Effektive Umsetzung von PAT für nachhaltige und effektive Prozesse
Den Wandel in der chemischen und pharmazeutischen Industrie prägen Themen wie Industrie 4.0 und Produktivität durch Vernetzung. Vor diesem Hintergrund ist die Einführung von PAT (Process Analytical Technology) zu einem festen Bestandteil von Arbeitsmethoden und Prozessentwicklung geworden.
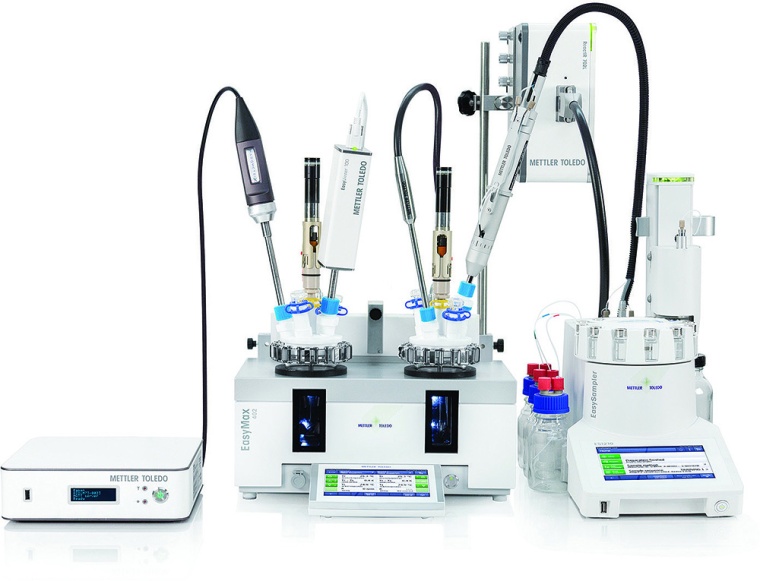
Die Covid-19-Pandemie war wohl die größte Beeinträchtigung, die die chemische und pharmazeutische Industrie je erlebt hat. Schließungen führten zu einem dramatischen Rückgang der Produktivität, da Beschäftigte zu Hause bleiben mussten und nicht essenzielle Geschäfte stillgelegt wurden. Diejenigen, die ihren Betrieb aufrechterhielten, mussten schnell neue Arbeitsmethoden finden, die die Sicherheit der Mitarbeiter gewährleisten und gleichzeitig die Produktivität aufrechterhalten.
Herkömmliche Laborversuche erfordern umfangreiche manuelle Eingriffe, so dass Mitarbeiter den vollen Arbeitstag im Labor anwesend sein müssen. Viele Labore sind jedoch an ihrer Kapazitätsgrenze, was bedeutet, dass sie aufgrund sozialer Distanzregeln gezwungen sind, mit deutlich geringerer Kapazität zu arbeiten. Die Verlagerung von Geräten oder Umstellung auf Schichtarbeit allein konnte das Produktivitätsdefizit nicht ausgleichen und gefährdete so Projekte mit hoher Priorität.
Neue Arbeitsmethoden dank Automatisierung und PAT
Glücklicherweise gab es bereits Automatisierungswerkzeuge und laborgestützte PAT, die neue Arbeitsmethoden ermöglichten. Dies zeigte sich bei einem Auftragsforschungsunternehmen (CRO), das an einem Projekt zur Verbesserung einer Molekülsynthese arbeitete. Ihr einziges Labor war aufgrund des schnellen Wachstums des Unternehmens überlastet.
Aufgrund von Beschränkungen konnten in dem Labor nur noch zwei Chemiker gleichzeitig arbeiten. Das Unternehmen plante bereits, in ein automatisiertes Reaktorsystem mit Probennahmesonde und ein sondengestütztes MID-IR-Spektrometer zu investieren – verknüpft mit einer Steuerungssoftware, die gewährleistet, dass alle Daten gespeichert und zuverlässig auf einen sicheren Server hochgeladen werden. Das Unternehmen zog die Investition vor und nahm sie umgehend in Betrieb.
