Industrieverbund für die Herstellung von Batteriesystemen
Um die Energiewende mit dem Ausstieg aus fossilen Antriebstechniken kurzfristig, mittelfristig oder langfristig zu erreichen, gelten Batterien als zentrale Energiespeichersysteme in elektrisch angetriebenen Fahrzeugen.
Autoren: Dr. Udo Gommel und Dr.-Ing. Frank Bürger, Fraunhofer IPA, Stuttgart
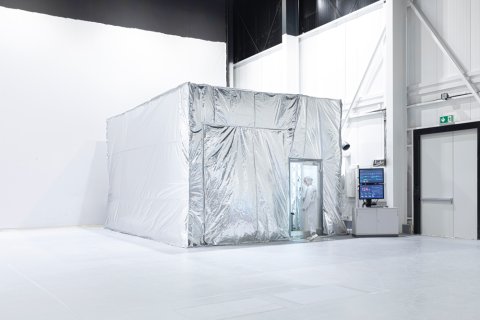
Die rasante Entwicklung von Elektroantrieben hat jedoch dazu geführt, dass die Nachfrage nach Batteriesystemen das Angebot und die Verfügbarkeit bei Weitem übersteigt. Daher wird die Verfügbarkeit elektrischer Batteriespeichersysteme zu einem entscheidenden strategischen Eckpfeiler, der die Wettbewerbsfähigkeit in verschiedenen Branchen beeinflusst, nicht nur in der Elektromobilität, sondern auch in der Elektrowerkzeugindustrie, Photovoltaikbranche und darüber hinaus – und somit auch den ge-sellschaftlichen Wohlstand. Infolgedessen versuchen Industrienationen, ihre Abhängigkeit von Anbietern aus anderen Weltregionen zu verringern, indem sie die Batterieproduktion ausbauen und steigern.
Bestehende Wettbewerbsnachteile in Europa, bedingt durch hohe Investitions- und Betriebskosten wie Arbeitslöhne, Energie und die Einhaltung von Umweltauflagen, können durch Wissensvorsprünge, ausgeklügelte Hochtechnologie, kosteneffiziente Produktionstechniken und spezifikationsgenaue Fertigungsanlagen ausgeglichen werden.
Die Weiterentwicklung von Batterietechnologien spielt zudem eine entscheidende Rolle bei der Verbesserung von Reichweite, Lebensdauer und Nachhaltigkeit von Energiespeichern. Unabhängig davon, ob Batterietechnologie als langfristige Lösung oder als Übergang zu Wasserstoffantrieben betrachtet wird, führt kein Weg an leistungsstarken und effizienten Batteriesystemen vorbei.
Inhalt:
- Herausforderungen der Batterieproduktion
- Batteriezellen, -module und -systeme
- Elektrodenherstellung, Montage und Validierung von Batteriezellen
- Assemblierung der Batteriezellen
- Die Montage
- Industriesupport: Aufbau des Industrieverbunds „Dry-Clean Suitable Materials“
- Dr. Udo Gommel
- Dr.-Ing. Frank Bürger
Herausforderungen der Batterieproduktion
Ein wesentlicher Kostenfaktor in der Herstellung von Elektrofahrzeugen sind die Batterien, die etwa 40 % der Gesamtkosten eines Elektroautos ausmachen. Zudem besteht eine erhebliche Abhängigkeit von Zulieferern aus Fernost, die rund 95 % der Batteriezellenproduktion ausmachen. Um diese Abhängigkeit zu reduzieren, ist der Aufbau eigener Fertigungskapazitäten in Deutschland und Europa erforderlich. Dabei müssen Herausforderungen wie eine schnelle und kosteneffiziente Produktion bewältigt werden.
Die Grundvoraussetzung ist ein zügiges Hochfahren der Produktionsstätten unter effizienten, wirtschaftlichen Rahmenbedingungen. Dass dies nicht immer erfolgreich ist, zeigen einige Initiativen der europäischen Batteriefertigung, die aktuell auf dem Prüfstand stehen oder bereits verschoben bzw. eingestellt werden mussten, da die immensen Hürden nicht erfolgreich überwunden werden konnten. Das Fraunhofer IPA möchte − mit einem Fokus auf Produktionstechnik und Automatisierung in der Zellproduktion unter herausfordernden, kontaminations- und feuchtekontrollierten Bedingungen − einen wesentlichen Beitrag zur Überwindung dieser technologischen Hürden leisten.
