Explosionsschutz in der Prozesstechnik
Mischer werden auch in explosionsgefährdeten Bereichen eingesetzt. Für den präventive Explosionsschutz sind von der Konstruktion bis zum Betrieb sind einige Punkte zu beachten.
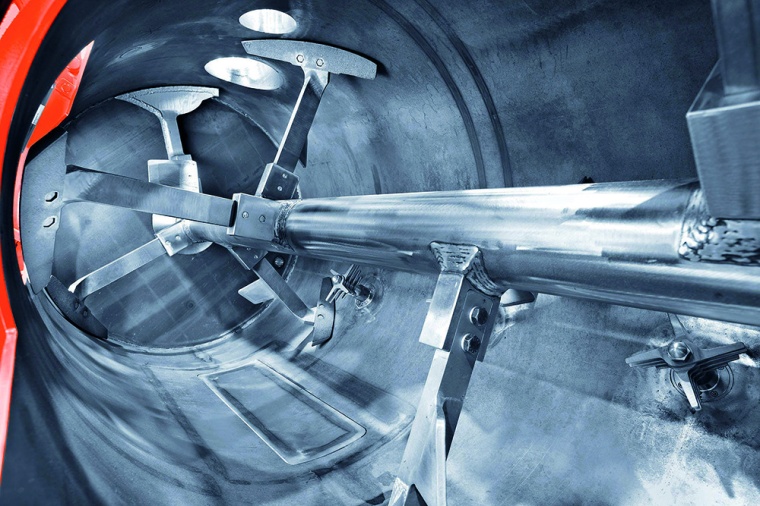
Ob Umwelt- und Baustoffindustrie, Chemie- und Pharmaindustrie, Kosmetik- oder Lebensmittelherstellung. In nahezu allen Industriebereichen werden Schüttgüter gemischt. Dabei kommen Mischer auch in explosionsgefährdeten Bereichen zum Einsatz. Ein präventiver Explosionsschutz kann Mitarbeiter und Anlagen wirksam schützen. Von der Konstruktion bis zum Betrieb der Maschine sind dabei eine Reihe von Punkten zu beachten.
Wie alle Maschinen, die für den Einsatz in explosionsgefährdeten Bereichen vorgesehen sind, müssen Mischer, die innerhalb der EU in Verkehr gebracht werden, der Richtlinie 2014/34/ EU entsprechen. Die 2016 in Kraft getretene Atex-Richtlinie richtet sich in erster Linie an den Hersteller und regelt die grundlegenden Anforderungen an den Explosionsschutz. Andere Länder, andere Sitten bzw. Richtlinien: Das gilt auch beim Explosionsschutz. So gelten in Russland, China, den USA oder Australien/Neuseeland andere Vorgaben, wie bspw. NFPA/NEC, TR CU, IECEx oder CCC. Erfahrene Maschinenbauer wie Lödige Process Technology besitzen die erforderliche Expertise, um die gültigen Richtlinien – ob europäisch oder international – umzusetzen.
Konstruktiver Explosionsschutz
Der erste Schritt in Richtung konstruktiver Explosionsschutz ist die Auswahl des richtigen Materials. Grundsätzlich können Mischer, je nach Kundenwunsch und Einsatzgebiet, aus verschiedenen Materialien gefertigt werden. Das Spektrum umfasst dabei hochlegierte, nicht rostende Stähle sowie legierte und unlegierte Stähle. In Bezug auf den Explosionsschutz sind funkenarme Werkstoffe, wie bspw. die meisten Edelstähle, jedoch die erste Wahl.
Ein weiterer Punkt, den es bei der Konstruktion zu beachten gilt, ist der Abstand der Schaufeln zur Behälterwand des Mischers. Nach Möglichkeit sollen nur geringe Restmengen des zu mischenden Produkts in der Maschine verbleiben. Dazu ist es notwendig, die Schaufeln sehr nah an die Behälterwand heranzuführen. Doch insbesondere, wenn die Maschine mit einem Doppelmantel zum Heizen und Kühlen ausgestattet ist, können hier Risiken durch den Wärmeeintrag entstehen: Es besteht die Gefahr einer unregelmäßigen Ausdehnung des Druckbehälters, sodass eine Kollision der Schaufeln mit der Behälterwand möglich ist. Die Festlegung der optimalen Schaufelabstände wird zum einen auf der Basis von Erfahrungswerten in Versuchsreihen ermittelt. Zum anderen werden Berechnungen herangezogen, bei denen die Schaufelabstände simuliert dargestellt werden.
