Reinste Energie- und Kabelführungen
Der Reinraum stellt besonders hohe Anforderungen an die Abriebfestigkeit sich bewegender Komponenten, denn jegliche Verunreinigungen können sich produkt- und prozessschädigend auswirken. Igus entwickelt Hochleistungspolymer-Produkte und prüft diese im eigenen Reinraumlabor.
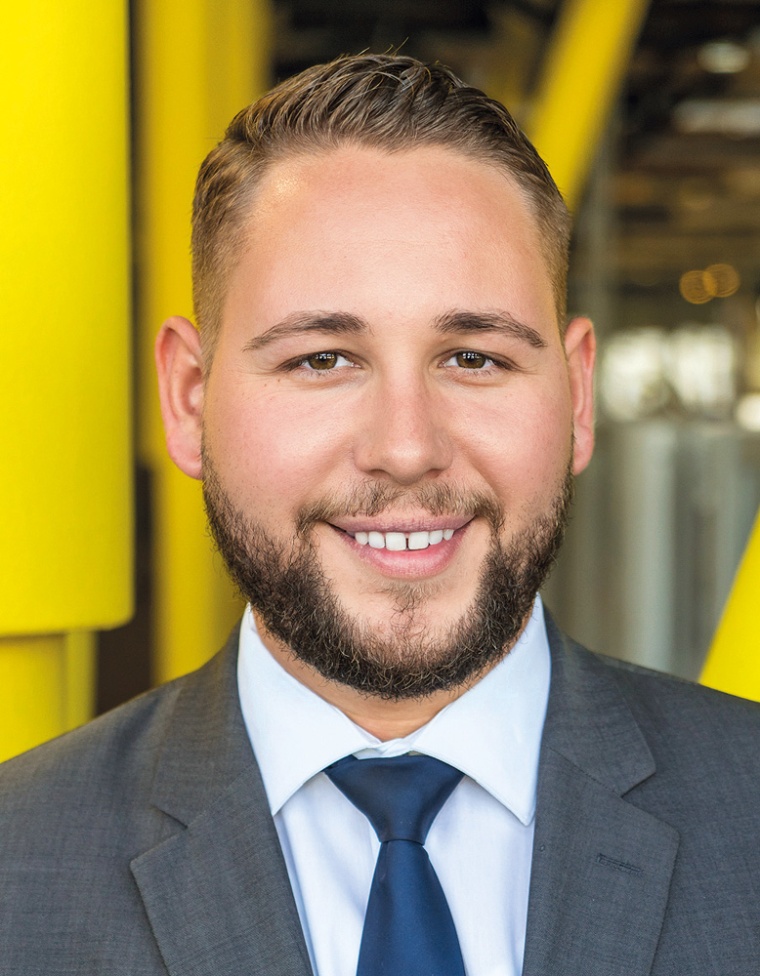
Um den Produkten darüber hinaus die bestmögliche Eignung im Reinraum zu attestieren, werden sie weiteren Tests durch das Fraunhofer Institut unterzogen.
Dies ermöglicht inzwischen ein IPA-geprüftes Produktportfolio mit bestmöglicher Reinraum-Klassifizierung (ISO Klasse 1).
Herr Mattonet, seit 1971 stellt igus Energieführungen her, seit 2001 partikelfreie speziell für Reinraumanwendungen. Wie kam es dazu, dass Sie in diesem Marktsegment expandiert haben?
Peter Mattonet: 1997 startete Igus mit ersten Reinraumtests für unsere Energieketten der Serie 10. In den Tests, damals noch in Zusammenarbeit mit einem unabhängigen amerikanischen Institut, erzielten wir die Reinraumklasse 1 nach FED STD 209E. Speziell in den Bereichen Medizin, Pharma und der Elektronikfertigung werden Milliarden an Dollar pro Jahr in die Forschung und Entwicklung investiert. Die Anforderungen der Industrien stiegen und somit kamen auch immer mehr Anfragen bzgl. möglichst reinraumkonformen Igus Produkte. Das bedeutet: möglichst abriebsarme, kompakt gebaut oder elektrische leitfähige Produkte. Da alle drei Märkte Wachstumsmärkte sind, war es natürlich auch für uns an der Zeit die richtigen Lösungen für unsere Kunden zu entwickeln. So entstanden zum Beispiel unsere Energieführungsserien E3 und E6, welche wir bis heute an tausende Kunden aus den Bereichen Elektrofertigung, Medizin- und Pharmaindustrie beliefern. Wir sehen den Markt weiterhin stark wachsen und arbeiten mit Hochdruck weiter an neuen Innovationen für die nächsten Jahre.
Aktuell sind die Halbleiterindustrie (Elektronikfertigung) sowie die Medizintechnik- bzw. Pharmaproduktion Ihre Kernmärkte. Wie verteilen sich diese Märkte in Ihrem Portfolio? In welchen Märkten sehen Sie Wachstumspotenzial? Sehen Sie weitere Wachstumsmärkte?