Die Entscheidung, ob die Strategie „Klasse statt Masse“ oder „Masse statt Klasse“ verfolgt wird, liegt bei jedem Automobilhersteller oder Batteriefertigungskonsortium. Es ist wahrscheinlich, dass insbesondere bei in Deutschland hergestellten Produkten der Fokus auf qualitativ hochwertigen Batteriesystemen mit geringen Ausfallraten liegen wird. Die Herstellung von Batteriezellen ist jedoch ein komplexer Prozess, der höchste Qualitätsanforderungen an die Reinheit und Trockenheit in den folgenden Herstellungsphasen stellt.
Batteriezellen, -module und -systeme
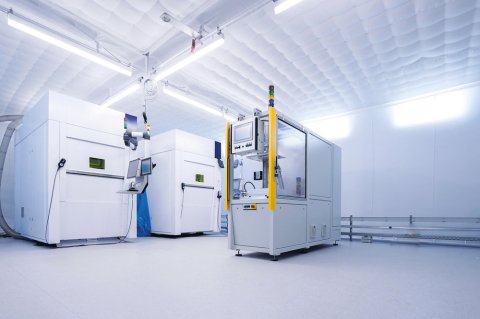
Die Produktion von Batteriezellen, -modulen und -systemen setzt sich aus drei elementaren Bausteinen zusammen: der Produktionsstätte, der Produktionstechnik (d. h. Anlagen, Ausrüstung etc.) und den Fertigungsprozessen. Zunächst muss das Thema vom Ende her betrachtet werden: Ausgehend von der übergeordneten Aufgabe, eine funktionierende Batterie zu entwickeln, konzentrierten sich die Wissenschaftler und Ingenieure zunächst auf die zentralen chemischen Kernprozesse, die in einer Batteriezelle ablaufen. Hierbei sind zahlreiche Fertigungsprozesse und qualitätsrelevante Faktoren zu berücksichtigen. Nachdem diese Einflussfaktoren bekannt sind, muss der nächste Schritt erfolgen, um von funktionierenden Prototypen im Labormaßstab zur Herstellung marktfähiger Systeme zu gelangen, die sowohl die Qualitätsanforderungen als auch die Kostenbedarfe erfüllen. Hierfür ist angepasste Produktionstechnik erforderlich, die alle Prozessschritte in der benötigten Qualität und Geschwindigkeit ermöglicht. Übergeordnet werden die äußeren Rahmenbedingungen werden durch die Produktionsumgebung (z. B. Rein- und/oder Trockenraum) realisiert.
Bei allen drei elementaren Bausteinen (Fertigungsprozess, Produktionstechnik, Produktionsumgebung) hat sich gezeigt, dass die Reduktion von Verunreinigungen und Feuchte zu leistungsfähigeren Batteriezellen führt. Zudem müssen die Produktionstechnik und die darin enthaltenen Fertigungsanlagen auf extreme Hochautomatisierung ausgelegt sein, um die für eine wirtschaftliche Batterieproduktion erforderlichen hohen Stückzahlen pro Tag zu erreichen. Großkonzerne planen Batteriefertigungen, die jährlich bis zu zwei Millionen Autos mit dort hergestellten Batterien versorgen können.
Im Folgenden wird ein kurzer Überblick über die wichtigsten Prozessschritte gegeben, um zu prüfen, ob Anforderungen an die Produktionstechnik und -umgebung, insbesondere aus kontaminationstechnischer und feuchtekontrollierter Sicht, berücksichtigt werden müssen.
Elektrodenherstellung, Montage und Validierung von Batteriezellen
Die Elektrodenherstellung ist ein entscheidender Schritt in der Produktion von Batteriezellen. Zunächst erfolgt die Pastenherstellung für Kathode und Anode durch das Mischen hochreiner Wirkstoffe und Lösemittel. Die Reinheit der Ausgangsmaterialien ist entscheidend, um die Leistungsfähigkeit der herzustellenden Batteriezelle nicht zu beeinträchtigen. Unabhängig von der geometrischen Bauform (pouch, zylindrisch, prismatisch) müssen Querkontaminationen bei der Herstellung der Elektroden (Anode aus z.B. graphitbeschichteter Kupferfolie, Kathode aus z.B. NMC-beschichteter Aluminiumfolie) strikt vermieden werden. Hierfür müssen separate Fertigungslinien für die Elektroden aufgebaut werden.