Im Rahmen des konstruktiven Explosionsschutzes kann es zudem erforderlich sein, eine Temperaturüberwachung an den heißesten Stellen im Mischer vorzusehen. Diese Stellen treten in der Regel an den Abdichtungen auf. Dazu zählen sowohl die Abdichtungen der Hauptwelle, aber auch die Abdichtungen an den einzelnen Messerköpfen. Die Wärmeentwicklung entsteht durch die Drehbewegung der Welle, die von der Maschinengröße, dem Maschinentyp und dem jeweiligen Verfahren abhängt. Diese Drehzahlen, die bei der Welle teilweise > 500 1/min und bei den Messerköpfen > 1.500 1/min betragen können, lassen sich durch den Einsatz von Frequenzumrichtern beeinflussen.
Weitere heiße Oberflächen können durch den Wärmeeintrag eines Doppelmantels für Beheizung und Kühlung entstehen. Hierbei ist es wichtig, dass die zugeführte thermische Energie unterhalb der Zündtemperatur liegt. Beispielsweise ist das Betreiben eines Doppelmantels mit einer Temperatur von 300 °C und einem Produkt mit einer Zündtemperatur von 200 °C nicht ohne weiteres möglich. In diesem Fall müssen z.B. Maßnahmen aus dem Bereich des primären Explosionsschutzes zum Einsatz kommen. Spezialisierte Maschinenbauer sind in der Lage vor der Umsetzung eines Kundenauftrags Lösungen für entsprechende Sonderfälle zu erarbeiten.
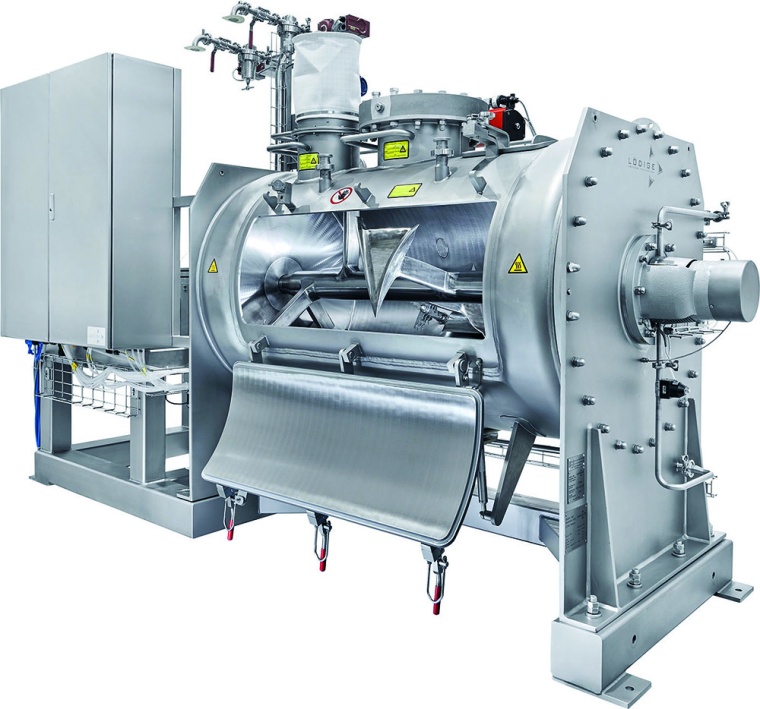
Primärer Explosionsschutz – Vermeiden einer explosiven Atmosphäre
Die Inertisierung des Mischers zur Vermeidung einer explosiven Atmosphäre zählt zu den primären Explosionsschutzmaßnahmen. Hierbei wird in der Regel ein Vielfaches des Mischervolumens an Inertgas (CO2, N2, Edelgase etc.) in den Mischer gegeben und der Durchfluss sicherheitsgerichtet überwacht. Die Menge hängt von dem zu mischenden Produkt ab. Dabei wird das Inertgas mittels eines separaten Stutzens in den Mischer eingeblasen. Dies erfolgt vorzugsweise mittels Druckwechselverfahren unter Anwendung von Vakuum oder Überdruck. Dabei sind die Auslegungsparameter des Mischers zu beachten. Zusätzlich wird, nach der erfolgreichen Inertisierung, über die Abdichtungen das Inertgas nachgeführt. Dies dient der Aufrechterhaltung der Inertisierung. Bei Bedarf kann mittels des Stutzens nachinertisiert werden.