P. Mattonet: Eine genaue Verteilung der Märkte für ganz Igus lässt sich schwer klar darstellen, aber wir können schon sagen, dass wir im Bereich Pharma/Medizin die Gewichtung eher im Produktbereich der Lagertechnik und im Bereich der Elektronikfertigung unsere Energieketten sehen. Projekte zu unseren recht neuen Produkten wie der e-skin flat Serie kommen meist auch noch aus der Halbleiter- oder Displayfertigung. Immer mehr Anfragen erreichen uns auch aus dem Bereich der Medizin. Hier sehen wir vor allem, dass unsere Produkte oft in „industrieähnlichen“ Maschinen und unter höchsten Reinraumbedingungen zur Probenentnahme und in speziellen medizinischen Apparaturen zum Einsatz kommen. Im Rahmen der Digitalisierung von Fabriken, Maschinen und Automobilen ist nach wie vor die Elektrofertigung eine unserer Hauptwachstumsmärkte. Aber auch im Bereich anderer herstellender Industrien, zum Beispiel in Druckmaschinen, Lackier- oder Hohnmaschinen sind Fremdpartikel unerwünscht, da Endprodukte kontaminiert werden können: Hier sehen wir immer öfter wie unsere Reinraumprodukte „zweckentfremdet“ werden.
Sie haben sich auf die Entwicklung von Kunststoffen für bewegliche Teile spezialisiert. Für gewöhnlich haben Kunststoffhersteller Kunststoffe im Sortiment. Sie bieten Lösungen für bewegte Teile an. Entwickeln Sie selbst Kunststoffe oder kaufen Sie Basiskunstoffe zu und modifizieren sie je nach Anwendung?
P. Mattonet: Bei unseren Werkstoffen handelt es sich um besondere Kunststoffmischungen, die auf Vermeidung von Verschleiß und Reibung optimiert sind. Dazu entwickeln wir jedes Jahr über 250 Kunststoff-Compounds. Unsere Polymere bestehen dabei aus Basispolymeren, Fasern und Füllstoffen sowie speziellen Additiven, die die Reibung vermindern. Alle Werkstoffe mischen, extrudieren, trocknen und verarbeiten wir selbst in Köln.
In Ihrem Testzentrum testen Sie viele Werkstoffparameter. Wie testen Sie Lebensdauer und Standzeiten? Welche tribologischen Untersuchungen machen Sie? Messen Sie dabei auch den Abrieb, die entstehenden Partikelgrößen und die Partikelanzahl?
P. Mattonet: Wir testen auf 3.800 m2 jährlich bis zu 15.000 Testaufbauten mit 10 Milliarden e-ketten Zyklen und bis zu 400 kundenspezifischen Tests. Darunter fallen rotierende, lineare, schwenkende Tests. Um noch bessere Aussagen für unsere Kunden machen zu können, haben wir 2020 in ein eigenes Reinraumlabor investiert. Hier haben wir die Möglichkeit unsere Produkte unter Reinraumbedingungen der ISO-Klasse 1 zu entwickeln und zu testen. Wir messen hier die Partikelemission nach Größe und Anzahl.
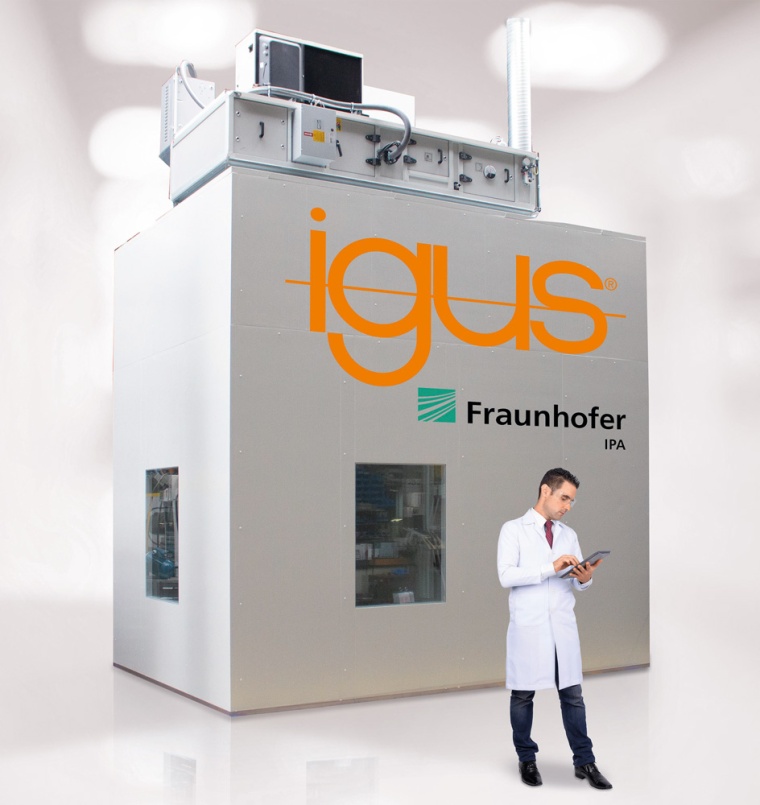
Ein geringer Verschleiß bedeutet kein Partikelverlust bzw. keine Partikelentstehung. Sind Ihre Kunststoffe (Kunststoffformulierungen) so gut, dass Sie Formulierungen für den Reinraum ohne (messbaren) Verschleiß haben? Wo liegt Ihr Geheimnis?