Da NMC gesundheitsschädlich ist, muss sichergestellt werden, dass diese toxischen Substanzen weder die Mitarbeiter noch die Umwelt belasten. Dies bedingt extrem hohe Anforderungen an Absauganlagen, Filtrationstechnik und reinheitskontrollierte Umgebungen. Eine angepasste Reinheitstechnik ist hierbei unabdingbar. Die Elektrodenfolienherstellung umfasst mehrere Schritte: Zunächst erfolgt eine hochpräzise beidseitige Beschichtung der Trägerfolien aus Kupfer und Aluminium. Anschließend wird eine graduelle Trocknung der beschichteten Folien durchgeführt, um das Lösungsmittel gleichmäßig zu entziehen. Durch das Kalandrieren mit rotierenden Walzen wird die Schichtdicke auf den Elektrodenträgerfolien konstant gehalten und die Haftung der Beschichtungen verbessert. Beim „Slitting“ werden die Folien in Bänder geschnitten, um die geometrischen Anforderungen der Elektroden zu erfüllen. Die Vakuumtrocknung sorgt schließlich für eine optimale Trocknung der Materialien. Digitale Datenerfassung und KI-gestützte Auswertungen ermöglichen es, geringste Sollwertabweichungen sofort zu erkennen und anzupassen.
Assemblierung der Batteriezellen
Die Assemblierung der Batteriezellen erfolgt in mehreren hochpräzisen Schritten. Zunächst werden die Elektroden durch „Notching“, d. h. Schneiden, in rechteckige Formen gebracht. Dies geschieht entweder mechanisch oder mittels eines Laserschneidverfahrens, das ein geringeres Risiko von Querkontaminationen ermöglicht.
Im nächsten Schritt erfolgt das „Stacking“, bei dem die Elektrodenfolien, Separatoren und Kathoden in wiederholenden Zyklen gestapelt oder gewickelt werden. Höchste Präzision und Sauberkeit sind erforderlich, um Kurzschlüsse zwischen Elektrode und Anode durch überstehende Separatorfolien oder Partikelkontaminationen zu vermeiden. Anschließend wird der elektrische Anschluss von Kathode und Anode hergestellt. Nach dem Stapeln erfolgt die Montage der Komponenten, die das Anschweißen der Elektroden an die Hauptkontakte sowie das Zusammenfügen von Gehäuse, Deckel, Dichtungen und Sicherheitsventilen umfasst.
Die Montage
Die Montage muss unter extrem trockenen Bedingungen erfolgen, da Feuchtigkeit zu einer Degradation der Elektroden (Bildung von Lithi-
umhydroxid) und damit zu einem Leistungsabfall der Batteriezelle führen kann. Diese Arbeiten müssen unter Trockenraumbedingungen durchgeführt werden, die oft einen Taupunkt von mindestens -40 °C erreichen müssen. Materialien wie NMC811 oder Lithiummetalle erfordern sogar noch tiefere Taupunkte und somit noch trockenere Umgebungsbedingungen.
Nachdem die Zellen montiert sind, erfolgt die Überprüfung in mehreren Schritten. Zuerst wird die Zelle mit Elektrolyt befüllt, gefolgt von der Formierung und Konditionierung, die das erstmalige Be- und Entladen der Zellen umfasst und bis zu 24 Stunden dauern kann.
Die Alterung der Batterien erfolgt durch Lagerung bei erhöhten Temperaturen über mehrere Wochen, um Kurzschlüsse zu identifizieren und die Zelleigenschaften zu bestimmen. Mehrere Batteriezellen werden in Reihe geschaltet, um ein Batteriemodul zu bilden, aus dem dann das gesamte Batteriesystem entsteht. Abschließend werden die Systeme getestet, um die Ausfallsicherheit der Batterien zu überprüfen.
Insgesamt erfordert die Elektrodenherstellung und Montage von Batteriezellen höchste Präzision und Reinheit, um die Leistungsfähigkeit und Sicherheit der Endprodukte zu garantieren.
Dadurch ergeben sich extreme Anforderungen an die Einsatzfähigkeit und Tauglichkeit der Fertigungsanlagen für den Betrieb unter diesen extrem trockenen Umgebungsbedingungen, verbunden mit hohen Anforderungen an die Reinraum- und Reinheitstechnik. Dies steht im diametralen Gegensatz zum Wissen über den Dauerbetrieb dieser Anlagentechnik unter solchen extremen Bedingungen.
