Reifenrecycling – Ruß aus Altreifen
Altreifen durchlaufen zahlreiche Recycling-Prozesse. Unterschieden wird zwischen werkstofflichem Recycling (Sortieren, Separieren und Granulieren), rohstofflichem Recycling (z.B. Pyrolyse-Verfahren) und dem chemischen Recycling als finaler Veredelungsschritt der Pyrolyse. Mit dem Verfahren von RCB Nanotechnologies lässt sich hochreiner Ruß (recovered Carbon Black) aus dem Kautschuk wiedergewinnen.
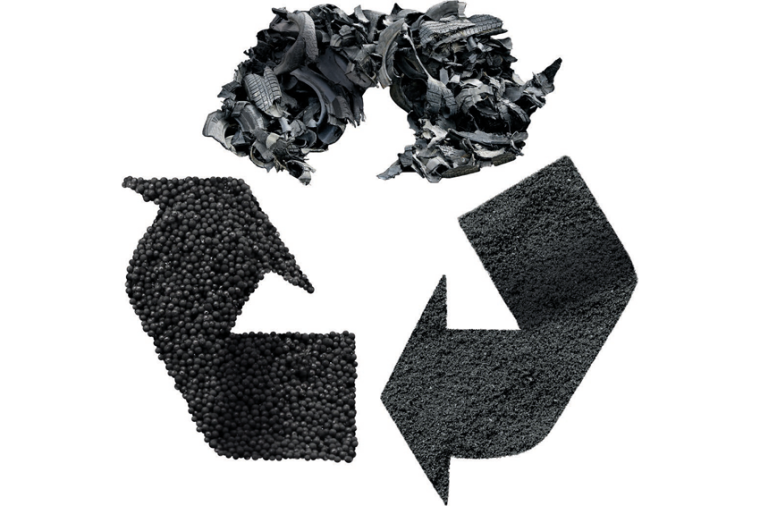
Carbon Black, im Volksmund auch Industrieruß genannt, kommt fast in jedem schwarzen Gummi- oder Kunststoffprodukt vor. Ein Großteil des hergestellten Hightech Industriewerkstoffes – rund 70 % der weltweiten Gesamtproduktion – wird für die Produktion von Reifen benötigt. Für die Herstellung einer Tonne Carbon Black verbrauchen Hersteller neben großen Wassermengen rund 1,5 t fossiler Rohstoffe. Zusätzlich entstehen beim Herstellprozess von Carbon Black bis zu 3 t CO2-Emissionen. Schätzungen zufolge lagern derzeit weltweit rund vier Milliarden Altreifen auf Deponien, ein gebrauchter Pkw-Reifen enthält ca. 3 kg Carbon Black.
Rückgewinnung von Carbon Black
Durch innovative Technologien zur Aufbereitung der Altreifen, könnte dieser bislang ungenutzte Materialschatz zukünftig viel besser wiederverwertet werden. „In der industriellen Rückgewinnung von Carbon Black liegen vielversprechende Potenziale für Kunden und Umwelt“, sagt Dr. Markus Vöge, CEO der Zeppelin Systems. „Wir möchten unseren Kunden nachhaltige Alternativen für die Reifenherstellung anbieten – bei gleichbleibender Qualität und in ausreichender Quantität“, ergänzt Guido Veit, Vice President Sales für Polyolefine, Rubber und Silos bei Zeppelin Systems. Und genau an diesem Punkt setzt der Friedrichshafener Anlagenbauer gemeinsam mit dem Unternehmen RCB Nanotechnologies an!
Die Prozesse zum wertstofflichen, zum rohstofflichen und chemischen Recycling von Altreifen. © Zeppelin Systems
Neues Verfahren für reines recovered Carbon Black
RCB Nanotechnologies entwickelte zusammen mit dem Fraunhofer Institut für Bauphysik IBP ein neues Verfahren. Dieses Verfahren wurde von Fraunhofer IBP zum Patent angemeldet und RCB Nanotechnologies hat die exklusiven, weltweiten industriellen Verwertungsrechte. In dem Verfahren wird der Ascheanteil (aktuell von bis zu 25 %) vom – durch Pyrolyse gewonnenen – Roh-recovered Carbon Black, abgetrennt. Die Verunreinigung des Roh-recovered Carbon Black ist aktuell schon ein großes Hemmnis für die industrielle Einsetzbarkeit des Materials. Der Ascheanteil wird zudem in den kommenden Jahren stark zunehmen, da die Reifenhersteller vermehrt weitere Additive einsetzen, die sich nach der Pyrolyse neben dem Kohlenstoff als „Asche“ im recovered Carbon Black wiederfinden. Ascheanteile von 30 bis 35 % sind in absehbarer Zukunft zu erwarten, was den Einsatz des recovered Carbon Black immer weiter erschwert bzw. unmöglich machen wird.
