Reinraum-Tücher-Ökologie zwischen Nachhaltigkeit, Partikelfreisetzung und Preis
HiTech-Wischmittel wie Reinraum-Tücher, Schwämme, Swabs und Mops sind aus Gründen der Vermeidung von Kontaminations-Verteilung (spreading) zum großen Teil Einweg-Produkte. Von daher sind sie nach Gebrauch Plastik-Müll wie auch Plastikflaschen oder Becher. Das heißt: Der Anwender muss sie entsorgen – entweder in der Müllverbrennungs-Anlage oder auf der Kippe. Beides ist Grund genug, sich des Themas Nachhaltigkeit näher anzunehmen.
Autor: Win Labuda, Clear & Clean, Lübeck
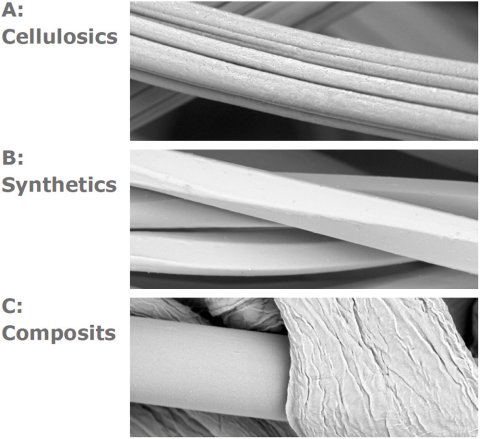
HiTech-Reinigungs-Tücher sind auch unter dem Begriff „Reinraum-Tücher“ – engl. cleanroom wipers oder einfach wipes bekannt. Wir gebrauchen diesen Begriff jedoch ungern, weil er im Zusammenhang mit dem Raumbegriff fälschlich mit „Raumpflege-Tüchern“ verwechselt werden kann.
Reinraum-Tücher lassen sich entsprechend der Rohstoffe, aus denen sie bestehen, in drei Kategorien einteilen:
- A- Cellulosics: Tücher aus Cellulose-haltigen Polymeren (Viskose, Cupro) Cellulosics werden heute ausschließlich als Vliestücher gefertigt.
- B- Synthetics: Tücher aus synthetischen Polymeren (Polyester, Polyamid, Polypropylen) Synthetics werden als Vliestücher, Gestricke und Gewebe gefertigt.
- C- Composits: Tücher aus einem Mix von Holz- schliff + Polyester oder Polyester + Polyamid- Composits werden sowohl als Vliestücher und als Bikomponent-Garn-Gestricke gefertigt.
Schwerpunkt Nachhaltigkeit

Viele von uns kennen aus dem Fernsehen den Video-Film mit der Meeresschildkröte, die verheddert in einem Plastikbeutel über ihrem Kopf – in wirren Bögen dem sicheren Tod entgegen schwimmt.
Millionen Tonnen von Plastikteilen haben unsere Meeresfauna erreicht und werden für diese zur lebensgefährdenden Bedrohung. Solange uns die Entsorgungswege unserer industriellen Abfallprodukte weitgehend verbor- gen bleiben, müssen potenziell auch benutzte Reinraumtücher der HiTech-Industrien dazu gerechnet werden – es sei denn sie bestehen aus Materialien der Gruppe A, und sind innerhalb überschaubarer Zeiträume biologisch abbaubar. Wir von Clear & Clean glauben, dass die ökologische Unbedenklichkeit unserer Materiaauswahl nicht erst in ferner Zukunft die wichtigste Voraussetzung für die Nachhaltigkeit unseres Unternehmens ist, sondern schon jetzt. Wir haben daher bereits im Jahr 2019 mit eigenen Verrottungs-Studien für Viskose-Produkte begonnen. Künftig werden weitere Produkte in die Studie eingegliedert werden. In diesem Kontext ist neues Bildmaterial entstanden, welches das Phänomen der Verrottung unserer Cellulosics im Erdreich in bester Weise aufzeigt.