Taupunktvorgaben von -40 °C bis -50 °C führen dazu, dass aufgrund der Abwesenheit selbst geringster Mengen an Restfeuchte in der Umgebungsluft kaum freie Wassermoleküle mehr in der Produktionsumgebung vorhanden sind, die als Schmierstoff zwischen den tribologisch belasteten Werkstoffen der Fertigungsanlagentechnik fungieren könnten. Diese Situation resultiert in erhöhten Reibbelastungen und damit in einem deutlich schnelleren Verschleiß der Produktionsanlagen. Voruntersuchungen am Fraunhofer IPA in speziell dafür eingerichteten DryClean-Environments, in denen sowohl die trockenen als auch die sehr reinen Umgebungsbedingungen präzise eingestellt werden können, zeigten ein Verschleißverhalten, das teilweise um den Faktor 1.000 höher lag im Vergleich zu klassischen Fertigungsbedingungen mit einer relativen Luftfeuchtigkeit von ca. 45 % r.F.
Zur wissenschaftlichen Erforschung dieser herausfordernden Produktionsbedingungen hat das Fraunhofer IPA mehrere Analysezellen aufgebaut, sowohl eigenständig (s. Aufmacher) als auch in Zusammenarbeit mit Spezialisten der Reinraum- und Trockenraumbranche. Diese Umgebungen ermöglichen die systematische Analyse der wissenschaftlich