Nachhaltige Messtechnik für Wasserstoffanwendungen
Im Gespräch mit CITplus erläutern die Produktmanager von VEGA Stefan Kaspar und Robin Müller die Anforderungen an Druck- und Füllstandmessgeräte für Anwendungen in der Wasserstoffproduktion. Neben der Anwendungstechnik für Druck- und Füllstandmessungen in Elektrolyseuren beschreiben sie auch die Kommunikationsmöglichkeiten der Sensoren und beleuchten die Nachfragesituation für eine digitale Vernetzung der Messtechnik. Außerdem sprechen wir darüber, welche Rolle das Thema Nachhaltigkeit derzeit bei der Gerätetechnik spielt.
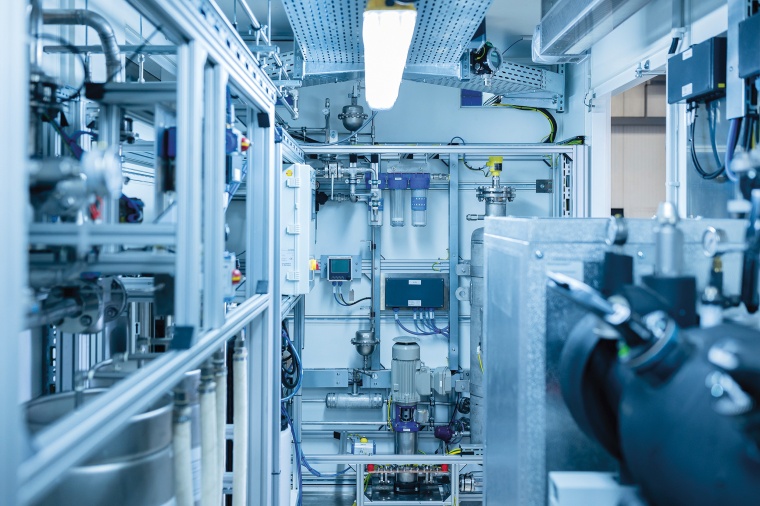
CITplus: Guten Tag, Herr Kaspar und Herr Müller. Die Produktion von Wasserstoff ist ein aufstrebender Industriezweig. Sind Messaufgaben in Wasserstoffanwendungen neu für Vega und gibt es generelle Anforderungen an die Messtechnik?
Robin Müller: Neu sind die Messaufgaben nicht. Wasserstoff wird in vielen Prozessen schon sehr lange verwendet, allerdings kommen neue Anwendungen hinzu, die auch zu deutlich höheren Drücken hochskaliert werden. Wir gehen dazu mit den bestehenden Geräten in den Markt und passen diese an die jeweilige Anwendung an. Gerade der Bedarf von grünem Wasserstoff lässt die Nachfrage nach Messtechnik in Elektrolyseuren steigen. Die Geräte sind alle aus sehr hochwertigen Materialien wie beispielsweise Edelstahl gefertigt. Wir nutzen hauptsächlich 316L, der grundsätzlich für Wasserstoff geeignet ist.
Neben dem Stahl kommt es auch auf die Dichtungen an. Welche Lösungen haben Sie im Portfolio?
R. Müller: Wir haben ein Angebot an speziellen Hochdruckprozessanschlüssen, zum Beispiel von Swagelok, die allgemein für Hochdruckgase verwendet werden können. Im Niederdruckbereich bieten wir je nach Kundenwunsch verschiedenste Gewindeanschlüsse und auch Flanschprozessanschlüsse an und können uns flexibel an das Dichtungskonzept der Auftraggeber anpassen. Nach innen haben wir vollverschweißte Geräte für die Druckmessung, die komplett aus Edelstahl bestehen. Zwar kann Wasserstoff durch die dünne Membran leicht diffundieren, aber das bewegt sich in einem sehr, sehr geringen Bereich, der von den Anlagenbetreibern akzeptiert wird. Bei anderen Geräten, wie beispielsweise bei geführten oder freistrahlenden Radarsensoren oder einem keramischen Drucksensor, haben wir auch Elastomerdichtungen verbaut – hier verwenden wir meist FKM als bewährten und beständigen Dichtungswerkstoff für Wasserstoffanwendungen.
Über welche Anwendungen Ihrer Füllstandmesstechnik können Sie berichten?