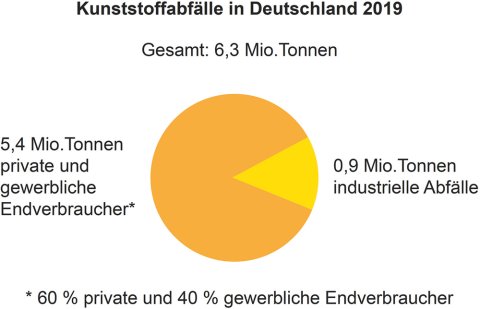
Das Entsorgungsproblem gewinnt auch dadurch an Momentum, dass China sei- nen Polymer-Müll-Import aus Deutschland ab 1.1.2019 von 460.000 auf 13.000 t/p. a. reduziert hat und auch Malaysia und Vietnam Import-Reduzierungen vorgenommen haben.
Die Anlieferer bei den 29 deutschen Müllver- brennungsanlagen klagen nun naturgemäß über zu geringe Verbrennungskapazitäten. Im Prinzip gehört ein Teil der HiTech-Reinigungstücher aus synthetischen Polymeren etwa zur Hälfte zum wieder verwertbaren Kunststoffabfall. Dies ist jedoch nicht der Fall, wenn es sich um Bikom- ponent-Tücher mit einem Faser-Mix aus einer Polyester-Polyamid oder Polyester-Holzschliff- Kombination handelt.
Weder die Politik noch die großen Produktanwender können und werden sich aufgrund des zunehmenden Drucks „von der Straße“ der Plastik-Müll-Problematik länger verschließen. Hinzu kommt, dass mit dieser Problematik möglicherweise auch das Mikroplastik-Problem einhergeht. Direkte Korrelationen zwischen Plastikmüll- und Mikroplastik-Vorkommen sind uns noch nicht bekannt geworden. Es gibt aber Vermutungen, die in diese Richtung weisen. Weil die von uns gefertigten Produkte Fasern von 5 – 10 µm Durchmesser enthalten ist es für uns wichtig zu erfahren, was mit den von uns gefertigten Produkten endlich geschieht und ob sie einen Beitrag zur Mikroplastik-Problematik leisten oder nicht.
Wischmittel-Anwendungen in den HiTech-industrien sind bspw.:
- Partikel von Oberflächen entfernen
- Flüssigkeitslachen aufnehmen
- gereinigte Teile trockenwischen
- Schmierfilme lösen und entfernen
- Lack- und Farbreste entfernen
- reinigende Klebeflächen-Vorbereitung
- Flüssigkeiten und Cremes auftragen
- Moppreinigung in reinen Bereichen
- Präzisionsreinigung optischer Glasflächen
- Beschichtungs-Vorbereitung
- Schnäuz- und Brillen-Reinigungs-Tücher
- analytische Probenahmen durch Swabs
Bei den oben angeführten Anwendungen muss sichergestellt sein, dass es zu keiner oder lediglich minimaler Rückübertragung der Verunreinigungen aus der Tuchmatrix hin zu den verunreinigungsempfindlichen Objekt- Oberflächen kommt. Das betrifft auch die partikuläre Verunreinigung, die im höheren Maße bei der Anwendung von Tüchern der Gruppe A – Cellulosics entsteht als bei denen der Gruppen B – Synthetics und C – Com- posits. Bei der Gruppe C ist die gegebene Wahrscheinlichkeit einer solchen Übertragung unterschiedlich verteilt. Während die Tücher der Polyester-Holzschliff-Kombination durch- aus eine gewisse Tendenz zum Hinterlassen partikulärer Oberflächen-Verunreinigung auf- weisen, ist dies bei der Polyester-Polyamid- Kombination deutlich weniger der Fall.
Um zu gewährleisten und zu demonstrie- ren, dass die von den Premium-Herstellern gefertigten Produkte für das wischende Rei- nigen spezifikationsgemäß und unter Einhal- tung angemessen hoher Reinheits-Standards gefertigt sind, unterhalten diese ein analytisches Labor. Manche, wie Clear & Clean veröffentli- chen die QS-Daten für die wichtigsten Produkte im Internet.