P. Mattonet: Igus entwickelt mehrere hundert neue Kunststoffcompounds für verschiedenste Anforderungen jedes Jahr. In den letzten zwei Jahren haben wir uns sehr auf Materialien für den möglichst partikelfreien Einsatz in Energieführungssystemen fokussiert und konnten zum Beispiel unsere neuen Materialien igulen CR1, igumer SK, igumer SKS und igumer SKS entwickeln. Diese setzen wir in unseren Neuheiten der e-skin flat und der C6 Familie ein. Das Geheimnis liegt in jahrelanger Erfahrung unserer Ingenieure aus der Entwicklung und vielen Testreihen mit verschiedensten Materialrezepturen. Kurz, die Kompetenz in Forschung, Entwicklung und Produktion und das anschließende Testen im Haus und beim Kunden hilft uns für jeden Anwendungsbereich das richtige Material zu finden.
Arbeiten Sie hier auch mit dem Fraunhofer IPA an „Reinraum“-Testkriterien? Oder Hauptsache „kein Verschleiß“?
P. Mattonet: Da unserer Reinraumtestlabor in Kooperation mit dem Fraunhofer IPA errichtet wurde, mit dem Ziel Grundlagenforschung zu betreiben, finden unsere Tests natürlich unter IPA Anforderungen nach DIN EN ISO 14644-1 : 1999 statt. Da wir aber auch immer das Letzte aus den Produkten rauskitzeln wollen, werden in Stress-Tests auch Extremanforderungen simuliert, um möglichst viele Erkenntnisse ziehen zu können. Die abschließende Zertifizierung nach DIN EN ISO 14644-1 : 1999 wird im Anschluss vom IPA Fraunhofer Institut durchgeführt.
Seit 2020 betreiben Sie in Korea eine Reinraum-Montage und Verpackung. Die Verpackung im Reinraum sehe ich als Komplettierung der „Reinraumproduktion“. Wäre es nicht sinnvoll die in Deutschland produzierten Halbschalen auch direkt in Korea zu produzieren, anstatt sie nach der Produktion in Deutschland nach Korea zur Montage und Fertigung im Reinraum zu senden? Und werden die Halbschalen in Deutschland nach der Produktion auch im Reinraum verpackt? Oder in Korea vor der Montage gereinigt?
P. Mattonet: Wie unser Unternehmer Frank Blase gerne sagt, der beste Chinese kommt aus Köln. Um die Kompetenz im Spritzguss und der Materialvorbereitung am besten kontrollieren zu können, kommen alle Spritzgussteile aus unserer Firmenzentrale in Köln. Anschließend werden die Teile als Schüttgut nach Korea versendet, gereinigt und im Reinraum verarbeitet, verpackt und zum Endkunden geschickt. Warum nur in Korea bisher? Weil wir hier die meisten Kunden haben, welche direkt in den Reinraum beliefert werden. Ansonsten werden unsere Komponenten noch durch mehrere Zulieferer verarbeitet und es finden doppelte Endreinigungen statt.

Sie berichten von einer Erweiterung Ihrer Reinraumfertigung in Köln, das heißt Montage und Verpackung. Dies sehe ich als logische Konsequenz und Expansion. Wie läuft die Umsetzung? Wann planen Sie mit der Fertigstellung?
P. Mattonet: Aktuell befinden wir uns in der Planungsphase und werden wohl in den nächsten Monaten mit der Umsetzung der Umbauarbeiten beginnen. Speziell für den europäischen Markt ist diese Erweiterung geplant, da wir auch hier einen steigenden Bedarf an Reinraumprodukten sehen.
2021 haben Sie beim Fraunhofer IPA Award REINER für Ihre Entwicklung „partikelfreie und kompakte e-skin flat Energieführung“ den zweiten Platz erzielt. Glückwunsch. Die Anerkennung Ihrer harten Arbeit und Mühen. Wir durften darüber in der ReinRaumTechnik bereits berichten. Und was dürfen wir jetzt von Igus erwarten?
P. Mattonet: Vielen Dank für die lobenden Worte! Ich kann nur soviel sagen, und zwar, dass wir aktuell schon an weiteren Entwicklungsstufen unserer e-skin flat arbeiten und auch im Bereich der „herkömmlichen“ Igus Energieführungsketten E6 und E6.1 weitere Neuheiten wie die C6 bereits im April als Beta-Studie vorstellen durften. Ich denke in den nächsten Jahren können Anwender weitere spannende Neuheiten für und um den Reinraum erwarten.