Zuverlässig trocknen in der Pharmaproduktion
Bei diversen pharmazeutischen Herstellungsprozessen geht es irgendwann um Trocknung. Das kann die Entfeuchtung von Wirkstoffen sein oder die Entfernung von Haftwasser an Oberflächen. Funktioniert diese nicht oder nicht reibungslos, bringt sie den kompletten Ablauf ins Stocken. Und natürlich spielt das Thema Abluft bei vielen Herstellern eine ebenso große Rolle. Beispiele aus der Praxis zeigen, wie eine abluftfreie Technologie hochwertige Ergebnisse erzielt und zugleich Energiekosten senkt.
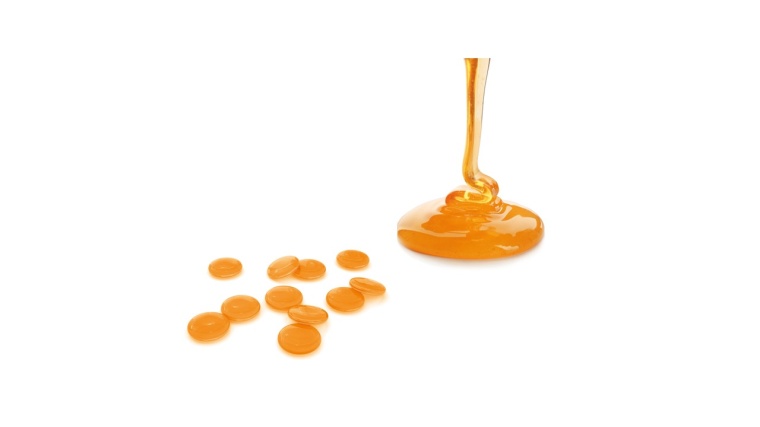
Es geht um die sogenannte Kondensationstrocknung mit Wärmepumpe, die Trocknerhersteller Harter vor über 30 Jahren auf den Markt gebracht hat. Das Allgäuer Unternehmen hat diese Art der Trocknung so entwickelt, dass sie im geschlossenen Kreislauf abläuft. Mit dem abluftfreien Trocknen entfallen auf einmal Themen wie Filtertechnik und die Abhängigkeit von äußeren klimatischen Schwankungen. Produktionsumgebungen und Reinräume bleiben unbelastet. Reinhold Specht, geschäftsführender Gesellschafter bei Harter erklärt: „Das Hauptkriterium in unsere Wärmepumpentrocknung zu investieren, war immer die Tatsache, dass wir Trocknungserfolge erzielt haben, die mit herkömmlichen Verfahren offensichtlich nicht möglich sind.“
Entfeuchtung von Verpackungsoberflächen
Bei einem US-amerikanischen Pharmaunternehmen ging es um die Trocknung von Infusionsbeuteln nach dem Sterilisationsprozess, also von feuchten Oberflächen einer Verpackung. Sind die Beutel nicht vollständig trocken, können sie nicht weiterverarbeitet werden oder werden gar als undichter Ausschuss bei der Qualitätskontrolle aussortiert. Wie zu Beginn eines jeden Projektes führte der Anlagenbauer zunächst einmal Trocknungsversuche im hauseigenen Technikum durch. Hier werden Produkte getestet und mitunter auch neue Produktideen entwickelt. Bei den Tests ermittelt ein Techniker Parameter wie Zeit, Feuchte, Temperatur, Luftvolumenstrom, Luftgeschwindigkeit und die so wichtige Luftführung. Dieses Vorgehen ist eine solide und seriöse Grundlage für die Konzeption einer Trocknungslösung.
In diesem Fall war die Aufgabenstellung groß. Beutel mit unterschiedlichen Größen und Inhalten liegen nebeneinander auf Blechen, wobei jede Charge immer die gleiche Größeneinheit hat. Die Bleche sind in 21 Lagen zu Türmen aufgestapelt. Immer vier dieser Racks werden zeitgleich innerhalb von 90 min sterilisiert. Versuche gaben Aufschluss, dass die Wärmepumpentrocknung die Infusionsbeutel innerhalb der geforderten Taktzeit trocknen konnte. Je vier Racks werden heute nach der Heißwasserberieselung vollautomatisch in den Trockentunnel eingefahren und bei 70 °C vollständig getrocknet. Die Nennleistung der Anlage im Produktionsprozess liegt bei 38 kW. In der technischen Umsetzung spielte bei diesem Projekt die richtige Luftführung die wesentliche Rolle, um alle Beutel zeitgleich mit der gleichen Menge an ungesättigter Prozessluft erreichen zu können. Die Zeiten von nassen Produkten sind heute passé.
„Wir erzielen unsere Erfolge durch eine perfekte Kombination aus Luftentfeuchtung und Luftführung“, so Specht. Die hier verwendete Prozessluft ist stark entfeuchtet. Weil sie somit ungesättigt ist, nimmt sie die Feuchte der Produkte gut und auch schnell auf. Nun gilt es die ungesättigte Luft so über bzw. durch die Produkte zu führen, dass sie nicht daran vorbeiströmt, sondern die Feuchte auch tatsächlich aufnimmt. Sowohl die Aufbereitung und Führung der Luft als auch der Kondensationsprozess laufen in einem geschlossenen Luftkreislauf ab. Luft und Wärme bleiben im System erhalten. Specht erläutert: „Bei diesem Projekt waren umfangreiche Versuchsreihen und viel Feinjustierung unserer Technik gefragt, um dieses gute und sichere Ergebnis zu erreichen. Unser Technikum ist unsere Ideenschmiede somit das Tor zum Erfolg.