Damit ist das Verfahren von Fraunhofer IBP und RCB Nanotechnologies für die weitere Verwendung von recovered Carbon Black unbedingt erforderlich, um eine ökologische Alternative zu Carbon Black auch zukünftig zu gewährleisten. Das durch das Verfahren hergestellte, hochwertige und äußerst reine recovered Carbon Black (rCB) weist einen Kohlenstoffanteil von ca. 98 % auf. Zahlreiche Tests des neuen rCB mit namhaften Reifenherstellern bestätigten, dass die Qualität im Vergleich zum ursprünglichen Industriematerial (herkömmliches Carbon Black wie bspw. N550, N660 und N772) aufgrund der hohen Reinheit des veredelten rCB absolut vergleichbar ist. Somit können bestimmte Carbon Black-Qualitäten in Zukunft zu 100 % substituiert werden. Zusätzlich werden im Prozess aus dem separierten Ascheanteil weitere, hochwertige Produkte gewonnen, bspw. Silizium- oder Zink-basierte Verbindungen. Damit entstehen im Prozess zusätzliche, nachhaltige Wertstoffkreisläufe für die Bau- und Reifenindustrie. Als Lösungsanbieter und Systemintegrator kann Zeppelin Systems die Technologie von RCB Nanotechnologies problemlos in bestehende, oder neue Pyrolyseanlagen einbinden.
Autoren: Patrick Buder, Sustainability Strategy Manager Zeppelin Systems und Jan Diercks, Managing Director, RCB Nanotechnologies
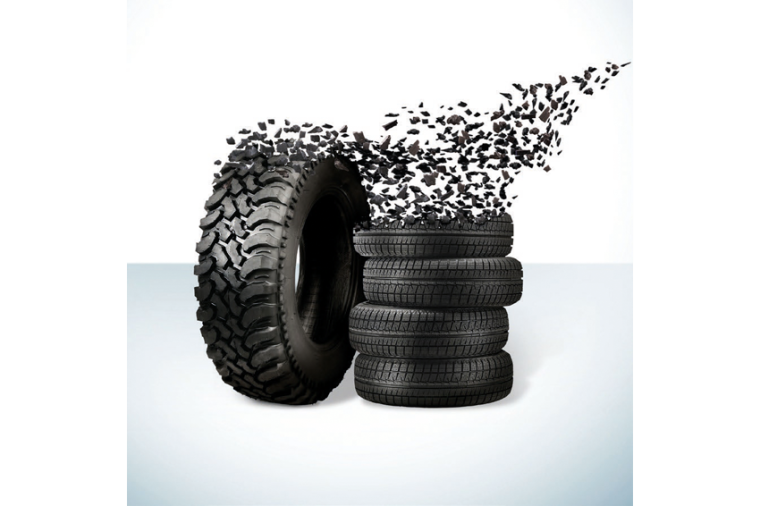
Nachgefragt bei Patrick Buder, Sustainability Strategy Manager Zeppelin Systems
Das Interview führte Dr. Etwina Gandert, Chefredakteurin CITplus.
Altreifen werden bereits in großen Mengen gesammelt. Was geschieht mit dem Altgummi in der Regel?
Patrick Buder: Laut aktuellen Zahlen für das Thema Altreifen-Recycling, fallen in Europa pro Jahr rund 3,5 Mio. t Altreifen an. Allein in Deutschland kamen im Jahr 2021 rund 550.000 t benutzter Reifen zusammen. Würde jeder Altreifen in Europa wiederverwertet, könnten so rund 2,45 Mio. t CO2-Emmissionen eingespart werden.
Aktuell am Markt verfügbare Verfahren der werkstofflichen Aufbereitung zerlegen den Reifen in der Regel in seine einzelnen Fraktionen – Stahl, Textil und Gummi. Der Stahl wird hierbei wiederverwertet. Die Textilfasern werden oftmals zu Ersatzbrennstoff weiterverarbeitet und der Verbrennung zugeführt. Das Gummi hingegen wird je nach Korngröße entweder thermisch verwertet oder beispielsweise für Bodenbeläge und Sportplätze eingesetzt. Zunehmend werden Altreifen auch deponiert oder illegal entsorgt. Diese Art und Weise des Altreifen-Recyclings ist jedoch nicht mehr zukunftsträchtig und stellt die Recyclingbetriebe zunehmend vor wirtschaftliche Herausforderungen. Es muss ein Umdenken der Recyclingbranche stattfinden. Denn das Potenzial Altreifen ist durch die Selbstverpflichtung der Reifenindustrie, Rezyklate für die Produktion neuer Reifen einzusetzen, enorm groß.