Cellulosics
Mit Cellulosics werden Wischmittel-Produkte bezeichnet, die zum größten Teil aus Zellu- lose-haltigen Stapelfasern bestehen und im Spunlace-Verfahren vervliest sind. Es ist nicht grundlos, dass in dieser Schrift den Cellulosics-Produkten mehr Raum gewidmet ist als den Synthetics. Das steht mit der Tatsache im Zusammenhang, dass wir von Clear & Clean gedanklich von dem Wunsch geleitet sind, eines Tages alle Prozeduren des wischenden Reinigens mit Hilfe biologisch abbaubarer Pro- dukte zu bewältigen. Dieser Wunsch kann – wenn überhaupt – nur unter Einbeziehung von Cellulosics in Erfüllung gehen. Dies ist schon deswegen so, weil allein Cellulosics die Mög- lichkeit der tensidfreien Flüssigkeits-Aufnahme auf der Basis naturgegebener Kapillarität gewährleisten und sie zudem die einzige Per- spektive biologischer Abbaubarkeit eröffnen (siehe Abb.).
Vielen stellt sich in diesem Zusammen- hang die Frage warum Viskose dann oftmals als „Chemiefaser“ bezeichnet wird. Der Stoff besteht doch hauptsächlich aus Zellulose, die ursprünglich aus Holz gewonnen wird. Die Ant- wort steht nicht im Zusammenhang mit dem eingesetzten Material Holz sondern mit dem Fertigungsprozess. Um Viskose zu gewinnen, wird die Zellulose mit Hilfe aggressiver Chemi- kalien aufwändig bearbeitet
