenradius Ri = 838,2 mm, einer Wandstärke von s = 74 mm und einer Länge Lz = 2.000 mm betrachtet. Zylinderwand und Stutzen werden mit einem inneren Überdruck p = 200 bar belastet. Der Zylinder wird durch einen Stutzen mit einem Stutzeninnendurchmesser D(St,i) = 460 mm und einer Stutzenhöhe HSt = 320 mm verschwächt, sodass nach AD Merkblatt B9 eine Scheibenverstärkung ausgelegt werden muss [3].
Ergebnis der Topologieoptimierung und FEM-Simulation
Das Ergebnis der Optimierung des Stutzenbauraums mit einer angestrebten Massenerhaltung von 15 % des Bauraums ist in Bild oben dargestellt. Neben einer Hauptstruktur, die um die Stutzeninnenfläche erhalten geblieben ist, haben sich in elf Iterationsschritten am Rand des Bauraums zwei Nebenstrukturen gebildet, die insgesamt eine Masse mTopo = 222,73 kg besitzen. Somit ergibt sich eine Massenreduktion von 59,9 % gegenüber einer einfachen Scheibenverstärkung. An der Hauptstruktur zeigen sich in den Bereichen der beim Referenzbehälter auftretenden strahlenförmigen Spannungsverteilung gekrümmte Verstärkungen. Am Fuß der Struktur ist vor allem an der Stelle Material erhalten geblieben, an der sich im Behälterinneren die Maximalspannung befindet.
Neben der Gewichtseinsparung konnten auch die resultierenden Spannungen in der optimierten Geometrie bei gleichen Randbedingungen verringert werden. Die von-Mises-Vergleichsspannungen reduzierten sich auf σTopo,max = 862 MPa, was einer Verringerung um ca. 5 % im Vergleich zum scheibenverstärkten Modell bedeutet. In beiden Modellen stellt sich das Maximum an der inneren Kante der Stutzen-Verbindung ein. Wird die Massenerhaltung des Bauraums als Randbedingung der Optimierung weiter begrenzt, lässt sich die Gewichtseinsparung weiter erhöhen. Gleichzeitig kommt es jedoch zu einem Anstieg der resultierenden Spannungen.
Additive Fertigung der topologie-optimierten Strukturen
Die Fertigung der finalen Geometrien erfolgt mithilfe von additiven Fertigungsverfahren, hier im Polymer 3D-Druck im eigenen Labor und mit dem Wire Arc Additive Manufacturing (WAAM) am FEF Forschungs- und Entwicklungsgesellschaft Fügetechnik in Aachen. In der ersten Abbildung ist eine Behälter-Stutzen-Verbindung mit einem Massenerhalt von 5 % dargestellt, die mit beiden Verfahren produziert wurde. Zu erkennen sind die deutlich hervorstehenden seitlichen Strukturen, welche eine gute Spannungsverteilung auf den Behälter ermöglichen. Der Polymerdruck wird mit PLA als Werkstoff durchgeführt und zeichnet sich durch seine geringe Schichthöhe von und einer Druckzeit von vier Stunden aus. Das WAAM Verfahren verwendet einen hochfesten Stahl und benötigt trotz einer erhöhten Schichtdicke von eine Druckzeit von insgesamt acht Stunden.
Ausblick
In Zukunft können die FEM Ergebnisse mithilfe der gefertigten Prototypen validiert werden. Eine weitere Oberflächen-Nachbearbeitung der Geometrie aus hochfestem Stahl erscheint hier sinnvoll. Bisher wird die Größe der Geometrien durch die Größe des Druckbettes der Polymer- und Metall-3D-Drucker begrenzt. In Zukunft ist jedoch zu erwarten, dass eine weitere Skalierung möglich ist. Neben den bisher betrachteten Flächenlasten können bei zukünftigen Designs auch weitere Lasten z.B. durch angeschlossene Rohrleitungen berücksichtigt werden.
Referenzen
[1] Sauer A (2018) Bionik in der Strukturoptimierung: Praxishandbuch für ressourceneffizienten Leichtbau. Vogel Business Media, Würzburg
[2] Bendsøe MP, Sigmund O (2011) Topology optimization: Theory, methods, and applications, Second edition, corrected printing. Engineering online library. Springer, Berlin, Heidelberg
[3] Beuth Verlag GmbH (2010) AD 2000-Merkblatt B 9:2010-02: Ausschnitte in Zylindern, Kegeln und Kugeln
[4] FEF Forschungs- und Entwicklungsgesellschaft Fügetechnik GmbH (2021)
Autoren:
Daniel Becker, Sina Gerling, Norbert Kockmann, Technische Universität Dortmund, Fakultät für Bio- und Chemieingenieurwesen