Digitalisierte, geführte Instandhaltung
In kaum einem anderen Industriezweig ist die Instandhaltung so wichtig wie in der Prozessindustrie, um ungeplante Stillstände zu vermeiden. Kommt es trotz allem dazu, ist jede Sekunde, die bei Fehlersuche und Reparatur eingespart werden kann, viel Geld wert. Je besser Instandhaltungs-Fachkräfte bei ihren Aufgaben unterstützt werden, desto effizienter und vor allem zuverlässiger können sie arbeiten. Diese Unterstützung schafft digitalisierte, geführte Instandhaltung.
Die Instandhaltung hat zum Ziel, die Funktionsfähigkeit einer Produktionsanlage erstens zu erhalten und zweites bei Verlust wiederherzustellen. Ersteres geschieht zumeist durch Inspektion und Wartung, letzteres durch Fehlersuche und Reparatur. In der Prozessindustrie spielen Inspektion und Wartung im Vergleich zu vielen anderen technischen Anwendungen eine größere Rolle, da ungeplante Stillstände in der Prozessfertigung durchschnittlich vielfach höherer Kosten verursachen. Daher müssen solche Stillstände, die eine Fehlersuche und Reparatur notwendig machen, von vornherein vermieden werden.
Da die Anlagen auch für Inspektion und Wartung heruntergefahren werden müssen, entstehen zusätzlich Kosten durch Produktionsausfälle. Wird während der Wartung festgestellt, dass benötigtes Werkzeug fehlt, oder zusätzliche Ersatzteile benötigt werden, steigen die Zusatzkosten ungeplant an. Gleiches passiert, wenn eingeplante Fachkräfte zum Zeitpunkt der Wartung ausfallen und ungeübten Vertretern die zu erledigenden Aufgaben erst erklärt werden müssen. Kurzum: Inspektion und Wartung müssen generalstabsmäßig geplant und durchgeführt werden. Dabei reicht es nicht, Zeitpunkt und Dauer zu planen. Vollständigkeit bei maximaler Effizienz kann nur erreicht werden, wenn alle Tätigkeiten, die während der Inspektion und Wartung durchgeführt werden sollen, bekannt und geplant sind.
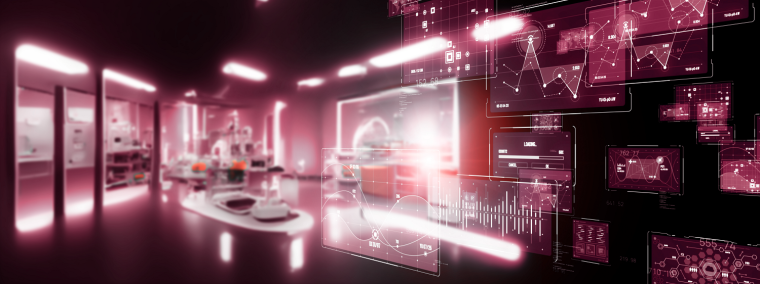
In vier Schritten zur geführten Instandsetzung
Um bei der Planung strukturiert vorzugehen und sicherzustellen, dass alle relevanten Tätigkeiten berücksichtigt werden, sollten die folgenden vier Schritten iterativ bearbeitet werden:
- Überblick verschaffen
Alle Bestandteile des Anlagensystems, die Gegenstand von Inspektion und Wartung sein können, müssen übersichtlich gelistet und dargestellt werden. Dabei hilft es der Struktur, die einzelnen Bestandteile in Gruppen zu unterteilen. Beispielsweise kann nach Aktoren, Sensoren, Steuergeräten und rein mechanischen Bauteilen unterteilt werden. So kann die Vollständigkeit gruppenweise überprüft werden. Weitere Anhaltspunkte dafür können Verbau- und Teilelisten sein. Im Rahmen dieser Systemanalyse bietet es sich an, eindeutige Namen und – im Vorgriff auf eine spätere Digitalisierung - maschinenlesbare Adressen zu vergeben.
- Ursachen erkennen und bewerten
Als nächstes muss für jeden zuvor ermittelten Bestandteil des Gesamtsystems hinterlegt werden, welche Fehlerursachen hier auftreten können. Weiterhin muss beurteilt werden, ob das Auftreten der Fehlerursache durch Wartung verhindert oder zumindest die Eintrittswahrscheinlichkeit gesenkt werden kann. Abschließend gilt es auf Basis dieser Einschätzungen zu beurteilen, an welchen Bauteilen für welche Fehlerursachen Inspektion und Wartung vorgesehen werden sollten. Für die Fehlerursachen können abhängig von der Art (Gruppe) des Systembestandteils generische Kataloge verwendet und gepflegt werden. Einzelne Katalogeinträge können fallweise auf Relevanz überprüft und entsprechend berücksichtigt oder mit entsprechendem Vermerk außer Acht gelassen werden. Auch hier ist es wieder sinnvoll, eindeutige Namen und maschinenlesbare Identifier für die Fehlerursachen zu verwenden.