abgesicherten Wechselwirkungen zwischen der feuchtereduzierten Fertigungsumgebung und den damit verbundenen Degradationen der verwendeten Produktionsanlagentechnik, sowie der darin verbauten Materialien und Werkstoffe.
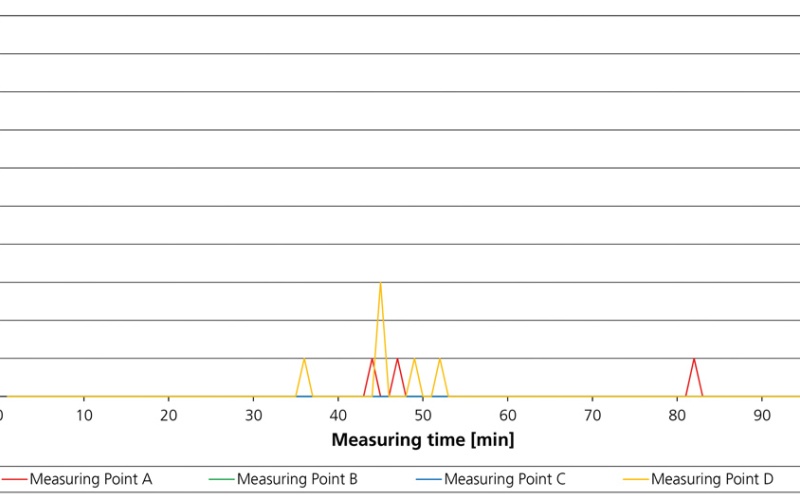
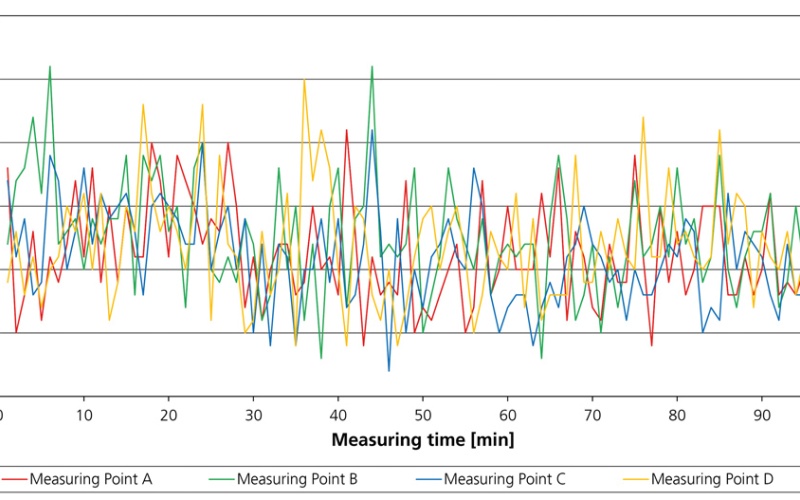
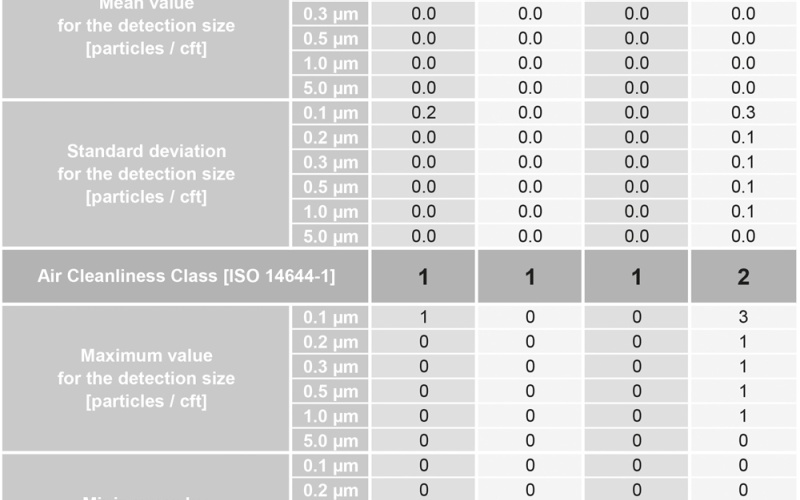
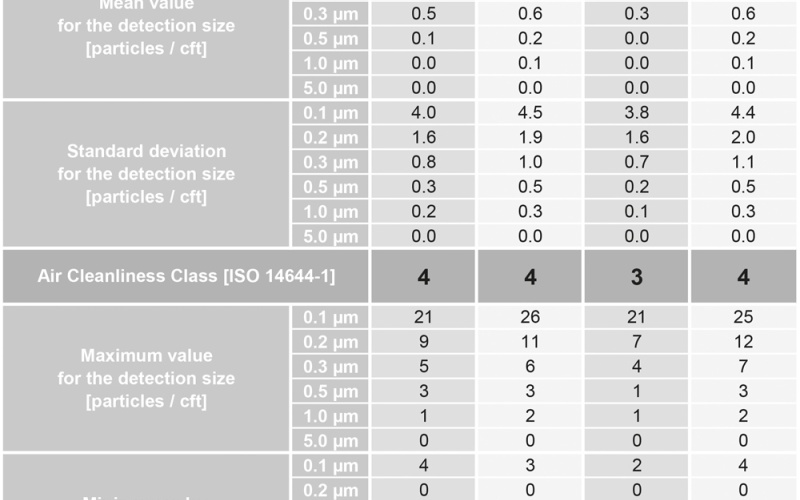
Industriesupport: Aufbau des Industrieverbunds „Dry-Clean Suitable Materials“
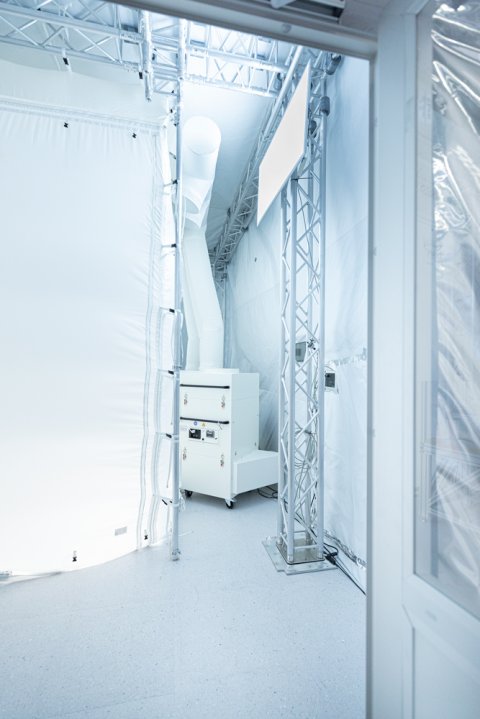
Im Mittelpunkt des in Gründung befindlichen Industrieverbunds „Dry-Clean Suitable Materials“ steht die gemeinsame Entwicklung von Verfahren zur Bewertung und Selektion von Hardwarekomponenten. Diese sollen unter systematisch abgestimmten Belastungsszenarien als Werkstofftests sowie an repräsentativen Automatisierungssystemen erprobt werden. Aufbauend auf den spezifischen Bedarfen und zu realisierenden Belastungsszenarien, die im engen Erfahrungs- und Wissensaustausch zwischen den beteiligten Industriepartnern und dem Fraunhofer IPA erarbeitet werden, sollen der Industrie diverse Werkzeuge zur Auswahl kompatibler Werkstoffe und Materialien an die Hand gegeben werden.