Trocknung von Gelee
Ein Hersteller von Lutschpastillen hatte eine sehr zeitaufwändige und klimaabhängige Trocknung im Einsatz. Das Ausgangsprodukt – flüssiges Gelee – darf nur bei niedrigen Temperaturen entfeuchtet werden. Eine Woche Trocknungszeit, das ständige Reagieren auf sich verändernde Wetterverhältnisse und ein Abluftproblem ließen den Hersteller auf die Wärmepumpentrocknung von Harter umstellen. In diesem Fall führte ein Harter-Ingenieur die Versuche mit einem Laborgerät beim Interessenten vor Ort durch, denn das gegossene Gelee konnte nicht ins Technikum transportiert werden. Zwischenzeitlich hat der Hersteller mehrere Trocknungsanlagen des Allgäuer Unternehmens im Einsatz. Das größte Projekt waren sechs baugleiche Kammertrockner. Jeder Kammertrockner hat elf Stellplätze. Insgesamt sind somit 66 Stellplätze vorhanden. Die Kammern sind je 10 m lang und 1,7 m breit. Der Prozess sieht heute folgendermaßen aus.
Wie bisher werden Kunststofftrays mit Stärke befüllt, darin die gewünschten Formen mittels Schablone hineingestanzt und dann die geleeartige Flüssigkeit eingespritzt. Die Trays werden auf spezielle Paletten gestapelt. Diese werden anschließend in die Trocknungskammern eingefahren. Jede Kammer ist für die Beschickung von 2 x 11 Palettengestellen ausgelegt. Es stehen jeweils zwei Palettengestelle nebeneinander, somit 22 in der gesamten Kammer, 132 insgesamt. Mitarbeiter fahren die Wagen manuell ein. Pro Charge werden maximal 2.000 kg Flüssiggelee eingebracht. Bei einer Temperatur von ca. 40 °C wird nun das Gelee auf den vom Hersteller vorgegebenen Trockenstoffgehalt entfeuchtet. Am Ende haben die Pastillen somit die exakt definierte Konsistenz, die Charge ein Restgewicht von circa 1.300 kg. Die Trocknungszeit liegt heute bei 72 Stunden. Dies bedeutet eine zeitliche Verringerung um über 57 %. Der Trockner besteht aus Edelstahl 1.4301 und entspricht GMP-Anforderungen. Die gesamte Anlage läuft im Dauerbetrieb 24/7 und hat eine Nennleistung von nur 33 kW.
Komplexe Geometrien
Eine wieder gänzlich andere Anwendung war die Trocknung von Edelstahlfässern. In ihnen transportiert ein Hersteller betriebsintern seine pharmazeutischen Wirkstoffe. Die Fässer sind Transportgebinde, die vor ihrer Wiederverwendung eine Reinigung und folglich auch eine Trocknung benötigen. Das Pharmaunternehmen hatte hierfür eine Waschanlage mit Trockenfunktion angeschafft, die nicht hielt, was sie versprach. Wie so oft stellte dies der Betreiber erst in der realen Produktion fest. Mitarbeiter bliesen die Fässer nachträglich mit Pressluft aus, was viel Zeit und Geld kostete. „Diesem Umstand begegnen wir in unserem Alltag sehr oft“, berichtet Specht. „Viele unserer Kunden haben ein Problem mit ihrer bestehenden Trocknung, weil sie bei der Anlagenbeschaffung stillschweigend davon ausgehen, dass sie einfach funktioniert – was sie eben oft nicht tut.“
Die Vorgabe war eine klar definierte Restfeuchte seiner Gebinde innen und außen. Diese haben unterschiedliche Größen mit Volumen von 10 bis 30 l. Auch in ihren Geometrien unterscheiden sich die Fässer sehr. Während die einen konisch zulaufen, haben andere einen Falz, der für die Trocknung eine große Herausforderung darstellt. Zudem sind die Wandstärken der Fässer verschieden, was ebenso Einfluss auf die Trocknung hat. Das Kniffligste für die Trocknung jedoch war die kleine Öffnung der Fässer ins Innere. Wie sich derlei Bedingungen in der Trocknung verhalten, testete Harter auch hier in seinem Technikum. Bei diesem Pharmazulieferer gab es sehr ausführliche Versuchsreihen mit unterschiedlichsten Parametern bis die finale Lösung einer Trocken-Kühl-Station entwickelt werden konnte.
Die Trockenkammer nimmt heute einen Trockengutträger auf. Auf diesem Träger befinden sich Fässer unterschiedlicher Größe mit der Öffnung nach unten. Die Luftführung spielt hier nun die entscheidende Rolle. Hierfür entwickelte Harter einen technischen Kniff, der aus Gründen des Know-how nicht näher erläutert wird. Diese Technik sorgt nun dafür, dass die Prozessluft in das Innere der Fässer gelangt und auch wieder abgeführt wird. So werden die Edelstahlgebinde sowohl innen wie außen durch die trockene Prozessluft entfeuchtet. Die Trocknung läuft bei 70 °C ab. Bei niedrigeren Temperaturen wäre die gesamte Prozesszeit von 30 min nicht einhaltbar gewesen. Innerhalb dieser halben Stunde findet auch der Kühlprozess bei 40 °C statt. Nach dieser Zeit sind Fässer jeder Größe und Geometrie gänzlich trocken und können wieder mit ihren Inhalten befüllt werden. „Mit uns haben Kunden eine zuverlässige Technologie nach modernsten Standards und einen zuverlässigen Entwicklungspartner an ihrer Seite“, so Specht abschließend.
Autorin:
Petra Schlachter, Technische Redaktion und Kommunikation, Harter