Energiesparende Fördertechnik in der Vorarlberger Mühle
Die Vorarlberger Mühle produziert Hartweizengrieß für die Pasta-Herstellung und Mehl für Backwaren aus Weichweizen mit einem Durchsatz von 90 bis 110 t in 24 h.
Dr. Jörg Lantzsch, Fachjournalist, Agentur Dr. Lantzsch
Zuverlässigkeit und Wartungsarmut sind die wesentlichen Anforderungen an Systeme für moderne Mühlen. Denn diese laufen heute überwiegend vollautomatisch und mit wenig Personal. Bei der Fördertechnik setzt die Vorarlberger Mühle deswegen auf Seilförderer der Wessjohann fördertechnische Anlagen.
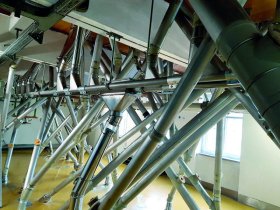
Die Vorarlberger Mühle am Standort Feldkirch gehört zu den zehn größten Mühlen in Österreich. Der Familienbetrieb, zu dem neben der Mühle auch noch ein Mischfutter- und Holzpellets-Werk in Dornbirn gehört, steht kurz vor dem Wechsel zur sechsten Generation innerhalb der Familie. Die kombinierte Mühle produziert etwa hälftig Hartweizengrieß für die Pasta-Herstellung und Mehl für Backwaren aus Weichweizen. Je nach Produkt beträgt der Durchsatz 90 bis 110 t pro 24 Stunden. Während der Grieß praktisch ausschließlich an Industriekunden geliefert wird, sind die Weichweizen-Mehle und Backmischungen in Kleinpackungen auch im Einzelhandel erhältlich. Die Hauptabnehmer für das Mehl sind aber Bäckereien.
Betrieb rund um die Uhr
Die Mühle produziert 24 Stunden am Tag, an sieben Tagen in der Woche hochwertiges Mehl und Grieß. „Um den Betrieb rund um die Uhr zu ermöglichen, ist in unserer Mühle alles durchautomatisiert“, erklärt Heinz Kollmann, der als Obermüller und Leiter Produktion und Technik für die reibungslosen Abläufe in der Mühle sorgt. Der Müllermeister, der auch eine Ausbildung zum Bäcker abgeschlossen hat, verfügt über sehr viel Erfahrung und hat vor der Vorarlberger Mühle in verschiedenen Großmühlen rund um den Globus die Technik und Produktion geleitet. Insgesamt arbeiten 16 Mitarbeiter in der Mühle. Da in der Nachtschicht kein Personal vor Ort ist, ist ein hoher Automatisierungsgrad unabdingbar und Störungen sollten nach Möglichkeit sehr selten sein.
„Müller sind heute eigentlich Prozesstechniker, deren Aufgabe darin besteht, eine durchautomatisierte Anlage zu überwachen“, meint Heinz Kollmann. Eine moderne Industriemühle besteht aus zahlreichen Walzenstühlen, in denen der Mehlkern des Korns von den Schalenbestandteilen getrennt wird. Zwischen den einzelnen Walzenstuhlvermahlungen trennen die sogenannten Plansichter die einzelnen Bestandteile voneinander ab. Grieße werden von den Plansichtern zu den Grießputzmaschinen transportiert, um dort bestmöglich von Schalenteilen gesäubert zu werden. Anschließend werden sie von dort zu den nachfolgenden Verarbeitungsstufen geschickt. Je nach Endprodukt durchläuft das Mahlgut bis zu fünf Schrot- und zwölf Grießauflöspassagen.
