Optimierung der Fleischwarenproduktion mit CSB-System
Um gesetzliche Regelungen und Dokumentationspflichten besser zu unterstützen, hat Courage mit der ERP-Software von CSB-System die Weichen für mehr Wachstum gestellt.
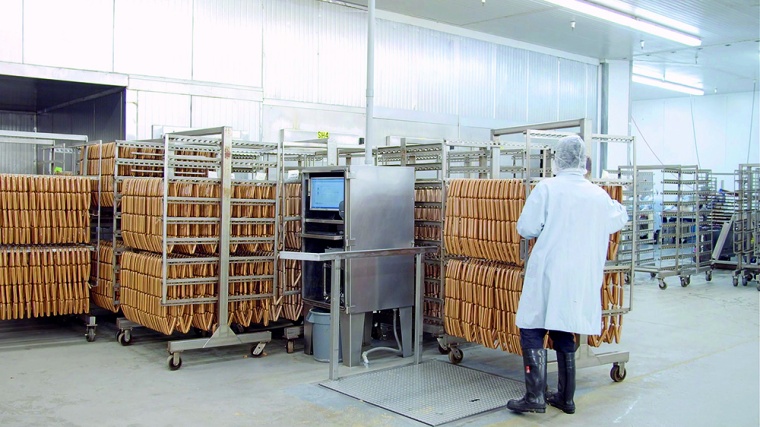
Wer die Kosten senken will, muss Rohstoffe, Prozesse und Produkte unter die Lupe nehmen: Das kalifornische Unternehmen Courage Production hat damit erhebliche Erfolge erzielt – nicht zuletzt durch eine konsequente Datenerfassung während des gesamten Produktionsprozesses. Das Unternehmen mit deutschen Wurzeln setzt auf durchgängige Digitalisierung. Ein alle Bereiche umfassendes ERP-System garantiert optimale Effizienz und schafft die technologische Basis für weiteres Wachstum.
„Wie wäre es, wenn wir genau wüssten, welche Rauchkammer bei welcher Produktgruppe die besten Ergebnisse liefert?“ ist eine der Fragen, die sich Rob Engelhart, Chief Operation Officer von Courage Production, in den letzten Jahren immer wieder gestellt hat. Das Unternehmen mit Sitz in Fairfield, Kalifornien, ist Spezialist für Hot Dogs, Beef Jerky und Feinkost-Produkte – und sehr innovativ, wenn es darum geht, mit neuen Technologien aktuelle Herausforderungen anzugehen. Um die gesetzlichen Regelungen und die steigenden Dokumentationspflichten des wachsenden Unternehmens besser zu unterstützen, hat Courage schon 2009 die ERP-Software von CSB-System implementiert.
Damit legte der Betrieb die Basis für ein umfassendes Optimierungsprogramm, das bis heute viele positive Ergebnisse gebracht hat. „Wir haben uns alleine zwei Jahre lang damit beschäftigt, wie wir den Produktionsprozess verbessern können. Früher war das alles ziemlich kompliziert, jeden Tag gingen rund 50 Seiten Papier in die Produktion: Aufträge, Stücklisten, Rezepturen, Arbeitsanweisungen und so weiter. Das haben wir schon weitgehend digitalisiert und damit gestrafft. Gleichzeitig haben wir unsere Datenerfassung stark intensiviert“, so Engelhart.
Rauchkammeroptimierung
Die digitale Datenerfassung an allen wichtigen Punkten der Verarbeitungskette bietet gleich mehrere Vorteile für den Fleischproduzenten. Zum einen ist die Arbeit mit Scannern und Tastatur schneller und deutlich weniger fehleranfällig als der Einsatz von Papier: Werden Herkunftsinformationen, Produktionszeiten, Qualitätsdaten, Losnummern und weitere relevante Daten an Ort und Stelle elektronisch ins ERP-System geschrieben, müssen sie nicht handschriftlich notiert und später übertragen werden. Zudem ist die Erfassung der Daten im Shopfloor die notwendige Voraussetzung für tiefergehende Analysen, auf deren Basis wiederum die richtigen Maßnahmen abgeleitet werden können.