Die Forscher benötigten so nur noch kurze Zeit im Labor zur Vorbereitung der Geräte und Materialien bevor sie wieder nach Hause gehen konnten. Das 18-stündige Experiment lief automatisch ab, wobei das IR-Gerät ein vollständiges Reaktionsprofil (einschließlich wichtiger Zwischenprodukte) lieferte und die automatische Sonde Proben für die Offline-Analyse der Verunreinigung sammelte. Die experimentellen Daten wurden außerhalb des Labors abgerufen und analysiert, und zwar rechtzeitig für das nächste Experiment. Durch diese Remote-Aktivität wurde das Labor entlastet, so dass andere Kollegen ihrer Arbeit nachgehen konnten.
Auf diese Weise war das CRO in der Lage, das Projekt fristgerecht abzuschließen und seinen Ruf für die termingerechte Lieferung qualitativ hochwertiger Projekte zu wahren. Dies ist kein Einzelbeispiel. Ein kürzlich erschienenes White Paper[1] zeigt, wie Unternehmen durch Investitionen in solche Technologien besser in der Lage sind, die Pandemie zu bewältigen und gestärkt aus ihr hervorgehen.
Auswirkungen von unerwarteten Störungen auf die Produktivität und mögliche Folgeszenarien.
Selbstoptimierende Prozessentwicklung
Das Paradigma der Industrie 4.0 hat die chemische Industrie durch die Neuorganisation der Ressourcen (Personal/Methoden/Ausrüstung) in allen Phasen der Prozessentwicklung erreicht. Der Einsatz neuer Technologien wie PAT liefert Informationen in Echtzeit und erschließt die Leistungsfähigkeit von Interkonnektivität, Automatisierung und Digitalisierung. Das führt zu einer effizienten chemischen Entwicklung. Industrie 4.0 passt besonders gut zu Flow Chemistry, die durch die Verbesserung der Ausrüstung, die Intensivierung der Forschung und der inhärenten Vorteile in Bezug auf Effektivität und Nachhaltigkeit zur Reife gelangt ist. Eine kürzlich durchgeführte Fallstudie veranschaulicht, wie Automatisierung, Interkonnektivität und PAT in der Flow Chemistry zur Steigerung der Produktivität eingesetzt werden können. Sagmeister et al. entwickelten eine modulare Plattform, die PAT zur automatischen Selbstoptimierung eines zweistufigen Prozesses für die Synthese des Medikaments Edaravone nutzt[2].
Die selbstoptimierende Plattform wird von einem Überwachungs- und Datenerfassungssystem (SCADA) gesteuert, welches die Sollwerte für Reaktortemperatur und Durchflussmenge berechnet. Nach dem Start der Synthese bestimmt PAT die Reagenzienkonzentrationen in Echtzeit. Diese werden vom SCADA-System verarbeitet und an den Entscheidungsalgorithmus zur Auswahl der nächsten Reaktionsbedingungen zurückgegeben. Das System führt wiederholende experimentelle Aufgaben mit iterativer Optimierung durch und gibt dem Chemiker Zeit für die Analyse und den Entwurf neuer Synthesewege.
Effizienz und Nachhaltigkeit als Zielvorgabe
Die selbstoptimierende Plattform zeigt die Fähigkeit zur automatischen Erkundung des chemischen Parameterfelds. Sie beschleunigte die Prozessoptimierung bei geringerem Einsatz von Ressourcen (Personal und Material). Sie führte zu einer Lösungsausbeute von mehr als 95 % bei gleichzeitiger Minimierung von Reagenzeinsatz, um die Nachhaltigkeit des Prozesses zu verbessern.
Die nachhaltige Produktion von Chemikalien und Pharmazeutika wird aufgrund erheblicher Einschränkungen bei Rohstoffen, Energiepreisen und behördlichen Beschränkungen für Abfall und Kohlenstoffemissionen immer wichtiger. Effiziente Prozessentwicklung muss daher die Nachhaltigkeit des Prozesses sowohl aus wirtschaftlicher als auch aus ökologischer Sicht berücksichtigen.