Produktschonende Fördertechnik
Zwischen den einzelnen Passagen muss das Mahlgut zum nächsten Walzenstuhl transportiert werden. Dabei sind die Förderstrecken innerhalb der Mühle teilweise horizontal oder das Fördergut muss sogar nach oben transportiert werden. Ein rein auf Schwerkraft beruhendes Fördersystem ist deswegen oftmals nicht möglich. Eine besonders wichtige Anforderung an das Fördersystem nennt Heinz Kollmann: „Die Fördertechnik muss das Mahlgut möglichst schonend fördern.“ Für die Förderung nach oben kommen in der Mühle überwiegend pneumatische Fördereinrichtungen zum Einsatz. Für die waagerechten Förderstrecken setzt Heinz Kollmann auf eine Seilförderanlage von Wessjohann fördertechnische Anlagen.
Die Seilförderer verwenden ein Fibercoat-Kunststoffseil, an dem in regelmäßigen Abständen Mitnehmerscheiben angebracht sind. Förderseil und Mitnehmerscheiben laufen in einem Edelstahlrohr mit einem Durchmesser von 60,3 mm und fördern die Zwischenprodukte bzw. den Grieß sehr schonend. Der Reibradantrieb sorgt für eine gleichmäßige und geräuscharme Kraftübertragung. Je nach Größe können auch mehrere Reibradantriebe in einer Anlage kombiniert werden.
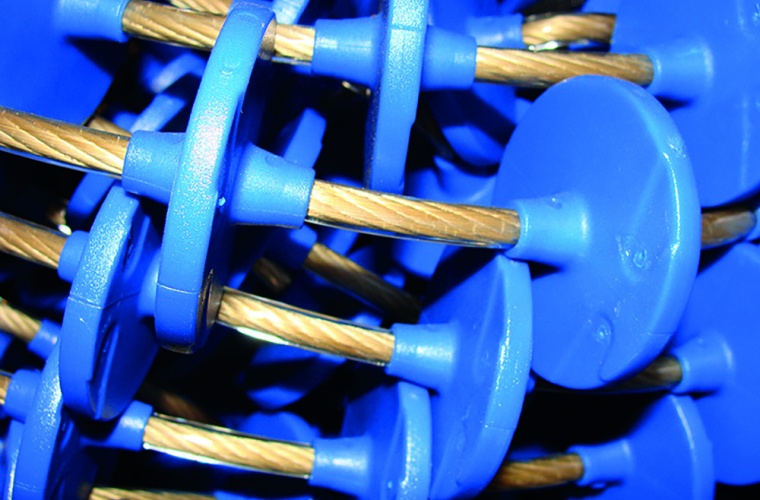
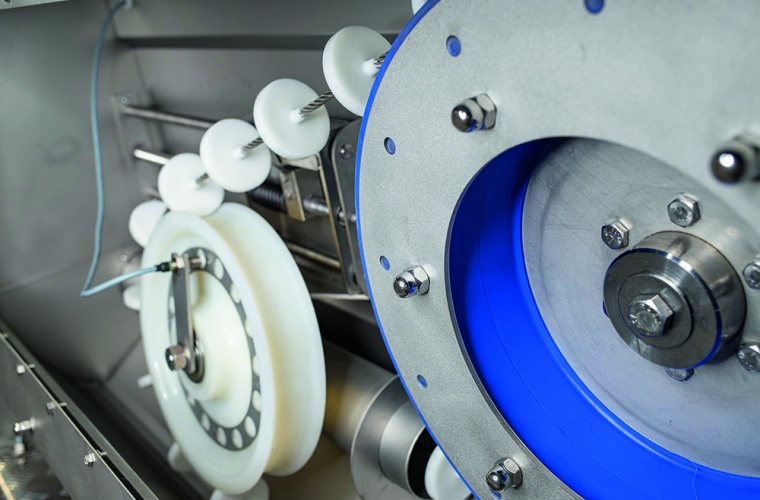
Flexibel konfigurierbar
„Einer der großen Vorteile des Systems ist die hohe Flexibilität“, erwähnt Heinz Kollmann den Hauptgrund, der ihn sofort überzeugt hat, den Seilförderer zu verwenden. Eckrollen können das Förderseil beliebig umlenken. Dadurch lässt sich die Förderstrecke flexibel an die räumlichen Gegebenheiten anpassen, selbst ein Wechsel aus der Waagrechten in eine schräge Förderstrecke ist machbar. Gerade in der Vorarlberger Mühle war dies besonders wichtig, da die Förderstrecke mehrmals die Richtung ändern muss. „Mit Schneckenförderern oder Trogketten wäre dies praktisch nicht möglich gewesen“, ist Heinz Kollmann überzeugt. Das Förderseil mit den Mitnehmerscheiben, der Reibradantrieb, und die Eckrollen sind extrem widerstandsfähig und wartungsarm.