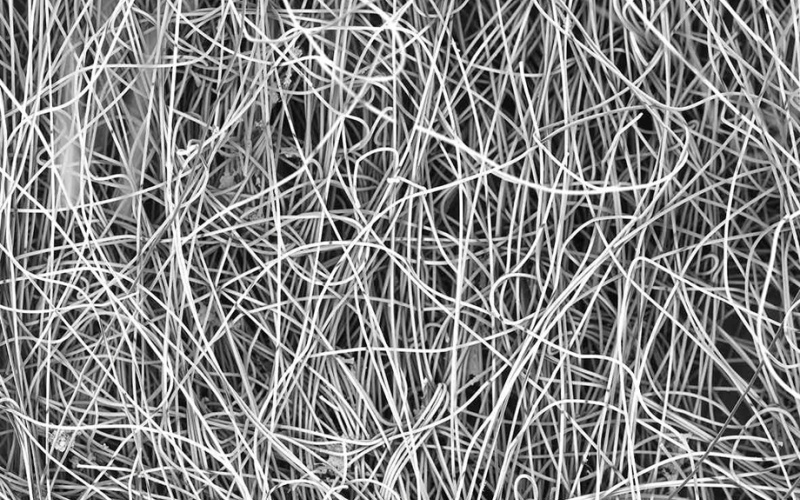
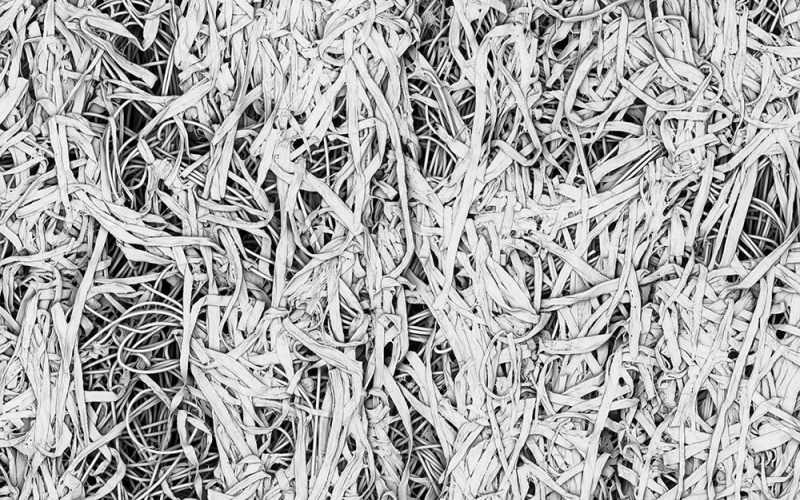
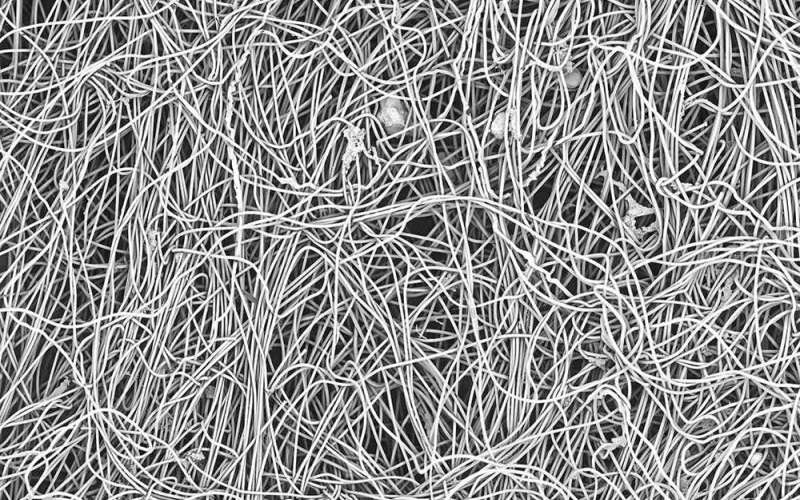
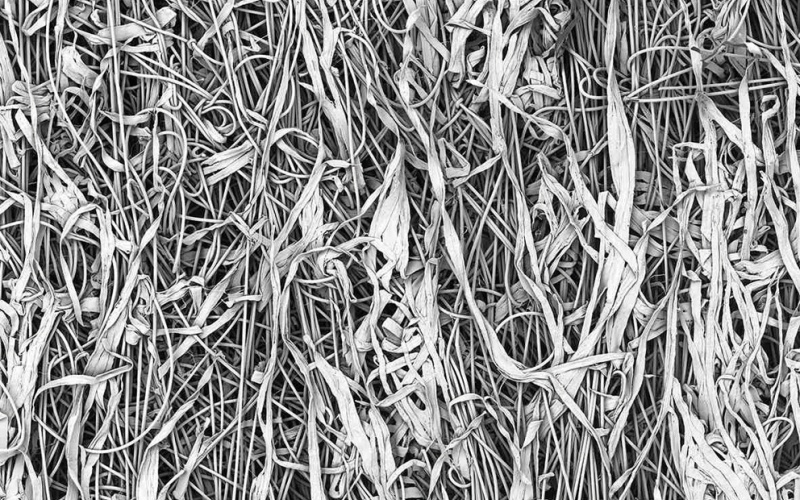
Viskose (CV)
Viskosefasern sind mittlerweile angemessen preiswert, sodass es möglich ist, aus ihnen ökonomisch interessante Wischmittel zu ferti- gen. Sie haben auch eine ganze Reihe Wisch- mittel-kompatibler Eigenschaften. Lediglich die eingeschränkte Abriebfestigkeit/bzw. erhöhte Partikelfreisetzung mindert ihre Attraktivität für den Einsatz als HiTech-Wischmittel – Viskose hat viele Eigenschaften, die sich insbesondere für den Wischmittel-Bereich als günstig erwei- sen, sodass dem Material in seinen mehrfach verbesserten Ausführungen eine technolo- gisch und ökonomisch aussichtsreiche Posi- tion einnehmen könnte. Dies soll nicht heißen, dass für die Präzisionsreinigung ausgewählter Oberflächen nicht auch weiterhin mehrfach dekontaminierte Synthetics-Produkte Einsatz finden werden.