So wurde bspw. über die Entwicklung eines robusten, skalierbaren Prozesses berichtet, bei dem die Kinetik eines kritischen Zwischenprodukts bei der Belzutifan-Synthese mittels PAT untersucht wurde[3]. Die Prozessmassenintensität (PMI) wurde um 50 % von 63 auf 29 reduziert. Das bedeutet, dass für jedes Kilogramm des finalen Wirkstoffs nur 29 kg anstatt vorher 63 kg an Materialien benötigt wurden. Darüber hinaus wurde die Prozesszeit von durchschnittlich 8,5 Tagen auf nur 5,9 Tage reduziert, was einen Produktivitätsgewinn von 30 % bedeutet.
Um diesen bedeutenden Schritt in Richtung einer nachhaltigeren Produktion zu erreichen, wurden verschiedene PAT-gesteuerte Ansätze genutzt. Die Gruppe setzte automatisiertes Screening ein, um das beste Lösungsmittel auszuwählen und Lösungsmittelaustausch während des Prozesses zu vermeiden. Das Zwischenprodukt konnte auch direkt aus diesem Lösungsmittel kristallisiert werden, um jegliche Aufarbeitung zu vermeiden. Allerdings wurden beim Scale-up Variationen von Charge zu Charge beobachtet. Die automatisierte Probenahme mit anschließender GC- und UPLC-Analyse sowie In-situ-IR- und Raman-Spektroskopiedaten aus den Reaktionen wurden genutzt, um den Mechanismus vollständig zu verstehen und die Ursache für diese Variationen zu ermitteln. Dies unterstreicht die Notwendigkeit, so viele Daten wie möglich in einem frühen Stadium des Prozesses zu erfassen.
Selbstoptimierende Plattform: Zusammenschaltung von SCADA, Peripheriegeräten, Reaktor, PAT und Entscheidungsalgorithmus.
Hybrider Ansatz aus Experiment und Modellierung
Es wurden signifikante Änderungen in der Kinetik zwischen geschlossenen, gespülten und belüfteten Reaktionsbedingungen beobachtet, die auf den CO2-Gehalt im Reaktionsgemisch zurückgeführt wurden. Die erforderliche Stickstoffspülung wurde durch Modellierung mit Dyno-Chem-Software optimiert, und Auswirkungen von Scale-up-Faktoren wie Rührergeschwindigkeiten und Füllvolumen wurden in silico untersucht. Dieser hybride Ansatz aus Experimenten und Modellierung führte zur Entwicklung eines robusten Verfahrens, das vom Labor- über Pilot- bis hin zum kommerziellen Maßstab eingesetzt werden kann.
PAT wurde traditionell für Entwicklungen in sehr spezifischen Bereichen eingesetzt, die von individuellen Projekten getrieben wurden. Die Industrie ist jedoch dabei, Arbeitsmethoden zu ändern, um besser auf künftige Unwägbarkeiten zu reagieren und Produktivitäten zu steigern, damit Produktanforderungen erfüllt werden. Darüber hinaus müssen Produktionsprozesse aufgrund des wirtschaftlichen und ökologischen Drucks nachhaltiger werden. Eine smarte Möglichkeit, diese Herausforderung erfolgreich zu bewältigen, ist, aus jedem Experiment eine maximale Menge an Information bzw. Daten zu gewinnen und so schon in frühen Entwicklungsstadien das Prozessverständnis zu steigern.
PAT ist zu einer entscheidenden Komponente für die Gewinnung von Echtzeitinformationen aus jedem Experiment geworden, die eine vernetzte (automatisierte) Entscheidungsfindung ermöglicht. PAT verändert die Industrie und ist nicht mehr nur ein „Nice to have“, sondern ein „Need to have“ geworden.
Referenzen:
[1] Covid-19 Recovery in Chemical R&D – Mettler Toledo (mt.com)
[2] https://doi.org/10.1002/advs.202105547
[3] https://doi.org/10.1021/acs.oprd.1c00231
Autoren: Ian Haley, Paul Hermant, Paul Kuijpers,
Technology & Application Consultant, Mettler-Toledo AutoChem