Bei einer Förderlänge von rund zweimal 25 m und einer Gesamtlänge von fast 100 m kommt der Seilförderer mit einem einzigen Antrieb aus, die Leistungsaufnahme beträgt dabei lediglich 0,7 kW. Damit ist die Fördertechnik deutlich energieeffizienter als andere Lösungen. „Mit dieser geringen Leistung fördern wir bis zu 1.500 kg pro Stunde“, sagt Heinz Kollmann. Und auch weitere Anforderungen, die in der Lebensmittelindustrie gefragt sind, erfüllt das System. So sind sämtliche Kunststoffteile für den Lebensmittelbereich zertifiziert, und das Rohr besteht aus Edelstahl. Die Mitnehmerscheiben sind für Lebensmittelanwendungen auch aus blauem Polypropylen lieferbar. Auch der Ex-Schutz ist konstruktionsbedingt kein Problem. Funkenschlag ist durch die Kunststoffkomponenten ausgeschlossen und aufgrund der niedrigen Geschwindigkeiten ist auch eine starke Erhitzung nicht realistisch.
Planung, Installation und Inbetriebnahme
Als Heinz Kollmann die Fördertechnik in der Mühle geplant hat, besuchte er die Powtech in Nürnberg, wo er erstmals mit Wessjohann in Kontakt kam. In den Folgemonaten haben die beiden Unternehmen im regen Austausch die Anlage konzipiert. Die Planung des Anlagenlayouts in der Mühle hat Heinz Kollmann selbst gemacht. Beim Aufbau der Förderanlage machte sich dann laut dem Müllermeister ein weiterer Vorteil bemerkbar: „Dank dem Baukastensystem ist die Förderanlage sehr schön und einfach zu montieren.“ Die gute Zusammenarbeit zeigte sich auch in der Inbetriebnahme-Phase, wo alle Probleme schnell und gut gelöst werden konnten.
Die Einbindung in die Steuerungstechnik der Mühle ist unkompliziert. Ein digitaler Ausgang der SPS schaltet den Schütz für den Motor, der das Reibrad antreibt. Über einen digitalen Eingang erhält die SPS die Rückmeldung, dass der Motor läuft. Und auch eine Überwachung hat Heinz Kollmann integriert. Eine Drehzahlüberwachung an einer der Spannrollen würde feststellen, wenn etwa das Förderseil reißt oder klemmt. „Nach der Inbetriebnahme ist das aber nicht mehr vorgekommen“, sagt Heinz Kollmann. Die neue Förderanlage ist jetzt seit 2019 in Betrieb und läuft seitdem problemlos. Verschleiß an den Förderelementen gibt es praktisch nicht. „In den vergangenen Jahren haben wir lediglich die Reibräder und Umlenkrollen ausgetauscht“, so Heinz Kollmann: „Anderen Wartungsaufwand gab es an dem System nicht.“
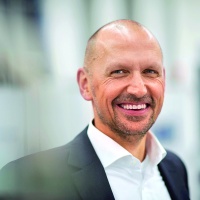
Dr. Jörg Lantzsch, Fachjournalist, Agentur Dr. Lantzsch
© Dr .Lantzsch