Stefan Kaspar: Die Füllstandmesstechnik kommt primär bei Elektrolyseuren zum Einsatz. Kernaufgabe ist es, das Niveau des Elektrolyts kontinuierlich zu messen, damit der Füllstand eingeregelt werden kann. In alkalischen Elektrolyseuren handelt es sich um Kalilauge, in PEM-Elektrolyseuren um Reinstwasser. Typischerweise messen wir mit geführtem oder freistrahlendem Radar.
R. Müller: Druckmesstechnik wird vor allem für die Messung von gasförmigem Wasserstoff genutzt. Im Niederdruckbereich bis 100 bar, zum Beispiel in Elektrolyseuren oder Wasserstoffpipelines, setzen wir bevorzugt unsere trockene keramische Messzelle ein, bei der durch die Keramik kein Wasserstoff diffundieren und damit auch der Messwert nicht verfälscht werden kann. Zwar lässt die Elastomerdoppeldichtung eine leichte Diffusion zu, aber dahinter haben wir kein Öl, das sich in irgendeiner Weise durch den Wasserstoff aufblähen und die Funktion beeinträchtigen kann. Darüber hinaus verwenden wir in Hochdruckanwendungen, zum Beispiel in Wasserstoffspeichern mit 350 oder 700 bar Druck, trockene metallische Druckmesszellen mit spezieller langzeitstabiler Membran, mit denen wir den Druck bis 1.000 bar messen können.
Wie kommunizieren die Druck- und Füllstandssensoren?
S. Kaspar: Die meisten der von uns verkauften Messgeräte kommunizieren nach wie vor über die bewährte 4…20 mA-HART-Schnittstelle. Alternativ bieten wir unsere Geräte seit vielen Jahren mit den digitalen Feldbussen Profibus PA und Foundation Fieldbus an. Allerdings sind diese den meisten Betreibern im täglichen Einsatz zu komplex. Für Standardanwendungen bieten wir mit unserer Basic-Linie Geräte mit IO-Link-Schnittstelle an, die sich gerade bei Druckmessungen auch für einige Wasserstoffanwendungen eignen. Natürlich haben wir auch das Thema Ethernet-APL in der Entwicklung. Noch dieses Jahr werden wir unseren neuesten Radar-Füllstandsensor Vegapuls 6X mit Ethernet-APL-Elektronik vorstellen.
Stefan Kaspar, Produktmanager Füllstandmesstechnik, Vega Grieshaber
„Es braucht herstellerseitig entsprechend Zeit, um alle Messgeräte mit der neuen Ethernet-Technologie auszustatten. Denn solange für eine Anlage nicht alle Messgeräte-Typen verfügbar sind, ist es für einen Anlagenbauer schwierig, vollends auf Ethernet-APL zu setzen.“
Welche Möglichkeiten der Zustandsüberwachung bieten die Vega-Geräte?
S. Kaspar: Unsere Geräte verfügen über Selbstüberwachungs- und Diagnosefunktionen, die konform zum Namur-Standard NE 107 ausgegeben werden können. Die Geräte zeigen damit standardisiert an, ob und wenn ja, welcher Fehler oder welche Störung vorliegt oder wann Wartungsbedarf besteht.Allerdings sind unsere Geräte nahezu wartungsfrei und gehen nur sehr selten kaputt.
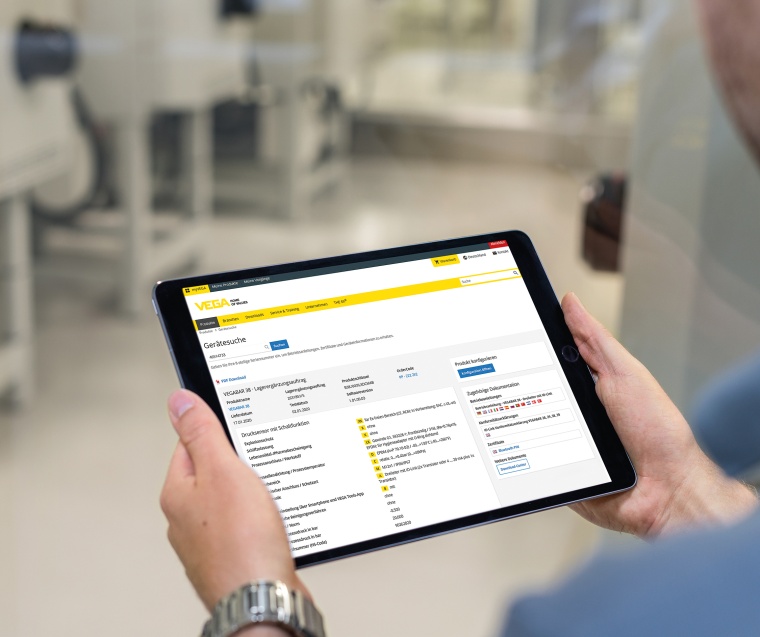
Wäre es nicht naheliegend, die neuen Wasserstofffanlagen gleich mit entsprechend APL-fähigen Geräten auszustatten?