Warum hat das wertstoffliche Recycling von Reifen eine große Bedeutung und was ist daran besonders schwierig?
P. Buder: Nach den Selbstverpflichtungen der Reifenindustrie soll ein Reifen bis spätestens 2050 zu 100 % aus natürlichen Ressourcen, aus nachhaltigen sowie recycelten Materialien hergestellt werden. Die Reifenhersteller wissen genau, dass sie auf hochwertige, recycelte und nachhaltige Materialien zurückgreifen müssen. Sie kennen ihren Bedarf und müssen daher Wege finden, um das Volumen, die Spezifikationen und die Konsistenz von den Recyclingbetrieben zu erhalten.
Hierfür benötigt es innovative Ansätze, die bestehende Verfahren aufwerten. Ziel ist, eine ausreichende Menge und eine konstante Qualität der Rezyklate sicherzustellen, die von der Reifenindustrie auch wieder bei der Produktion neuer Reifen eingesetzt werden kann. Aktuell lassen die herkömmlichen Verfahren einen Einsatz der Rezyklate in großen Mengen in einem neuen Reifen nicht zu, da die Qualitätsschwankungen zu groß sind. Hochwertige, für die Reifenindustrie verwendbare Rezyklate, können nur produziert werden, indem eine gewisse Art von Sortenreinheit geschaffen wird. Dies ist möglich, wenn bei der Reifenannahme nicht geeignete Altreifen bereits aussortiert oder Reifenteile separiert werden. Hochwertige Reifenteile wie beispielsweise die Lauffläche gebrauchter Lkw-Reifen, bedienen einen anderen Kundenstamm als Teile von den Seitenwänden.
Welche Produkte entstehen dabei?
P. Buder: In der Regel werden beim werkstofflichen Recycling rund 75 % Gummi, cirka 15 % Stahl sowie ungefähr 10 % Textilien gewonnen. Beim rohstofflichen Recycling hingegen ca. 33 % Carbon Black und ungefähr 34 % Öl. Je nach Reinheit und Qualität wird hierbei eine erhebliche Wertschöpfung erzielt.
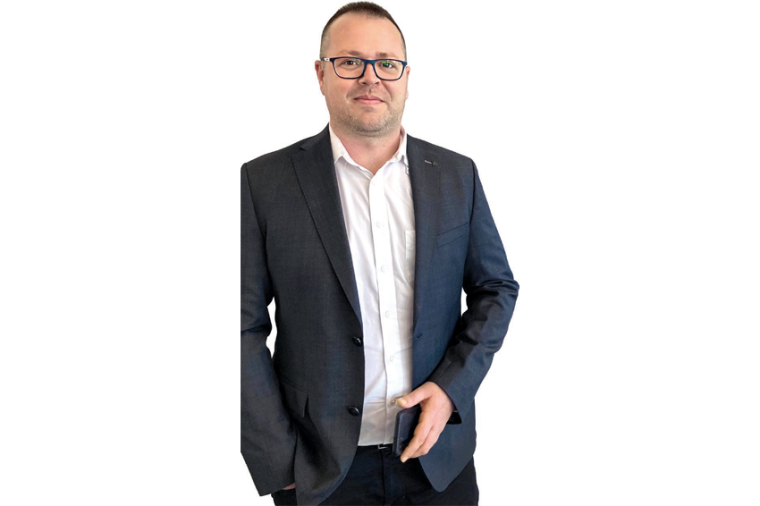
Welche Verfahren kommen beim wertstofflichen und rohstofflichen Recycling zum Einsatz und welches Entwicklungspotenzial besteht hier noch?
P. Bruder: Derzeit arbeiten wir mit Technologie- und Prozessgebern im Bereich des werkstofflichen und rohstofflichen Recyclings zusammen. Im Bereich der Reifensortierung sortiert ein Partnerunternehmen – basierend auf einer KI-Technologie – Reifen blitzschnell anhand der Markierungen auf den Seitenwänden. Auch der Verschleißgrad wird blitzschnell erkannt. Diese Technologie entscheidet bereits am Anfang der gesamten Prozesskette über den weiteren Recycling-Prozessschritt.