Am Beispiel der Rauchkammern wird klar, welche Effizienzsprünge hier möglich sind. Courage produziert rund 350 verschiedene Artikel. Jeder einzelne davon kommt irgendwann in eine der vier Rauchkammern – und verliert dort einen Teil seines Gewichts. Nur: wie viel genau und warum unterscheiden sich die Verluste in den Rauchkammern? Wo lassen sich Zusammenhänge zwischen Produkt und Rauchkammer identifizieren, wo Ausbeutepotenziale lokalisieren? Auf solch simple, aber existenzielle Dinge kommt es heute in der Lebensmittelproduktion an. „Uns war es wichtig, die Verluste in den Kammern zu minimieren. Als wir dann im Pilotprojekt anfingen, die Gewichte digital zu erfassen und zu analysieren, hatten wir schon mit Verbesserungen gerechnet. Die tatsächlichen Ergebnisse haben unsere Annahmen aber sogar übertroffen“, sagt Rob Engelhart.
Während des Projekts wurde jeder Rauchwagen an eigens dafür eingerichteten IT-Arbeitsplätzen vor und nach dem Räuchern gewogen und die Gewichte online ins ERP-System übermittelt. Über die aggregierten Daten bekamen die Manager einen genauen Überblick, wie hoch der jeweilige Gewichtsverlust war – und konnten so feststellen, welches Produkt in welcher Rauchkammer am wenigsten Verluste hatte. Das wiederum ermöglichte eine wirtschaftlich optimale Planung und Verteilung der Rohwaren auf die einzelnen Positionen in den Kammern. Das Resultat: Zahlreiche so genannte „Marginal Gains“ – hier 2 % mehr Ausbeute bei Hot Dogs, dort 1 % weniger Wasserverlust bei Beef Jerky – summierten sich am Ende zu einer großen Kostenersparnis. Aus den Erfahrungen, die im Pilotprojekt gesammelt wurden, ist ein neuer Standardprozess geworden. So können heute die Ausbeute jedes Artikels in jeder Rauchkammer optimiert und die Verluste auf ein Minimum reduziert werden.
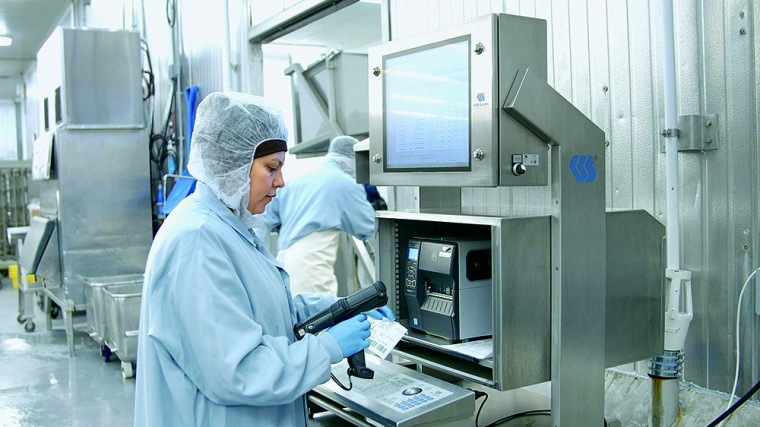
Simulierter Rückruf unter einer Stunde
Der positive Effekt zeigt sich auch bei der Rückverfolgbarkeit der Produkte. Die Erfassung der Daten beginnt am Wareneingang, wo jeder Rohstoff mit Scannern ins System gebucht wird, und folgt dem Verarbeitungsprozess durch Gewürzabteilung, Chargierung, Füllerei, Rauchkammern, Verpackung, Lager und der Kommissionierung. Für jede Charge werden an den CSB-Stationen Etiketten mit Seriennummern und weiteren wichtigen Informationen gedruckt. Über die Nummer der Versandeinheit (NVE) kann Courage schließlich den kompletten Verarbeitungsweg schnell zurückverfolgen – für einen simulierten Rückruf benötigt das Unternehmen weniger als eine Stunde.