Die Inertisierung ist dann sinnvoll, wenn das Produkt extrem zündfähig ist und es sich ggf. um hybride Gemische handelt. Hybride Gemische sind Gemische aus Luft und brennbaren Gasen, Dämpfen oder Nebeln, gepaart mit brennbarem Staub. Um hybride Gemische beurteilen zu können, sind in der Regel Untersuchungen zu den sicherheitstechnischen Kenngrößen erforderlich. Hier sollte daher eine separate Betrachtung durch ein Prüflabor erwogen werden. Dabei gilt es zu untersuchen, wie sich die vorhandenen Gase, Dämpfe oder Nebel auf die sicherheitstechnischen Kenngrößen des Staubes wie Zündtemperatur oder Mindestzündenergie auswirken. Von hybriden Gemischen ist dann auszugehen, wenn die Konzentration des Gases (bspw. Lösemittel) mehr als 20 % der unteren Explosionsgrenze (UEG) beträgt.
Sekundärer Explosionsschutz – Vermeiden wirksamer Zündquellen
Bei Mischern, bei denen keine hybriden Gemische auftreten können, ist in der Regel der sekundäre Explosionsschutz, also das Vermeiden wirksamer Zündquellen, ausreichend. Grundsätzlich sind alle Zündgefahren zu berücksichtigen, die bei Mischern auftreten können, dazu zählen auch Blitzschlag oder Ultraschall. Besonders relevant sind folgende Zündquellen:
- heiße Oberflächen
- mechanisch erzeugte Funken
- elektrische Anlagen
- statische Elektrizität
Diese Gefährdungen sind in der Zündgefahrenbewertung zu betrachten. Gegebenenfalls sind entsprechende Maßnahmen zur Vermeidung wirksamer Zündquellen einzuleiten. Dazu zählt z.B. die beschriebene Temperaturüberwachung der heißesten Stellen im Mischer sowie der Einsatz von konform zur Richtlinie 2014/34/ EU in Verkehr gebrachter elektrischer Anlagen und Bauteile.
Besondere Vorsicht ist bei Mischern geboten, die zusätzlich zum Doppelmantel eine beheizte Welle besitzen. Beim An- und Abfahren der Maschine sind aufgrund der unterschiedlichen thermischen Ausdehnungen besondere Reihenfolgen einzuhalten, um eine Kollision des Mischwerkzeugs mit der Behälterwand zu verhindern.
Auch in Sachen Reinigung muss der Explosionsschutz berücksichtigt werden. Die Reinigung von Mischern erfolgt zum Teil händisch, teilweise aber auch durch WIP-Systeme (Washing in Place) oder CIP-Systeme (Cleaning in Place). Dabei können unterschiedlichste Detergenzien wie Säuren oder Laugen zum Einsatz kommen. In aller Regel stellen diese Reinigungssysteme keine Gefahr aus Ex-Schutz-Sicht dar. Bei der Handreinigung wie dem Ausfegen der Maschine bei pulverförmigen Stoffen ist jedoch darauf zu achten, dass ein Aufwirbeln des Produkts vermieden wird. Insbesondere bei Stäuben sind das Absaugen mit einem Atex-zertifizierten Industriesauger oder eine Nassreinigung vorzuziehen. Ein besonderer Anwendungsfall liegt bei der Reinigung dann vor, wenn mit Reinigern auf Lösemittelbasis gearbeitet wird. Hier könnte es durch Ausgasung zu einer explosionsfähigen Atmosphäre kommen.