Mit einem weiteren Partner arbeiten wir an der Aufbereitung der Reifentextilien, welche generell eine Herausforderung für Recyclingbetriebe darstellen. Die Reifentextilien werden grundlegend verdichtet und im Straßenbau eingesetzt. Sie dienen als Stabilisatoren zwischen Bindemittel und dem Asphalt. Im Vergleich zu bisherigen, zellulosebasierten Stabilisatoren, überzeugt das recycelte Material dabei durch eine erhöhte mechanische Festigkeit und einem erhöhten Widerstand gegen das Eindringen von Wasser im Asphalt.
Ein anderer Technologie-Partner produziert Gummigranulate sowie Gummimehl durch den Einsatz eines Hochdruck-Wasserstrahl-Prozesses. Dieses Verfahren wird insbesondere bei Großreifen, sogenannten „Off-the-Road-Reifen“ mit Reifendurchmessern von bis zu vier Metern angewendet. Täglich fallen in Minen weltweit große Mengen an Altreifen an – die überall einsetzbare Hochdruck-Wasserstrahl-Technologie soll dieses Problem nachhaltig und umweltfreundlich lösen.
Um Gummi-Rezyklate wieder in eine Gummimischung integrieren bzw. erneut vulkanisieren zu können, müssen die Gummi-Rezyklate devulkanisiert werden. Und auch für diesen Fall hat die Zeppelin Sustainable Tire Alliance einen starken Partner an Bord.
Im rohstofflichen Recycling arbeiten wir mit Europas größtem und erfolgreichstem Betreiber einer Pyrolyse-Anlage für Altreifen zusammen. Bei der Pyrolyse werden Altreifen in Rohstoffe aufgespaltet, daraus resultiert Pyrolyse-Öl und recovered Carbon Black (rCB).
Ein weiterer Partner verfolgt das Ziel, gewonnenes Roh-rCB aus dem Pyrolyse-Prozess zu reinigen bzw. den Ascheanteil, welcher regionalen Schwankungen unterliegen kann, zu separieren. Neben reinem rCB entstehen zusätzlich im Prozess weitere, hochwertige Produkte, beispielsweise Silizium- und Zink-basierte Verbindungen.
Das Ergebnis: Nachhaltige Wertstoffkreisläufe für die Bau- und Reifenindustrie. Auch in der Reifenherstellung arbeiten wir mit Rohstofflieferanten zusammen, die nachhaltige Produkte – bspw. funktionale Additive – anbieten, um den Rollwiderstand zu verringern.
Weitere Entwicklungspotenziale beim Reifenrecycling sehen wir in der gezielten Separierung der Altreifen, wie beispielsweise der Abtrennung einzelner Reifenschichten oder auch das Analysieren von Rohstoffen in Reifen. Hierdurch können die Reifen gezielt dem besten Recyclingverfahren zugeführt werden.
Warum braucht es eine Sustainable Tire Alliance und wie sieht diese konkret aus?
P. Buder: Die Zeppelin Sustainable Tire Alliance steht für Tire-to-Tire Recycling. Sie verfolgt das Ziel, die Kreislaufwirtschaft nachhaltig zu unterstützen und im Industriemaßstab anzukurbeln. Dabei kommen Technologien zum Einsatz die den Anspruch verfolgen, hochwertige Rezyklate zu produzieren und reproduzierbare Qualitäten in ausreichender Menge sicherzustellen. Der geteilte Anspruch der Zeppelin Sustainable Tire Alliance besteht darin, dass produzierte Sekundärrohstoffe ein zweites Leben in neuen Reifen erhalten.
Zeppelin Systems sieht sich als Systemintegrator und Lösungsanbieter im Bereich der Reifenherstellung und des Reifenrecyclings.Gemeinsam mit unseren Technologie-Partnern bieten wir unter dem Dach der Zeppelin Sustainable Tire Alliance skalierbare und hoch automatisierte Anlagenkonzepte entlang der Recycling-Wertschöpfungskette an. Wir sind davon überzeugt, das Reifenrecycling als Industriezweig zukünftig ganzheitlich betrachtet werden muss und nicht als stand-Alone Lösung für sich „allein“ stehen kann. Im Weiteren ist die Zeppelin Sustainable Tire Alliance im engen Austausch mit den Industrien, um die Sekundärrohstoffe zu qualifizieren und die entsprechenden Absatzmärkte aufzubauen. Daran werden wir gemeinsam mit unseren Partnern nachdrücklich weiterarbeiten.