S. Kaspar: Nun, da gibt es den Wunsch und es gibt die Wirklichkeit aller Beteiligten. Das Problem ist leider noch immer die Verfügbarkeit entsprechender Geräte, aber auch der nötigen Peripherie. Am Markt verfügbar für alle Messprinzipien sind Geräte mit 4…20 mA-HART Schnittstelle. Daneben gibt es busfähige Geräte mit Profibus- und Foundation-Fieldbus-Kommunikation. Doch diese Bussysteme sind vielen Betreibern zu komplex und werden auch für Neuanlagen immer weniger geplant. Das heißt, es ist eher ein Rückgang zu verzeichnen, weil die Komplexität in der Regel über die Jahre einfach nicht händelbar ist. Wir haben sogar schon wieder zurückgebaut von Bussystemen auf 4...20 mA-HART. Deshalb hofft die ganze Branche nun auf den neuen Ethernet-APL-Standard, um die Digitalisierung endlich voranzubringen. Es braucht herstellerseitig entsprechend Zeit, um alle Messgeräte mit der neuen Ethernet-Technologie auszustatten. Denn solange für eine Anlage nicht alle Messgeräte-Typen verfügbar sind, ist es für einen Anlagenbauer schwierig, vollends auf Ethernet-APL zu setzen. Zum Glück können die verfügbaren Ethernet-APL-Switches parallel auch Geräte mit Profibus DP betreiben, sodass die Gerätelücke mit Profibus-Geräten geschlossen werden kann.
Dennoch ist die digitale Kommunikation ein wichtiger Baustein im Betrieb der Anlagen.
R. Müller: Aus diesem Grund bieten wir zusätzlich Bluetooth als Brückentechnologie an. Über Bluetooth lassen sich hohe Datenraten realisieren, was beispielsweise den automatisierten Import und Export der Geräteparameter ermöglicht. Die Daten können auf der MyVega-Plattform als Back-up zwischengespeichert werden, um auf das Ersatzgerät geladen zu werden. Auch Wiederholungsprüfungen der Geräte lassen sich per Bluetooth auf unserer Plattform hinterlegen und Zugangspins dort zentral verwalten. Dieser komplette Service ist kostenfrei für unsere Kunden.
Aber Bluetooth hat nur eine sehr begrenzte Reichweite.
R. Müller: Richtig, die Inbetriebnahme über Smartphone oder Tablet muss typischerweise im Umkreis von zehn bis 20 Metern erfolgen. Weil die Inbetriebnahme jedoch in der Regel einmalig erfolgt und man dabei ohnehin meist vor Ort ist, ist der Aufwand überschaubar.
Robin Müller, Produktmanager Druckmesstechnik, Vega Grieshaber
„Bei der Entscheidung für oder gegen eine Reparatur spielt nicht nur die Wirtschaftlichkeit eine Rolle, sondern auch die Frage nach einer nachhaltigen Nutzung der Geräte und damit der Ressourcen.“
Und bei einer Anwendung in einemElektrolyse-Container gibt es kein Sicherheitsproblem, weil jedermann sehr gut die Bluetooth-Verbindung aufnehmen könnte?
R. Müller: Diese Sensoren sind alle mit Passwörtern geschützt, sodass eben nicht jedermann rankommt. Außerdem entsprechen die neu entwickelten Geräte wie der Vegapuls 6X Security-Richtlinien wie der IEC 62443, die sicherstellen, dass die Geräte schon im Entwicklungsprozess mit aktuellen Mitteln der IT-Sicherheit ausgestattet werden, um gegen Cyberangriffe bestmöglich geschützt zu sein.
Wäre es sinnvoll, die Sensoren gleich mit WLAN auszustatten?
R. Müller: Zwar erreichen wir damit eine größere Reichweite, aber die Technik benötigt zu viel Energie. Wir brauchen mehr als 90 % der Energie nur, um das Messgerät zu betreiben. Und Mobilfunk per SIM-Karte wäre noch energiehungriger. Möglich ist ein Lowpower-Funkstandard wie LoRaWan. Mit diesem haben wir einzelne Geräte ausgestattet, darunter unsere Vegapuls-Air-Serie.