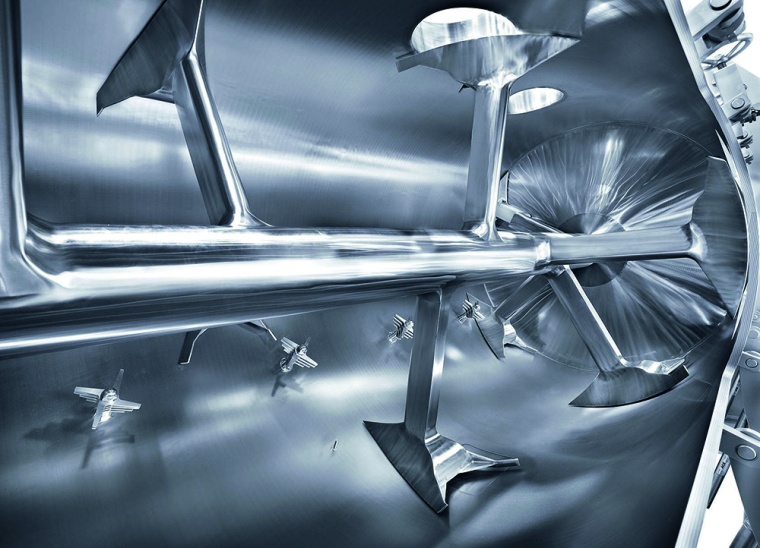
Sicherer Betrieb
Für einen sicheren Betrieb von Mischern in explosionsgefährdeten Bereichen sind weitere Punkte von Bedeutung. Ein besonderes Augenmerk liegt dabei auf den zu mischenden Produkten. Hierbei wird unterschieden, welche Mindestzündenergie (MZE) das jeweilig zu mischende Produkt hat. Es wird unterschieden:
- MZE ≥ 10 mJ (normal zündempfindlich)
- 3 mJ ≤ MZE < 10 mJ (besonders zündempfindlich)
- MZE < 3 mJ (extrem zündempfindlich)
Besitzt eines der zu vermischenden Produkte eine sehr geringe Mindestzündenergie, so kann bspw. die Reihenfolge der Beschickung des Mischers geändert werden, um die erforderliche Sicherheit zu gewährleisten. Die Zugabe der Produkte mit der geringen MZE erfolgt in diesem Fall erst dann, wenn Produkte mit einer höheren Zündtemperatur bereits gemischt werden. Produkte, bei denen mit einer exothermen Reaktion zu rechnen ist, sind dabei als problematisch anzusehen und bedürfen einer detaillierten Betrachtung. Betreiber sind zudem in der Pflicht mögliche Fehlanwendungen zu verhindern.
Hierzu zählen:
- Zündwirksame Fremdkörper, die sich im Produkt befinden und darüber in den Mischer gelangen
- Fremdkörper, die bspw. nach Reinigungs- und Wartungsarbeiten im Mischer verbleiben
- Staubablagerungen, die sich außerhalb des Mischers auf Bauteilen befinden und dann z.B. durch den Einsatz von Druckluft aufgewirbelt werden. Diese sollten nach Möglichkeit mit explosionsgeschützten Staubsaugern entfernt werden