Darüber hinaus sollen Vorgehensweisen sowie ein Leitfaden mit Handlungsempfehlungen zur systematischen Auslegung von Neuanlagen (Equipment-Design) für diese speziellen trocken- und reinheitskontrollierten Umgebungsbedingungen entwickelt werden. Auch die Optimierung bestehender Fertigungen wird im Fokus des Industrieverbunds stehen.
Zunächst ist eine Übersicht über bereits in der Industrie und der Forschungslandschaft verfügbare Methoden und Vorgehensweisen erforderlich. Diese Analyse, die durch Sichtung von Veröffentlichungen und Literatur erfolgt, wird als einer der ersten Schritte durchgeführt.
Ein zentraler Schwerpunkt, der nur gemeinsam von Forschung und Industrie erarbeitet werden kann, ist die Beantwortung der Frage, wie viel Trockenheit in Kombination mit den Reinheitsanforderungen tatsächlich für qualitätsentscheidende Prozessschritte erforderlich ist. Da beide Faktoren erhebliche Kostentreiber der Produktion darstellen, sollen Handlungsbedarfe erarbeitet und die größten Hebel für eine kosteneffiziente Produktion identifiziert werden. Des Weiteren ist eine Technologiebegleitung in Form der Erstellung von Best-Practice-Vorgehensweisen, dem kosteneffizienten Betrieb von Rein- und Trockenbereichen sowie dem Upscaling von Produktionsanläufen geplant. Auch die Sammlung und Erstellung von Expertenpapieren und Regelwerken zur kosten-, zeit- und spezifikationseffizienten Produktion unter Trockenreinraumbedingungen werden den Teilnehmern des Industrieverbunds als mögliche Schwerpunkte angeboten.
Speziell im DryClean-Anwendungsbereich der Batterieproduktion hat sich das IPA mit seinem umfangreichen produktionstechnischen Know-how zu einem zentralen Knotenpunkt entwickelt, der wesentliche Beiträge zur kosteneffizienten und qualitativ zuverlässigen Batterieproduktion leistet. Neben der Batterieprozesstechnik hat sich das IPA der wissenschaftlichen Weiterentwicklung der Produktionsumgebung, einschließlich der spezifischen Fertigungsumgebungen für Trockenreinräume, verschrieben.
Getreu dem Motto „Viele helfende Hände, schnelles Ende“ können die Teilnehmer des Industriekonsortiums einen erheblichen Hebel für eine zeit-, kosten- und qualitätseffiziente Produktion nutzen. Mit einem Aufwandsdeckungsbeitrag pro Teilnehmer und einer Gesamtteilnehmerzahl von ca. 20 bis 25 Firmen sollten zahlreiche Arbeitspunkte umgesetzt werden, von denen alle Teilnehmer in vollem Umfang profitieren.
Die folgenden Teilnehmergruppen sind geeignet, um die Ziele und Potenziale des Industrieverbunds optimal zu erreichen: Zulieferindustrie, Werkstoffhersteller, Anlagenbauer, Prozesstechnik sowie Anwender/Nutzer der Trockenreinraumtechnik.
Die Kick-off-Veranstaltung ist für den Spätsommer bzw. Herbst 2025 geplant und soll eine Laufzeit von ca. zwei Jahren haben. Sollte sich während der Laufzeit des Industrieverbunds herausstellen, dass für die Bearbeitung weiterer wichtiger Themen zusätzliche Kapazitäten oder Zeiten benötigt werden, besteht die Möglichkeit, eine fortführende Phase des Industrieverbunds anzuschließen. In bereits vorausgegangenen Industrieverbünden wurden damit sehr gute Erfahrungen gesammelt.
Einladung zur Teilnahme am Industrieverbund „Trockenreinraumtaugliche Werkstoffe“
Haben Sie Interesse mitzuwirken, dann melden Sie sich direkt an:
Anmeldung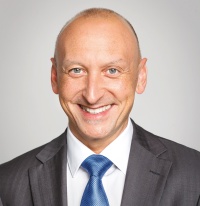
Dr. Udo Gommel
Projektleiter Fraunhofer IPA, Stuttgart
© Fraunhofer IPA
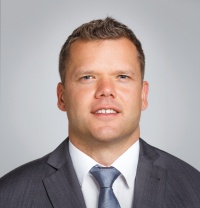
Dr.-Ing. Frank Bürger
Projektleiter, Fraunhofer IPA, Stuttgart
© Fraunhofer IPA