Minimierte Ausfallzeiten
Während die digitalen Optimierungen inzwischen zu einem hohen Maß an Effizienz geführt haben, setzen die Manager nun den Fokus auf die kennzahlenorientierte Planung und Steuerung des Fleischwerks. Bei fünf Produktionslinien und mehreren hundert Artikeln ist vor allem die Produktionsplanung eine komplexe Aufgabe, die durch die immer individuelleren Anforderungen der Kunden und kurze Zeitfenster von der Bestellung bis zur Auslieferung zusätzlich erschwert wird. Eine vorausschauende Maschineneinsatzplanung bekommt damit eine immer höhere Bedeutung, um die Produktionslinien bestmöglich auszulasten – und gleichzeitig eine möglichst große Flexibilität für kurzfristige Aufträge zu bewahren. Mit dem Advanced Planning and Scheduling (APS) ist für Courage beides möglich, denn das Modul berücksichtigt bei der Planung die für Courage fünf wichtigsten Faktoren:
- Produktgruppe,
- Etikett,
- Folien,
- Allergene,
- Umrüstungen.
So liefert das System einen bereits optimierten Planungsvorschlag, den die Manager während der Feinplanung noch dynamisch anpassen können. Zuerst wird eine wöchentliche Abverkaufsprognose erstellt, dann eine Produktionsprognose, der Lagerbestand wird geprüft und mit der Materialbedarfsplanung abgeglichen. Erst dann wird die Produktion pro Linie geplant.
Dabei sollen künftig Simulationen genau anzeigen, ob die Linien, Schichten und das Personal optimal ausgelastet sind. Kapazitätsengpässe oder minutengenaue Ausfallzeiten aufgrund von Produktwechseln und allergener Kontamination werden ebenfalls visualisiert, eventuelle Reinigungsvorgänge sind mit einkalkuliert.
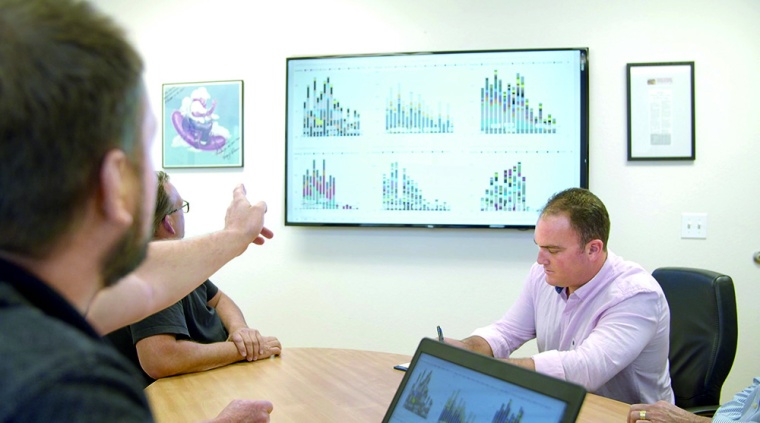
Wachstum mit dem ERP-System
Noch mehr Transparenz soll eine Reihe weiterer Optimierungsmaßnahmen bringen, die Courage jüngst angestoßen hat. Ziel ist es, das ERP-System mit seinen Daten zu Bestellungen, Auftragseingängen, Rechnungen Chargenkalkulationen, Produktionsaufträgen, Kommissioniervorgängen und Lagerbeständen zum Treiber für alle Geschäftsentscheidungen zu machen. Großes Potenzial schlummert aktuell noch in den Lagerbeständen. Über genauere Erfassungen und Dokumentationen der Bestandsbewegungen wollen die Manager jederzeit eine Übersicht darüber bekommen, welche exakten Werte zu einem bestimmten Zeitpunkt vorhanden sind. Um den Mitarbeitern in der Produktion die Arbeit zu erleichtern und die Produkte weiter zu standardisieren, sollen zudem die Stücklisten um technische Verfahrensanweisungen ergänzt werden.
Erfolgreich umgesetzt wurde jüngst das EDI-Modul (Electronic Data Interchange), das die Zusammenarbeit mit Handelskunden wie Costco, Trader Joe´s, Whole Foods (Amazon), Safeway und Vons weiter vereinfacht hat. Denn der automatisierte Datenaustausch – von vielen Key Accounts auch gefordert – ist ein wichtiger Baustein für das Wachstum des Betriebs. „Wir wollen in den nächsten fünf Jahren die Produktion verdoppeln und unsere Produkte in den ganzen USA vertreiben“, sagt Rob Engelhart.