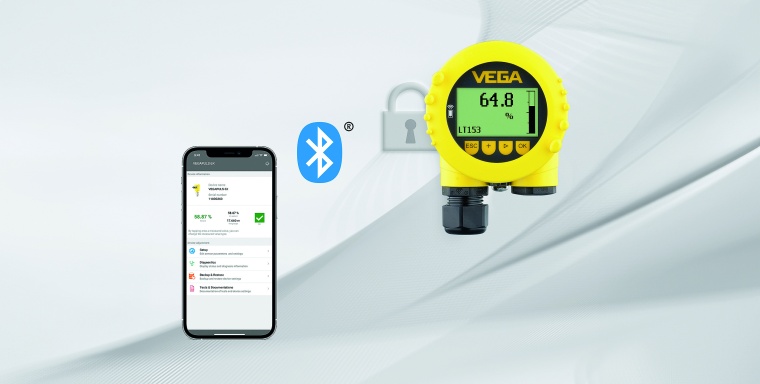
Wie nehmen Ihre Kunden die MyVega-Plattform an?
S. Kaspar: Viele Kunden haben erkannt, dass es im Moment die einzig gangbare Alternative ist, um Gerätedaten zentral und bequem zu speichern und zu verwalten. Wir haben daher stark steigende Nutzerzahlen. Außerdem arbeiten wir an Lösungen, um die Daten lokal beim Betreiber zu speichern. Wenn es herstellübergreifende Informationsaustauschplattformen gäbe, wäre das für viele Betreiber sicher noch interessanter. Es gibt verschiedene Ansätze dazu, wie sie zum Beispiel im Digital Data Chain Konsortium oder in der Open Industry 4.0 Alliance entwickelt werden – aber leider ist die Materie komplex und es wird vermutlich noch länger dauern, bis herstellerübergreifende Cloud-Lösungen etabliert sind.
Fallen bestimmte Anwendungen im Bereich der Wasserstofferzeugung unter ATEX-Richtlinien?
R. Müller: Die Anlagen insgesamt schon, aber unsere Geräte interessanterweise sehr oft nicht, weil die kompletten Wasserstoffanlagen häufig in speziellen Hallen oder auch in Containern aufgebaut werden und diese über eine sehr gute Belüftung verfügen, sodass keine Ex-Atmosphäre entstehen kann. Dennoch gibt es immer wieder Auftraggeber, die eine Ex-Zulassung anfragen, um sich abzusichern.
Kommen wir zum Thema Nachhaltigkeit. Das kann bei Geräten zum Beispiel auch die Reparaturfähigkeit und Betriebsdauer adressieren. Wie stellt sich Vega diesem Thema?
S. Kaspar: Nachhaltigkeit sehen wir auf jeden Fall als eine wachsende Anforderung bei uns und bei unseren Kunden. Wir haben eine Reparaturabteilung und gehen davon aus, dass Aspekte wie Nachhaltigkeit und Reparaturfähigkeit zukünftig zum Kaufkriterium für unsere Kunden werden. Unsere Geräte basieren auf einem modularen Konzept, sodass beispielsweise die Elektronik leicht ausgetauscht werden kann.
Lohnt sich das tatsächlich für den Betreiber und auch für Sie?
S. Kaspar: Es kommt immer auf das Schadensbild an. Wenn mit der Prozessbaugruppe die teuerste Komponente am Gerät betroffen ist, macht eine Reparatur meist wenig Sinn. Ist es lediglich die Elektronik, sieht das schon anders aus. Hinzu kommt der Gerätepreis an sich: Eine Reparatur lohnt sich eher bei hochpreisigen Geräten. Nach der Instandsetzung kann der Sensor nochmal einige Jahre zuverlässig messen. Allerdings wird der Service noch eher selten genutzt, weil sich natürlich auch die Messtechnik weiterentwickelt und nicht unbedingt veraltete Technik wieder eingebaut werden soll.
R. Müller: Bei der Entscheidung für oder gegen eine Reparatur spielt jedoch nicht nur die Wirtschaftlichkeit eine Rolle, sondern auch die Frage nach einer nachhaltigen Nutzung der Geräte und damit der Ressourcen. Ich bin gespannt, wie in Zukunft die Entscheidungen dazu getroffen werden.
Das Interview führte Dr. Etwina Gandert, Chefredakteurin CITplus.