Die Viskose-Herstellung
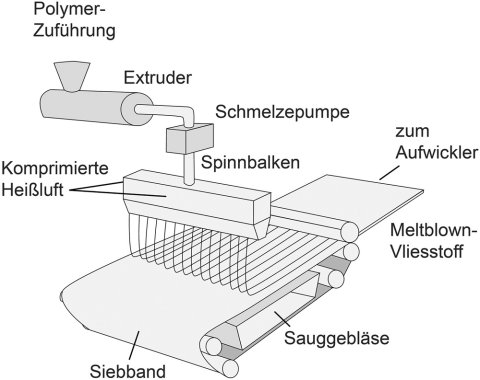
Die Viskosevlies-Herstellung vollzieht sich im Prinzip in drei aufeinander folgenden Schritten:
- Aufbereiten der Spinnmasse
- Spinnvorgang durch Fällen
- Nachbehandlung
Das Ausgangsmaterial ist Zellulose (C12H20O10) von hohem Reinheitsgrad. Im ersten Prozessschritt wird dem Zellstoff Natronlauge NaOH hinzugegeben um seine Mercerisierung (Quellung) zu bewirken. Anschließend erfolgt die Zugabe von Schwefelkohlenstoff CS2 (Xanthat). Zum Erhalt einer reinen Masse erfolgt eine mechanische Filterung. Danach ist es unverzichtbar, die filtrierte Masse eine bestimmte Zeit lang lang reifen zu lassen.
In der zweiten Fertigungsstufe erfolgt der eigentliche Spinnvorgang: Zunächst wird ein Spinnbad aus Schwefelsäure zubereitet und diesem sowohl Natrium-Sulfat als auch eine geringe Menge Zinksulfat hinzugegeben. Die Masse wird mittels einer Zahnradpumpe durch eine Düsenplatte welche mit Spinndüsen im Durchmesser von 0,05 mm versehen ist, hin- durchgepresst. Dabei nehmen die etwa 10 µm dicken Materialstränge feste Form an. Es entstehen Viskosefäden (siehe Abb.).
In der dritten und letzten Fertigungsstufe erfolgt eine Nachbehandlung. Das Material wird dabei chlorfrei gebleicht und mit einer Tensid- Avivage im Promille Massen-Bereich versehen und getrocknet.
Förderliche Ausgestaltungsformen des oben erläuterten Viskose-Prozesses finden sich in Prozessen für die ausschließlich Zellstoff aus Buchenholz-Schliff verwendet wird, Auf diese Weise ist es möglich erhöhte Filament- bzw. Faser-Festigkeitswerte zu erhalten.
Lange Zeit unerwünschter Aspekt des Viskose-Prozesses sind die im Prinzip umweltschädlichen Chemikalien des Fällbads. (Schwefelsäure, Natrium-Sulfat und Zinksulfat) Man suchte also längere Zeit nach einem ungiftigen wenngleich wirkungsvollen Fällbad. Dies fand man in dem Lösungsmittel N-Methyl-Morpholin-N-Oxyd, das ungiftig ist.
Dieser sog. Prozess erlaubt heute die modernste und effektivste Viskose- Fabrikation zudem mit erhöhter Faserfestigkeit.