- Inspektions- und Wartungsalgorithmen definieren
Für alle Inspektions- und Wartungsfälle, die im vorangegangenen Schritt für zielführend befunden wurden, müssen nun Algorithmen definiert werden. Algorithmen sind nicht notwendiger Weise Quellcodes. Im Grunde sind es einfache Schritt-für-Schritt-Anweisungen zur Abarbeitung von Aufgaben. Gegenüber Checklisten wird der Nutzer an die Hand genommen und durch die Aufgabe geführt, statt dass er sie lediglich quittiert. Es mag auf den ersten Blick aufwändig erscheinen, diese Anleitungen zu erstellen, aber ihr Nutzen überwiegt den Aufwand bei Weitem. Die Aufgaben können schneller und vor allem in wiederholbarer Qualität abgearbeitet werden. Es können ergänzende Checklisten zu benötigtem Werkzeug, Ersatzteilen und Vergleichswerten für Messungen und Teilenummern hinterlegt werden. Außerdem sollte zu jedem Inspektions- und Wartungs-Algorithmus hinterlegt werden, in welchem Intervall er durchzuführen ist und wie viele Personen und Zeiteinheiten für die Durchführung benötigt werden. Zudem lohnt sich auch hier ein Blick in Richtung Digitalisierung: Werden diese Algorithmen software-gestützt erzeugt, kann ein generischer Grundalgorithmus geschaffen und von diesem unterschiedlich stark ins Detail gehende Derivate abgeleitet werden. So kann beispielsweise ein sehr detailliertes Derivat zur Unterstützung von Auszubildenen und ein weniger detailliertes für Fachkräfte mit langjähriger Erfahrung erzeugt werden. Auch die Übersetzung in verschiedenen Sprachen ist bei digital erzeugten Algorithmen kein Problem.
- Inspektion und Wartung planen
In einem letzten Schritt werden Inspektion und Wartung auf Grundlage der Algorithmen und ihrer Metadaten zeitlich und inhaltlich ausgeplant. Metadaten umfassen zum Beispiel benötigtes Personal, Werkzeug und Ersatzteile, geschätzte Dauer, Durchführungsintervall, etc. Steht eine Inspektion oder Wartung an, erhält jede beteiligte Fachkraft einen Abarbeitungsplan und die ihr zugewiesenen Algorithmen (ggf. in der individuell sinnvollen Detailtiefe und Sprache). Benötigte Werkzeuge und Ersatzteile können vorab bereitgestellt werden und der effizienten und vollständigen Abarbeitung der Aufgaben während des geplanten Zeitfensters steht nichts mehr im Wege.
Da geht doch mehr – Ausweitung und Digitalisierung
Auf Basis der Ergebnisse der Schritte eins und zwei können ebenfalls Algorithmen für die Fehlersuche und Reparatur erstellt werden. So kann zielgerichtet und effizient gearbeitet werden, sollte trotz aller Wartung ein ungeplanter Stillstand auftreten. Dabei sollte unter Schritt zwei dokumentiert werden, wie sich eine Kombination aus Fehlerursache an einem bestimmten Systembestandteil bemerkbar macht. Fehlersuch-Algorithmen sind Schritt-für-Schritt-Anweisungen, um von einem solchen Symptom zur eigentlichen Fehlerursache zu gelangen. Der entsprechende Reparatur-Algorithmus beschreibt die Behebung der Fehlerursache.
Eine softwaregestützte Erarbeitung von maschinenlesbaren Ergebnissen eröffnet zusätzliche Möglichkeiten: die Bereitstellung der Algorithmen auf digitalen Endgeräten, oder die Einbindung der Planung und Durchführung in ERP-Systeme sind nur die Spitze des Eisbergs. Automatisierung und der Einsatz von Künstlichen Intelligenzen sind die nächsten Schritte. Selbst die Unterstützung der Fachkräfte durch Augmented Reality oder das Trainieren von Instandhaltungsfällen in einer Virtual Reality sind denkbar.
Mit dem Fortschreiten der Digitalisierung bieten sich mehr und mehr Möglichkeiten, Fachkräfte bei der Instandhaltung von technischen Systemen wie Produktionsanlagen zu unterstützen. Die Potenziale zur Einsparung von Zeit und damit Geld und zur Vermeidung von Produktionsausfällen sind enorm. Es wäre vermessen zu glauben, dass sich geführte Instandhaltung nicht lohnt.
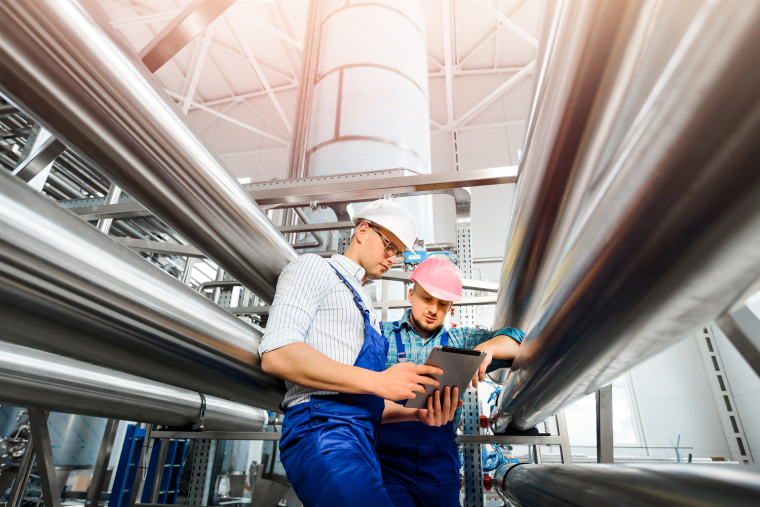
Autor: Johannes H. Diedrich, Leiter Industrieprojekte der Synostik GmbH
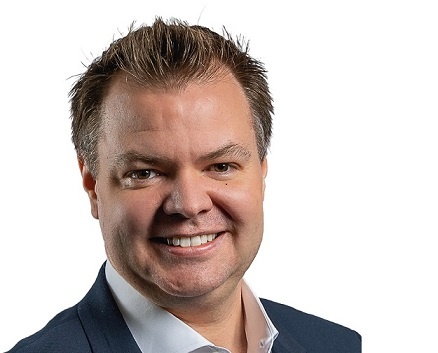