- Austausch von Bauteilen im Rahmen von Wartungs- und Reparaturarbeiten, die nicht die erforderliche Kennzeichnung besitzen
- Verändern der Parameter und Bauteile (Drehzahl, Leistung, Temperatur des Doppelmantels etc.)
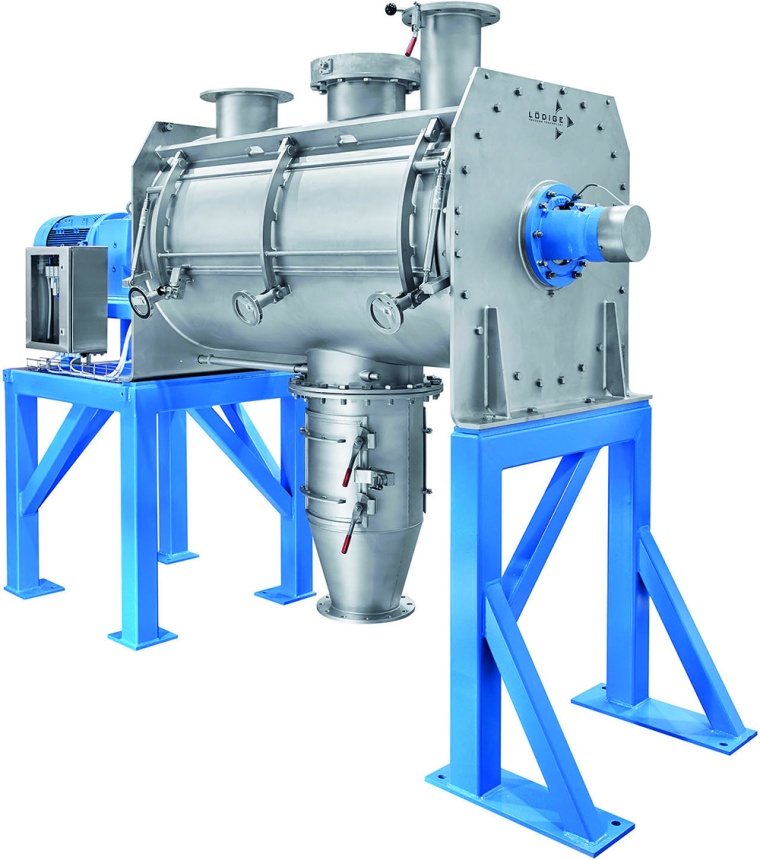
Beratung durch erfahrene Hersteller
Betreiber von Mischern, die in explosionsgefährdeten Bereichen eingesetzt werden, finden in spezialisierten Maschinenbauern wie Lödige Process Technology kompetente Ansprechpartner in Bezug auf Explosionsschutz. Lödige – im Jahr 1938 gegründet – hat mit der Erfindung des Pflugschar-Mischers die Misch- und Aufbereitungstechnik maßgeblich beeinflusst. Mehr als 35.000 ausgelieferte Maschinen und Systeme dokumentieren die Erfahrung für kundenorientierte Systemlösungen. Erfahrene und qualifizierte Hersteller bieten Lösungen nicht nur für das Neumaschinengeschäft, sondern auch für die Modernisierung von Bestandsanlagen sowie deren Anpassung an gesetzliche Anforderungen. Zudem sind sie in der Lage, Betreiber bei der Auslegung, Prüfung und Zonierung ihrer Anlage gemäß den jeweils aktuellen Anforderungen zu unterstützen – sowohl im Hinblick auf den europäischen Markt als auch bei Fragen zu weltweit geltenden rechtlichen und sicherheitstechnischen Anforderungen.
Autor
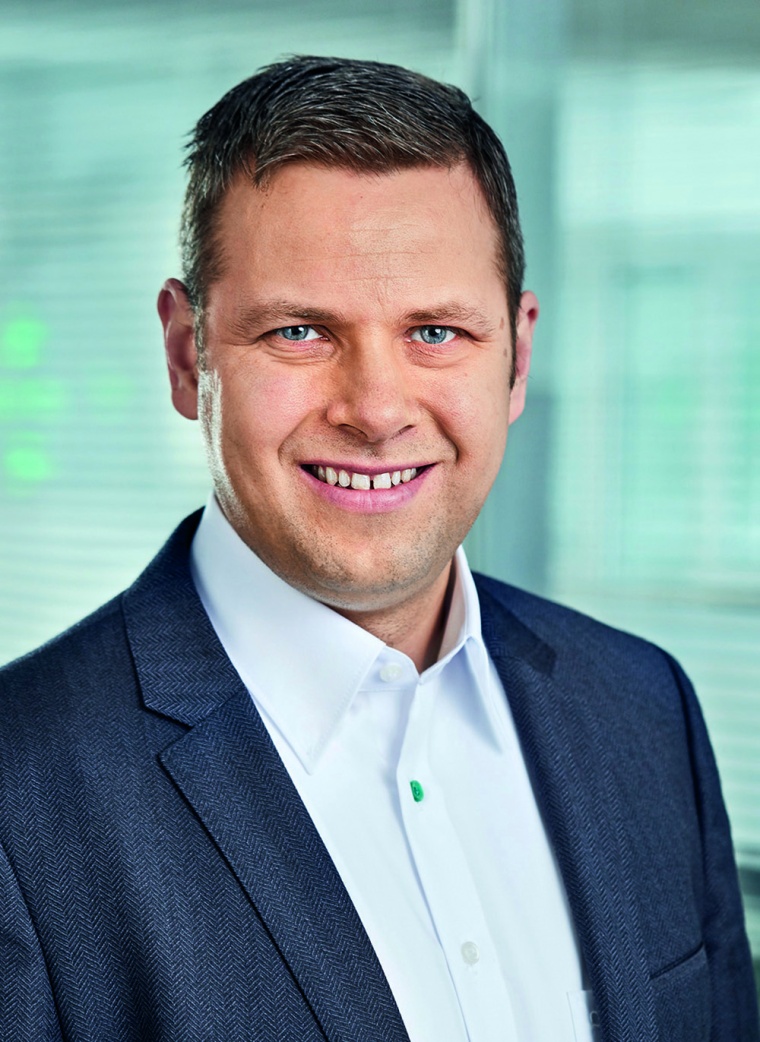