Die Faserfestigkeiten der verschiedenen Ausbildungsformen der Viskose (Cellulosics) im Vergleich mit zwei Synthetics sind wie folgt:
(in cN/dT- trocken/nass/Feuchteaufnahme)
Cupro | 15–20 | 9–12 | 100 % |
Viskose | 20–26 | 10–15 | 100 % |
M-HWM | 34–36 | 19–24 | 75 % |
MP | 36–42 | 20–30 | 60 % |
TEN | 38–47 | 26–40 | 65 % |
im Vergleich zwei Synthetics-Materialien:
Polyester | 30–95 | -- | 0,3 % |
Polyamid 6 | 30–80 | -- | 12 % |
Anwendungs-Eigenschaften der Viskose
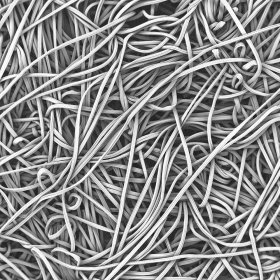
Viskose hat viele Eigenschaften, die das Material für HiTech-Anwendungen interessant machen. Dies trifft insbesondere zu wegen sei- ner ausgeprägten Absorptions-Eigenschaften für Lösungsmittel und andere Flüssigkeiten. Grundvoraussetzung ist jedoch, dass Viskose- Tücher während ihrer Handhabung mecha- nisch nicht übermäßig beansprucht werden. Nachstehend ein Eigenschaftskatalog von Viskose-Tüchern:
- kompostierbar oder teilkompostierbar
- sehr saugfähig
- Flächen-schmiegsam
- mittelmäßige Strapazierbarkeit
- geringe Riefenbildung beim Wischen
- geringe elektrostatische Aufladbarkeit
- geringe Dichte
- angenehme Haptik
Von höchster Bedeutung für den Spinnvorgang von Cellulosics-Garnen von Cellulosics-Garnen ist die Spinndüsenfertigung unter Zuhilfenahme der Laser-Technik. Stand der Technik sind Laser-gefertigte Nass- Spinndüsen-Platten mit 950 Bohrungen eines mittleren Durchmessers von 25 µm. Mithilfe dieser Technologie ist es möglich Cellulose zu Mikrofilamenten mit Filament-Feinheiten von 0,2 dTex zu spinnen. Das entspricht etwa einer Masse von 20 g für einen Spinnfaden, der von Lübeck bis nach Salzburg reicht.
An der Universität Stuttgart, wo man sich mit der Technik des Ultra-Microspinnens in Zusam- menarbeit mit dem Institut für Textilchemie und Chemiefasern in Denkendorf intensiv beschäftigt hat, ist es gelungen, mit Zellulose 1-Ethyl-3-methyl-imidazolium-acetat (EMIM OAc) und Cellulose-2.5-acetat/Aceton unter Einsatz von Düsen mit Bohrungsdurchmessern von 25 µm endlose Super-Mikro-fasergarne mit Filament-Feinheiten unter 0,2 dTex zu fertigen. Es ist gut möglich, dass es mit Filamenten dieser Feinheit gelingen kann, Partikel im Bereich von 80 nm und weniger Feret-Durchmesser von Objekt-Oberflächen durch wischende Reinigungs-Vorgänge zu entfernen und zu binden. Um dies sicherzustellen, müsste man die Materialfestigkeit solcher Filamente und deren Abriebfestigkeit bzw. Partikel-Eigenstreuung untersuchen.
Es gibt jedoch – die Viskose betreffend – einige weniger günstige Eigenschaften, die beim Einsatz als HiTech-Wischmittel nicht außer Acht gelassen werden dürfen. Das sind:
- geringe Abriebfestigkeit
- Partikelfreisetzung bei Wischvorgängenauf rauen Oberflächen
- erhöhte Lichtempfindlichkeit (Gilb)
- gering ausgeprägte Schimmelfestigkeit
- reduzierte Faserfestigkeit im Feuchtzustand
insbesondere auch im Reinraum-Tücher-Bereich. Es können allerdings Filament-Durchmesser von kleiner 4 µm erreicht werden.
Cupro (CU)
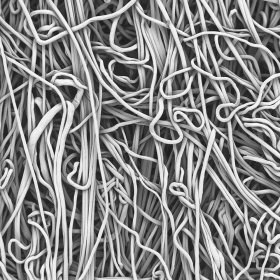
In den zwanziger Jahren des vorigen Jahrhunderts wurde in Deutschland als Seiden-Ersatz ein Kupferoxid-Ammoniak-Verfahren (Cupro) patentiert und nach dem Krieg in Japan weiterentwickelt. Seitdem hat es wegen der hochreinen Endlos-Filamente in den HiTech-Industrien, trotz sehr hoher Abgabepreise im 3-fachen Viskose-Bereich, ein hohes Maß an Bedeutung für Fein- und Präzisions-Reinigungs-Aufgaben in Reinheits-kontrollierter Umgebung erlangt. Dem Material wird eine erhöhte Aceton-Verträglichkeit nachgesagt, was wir bisher jedoch noch nicht untersucht haben. Entsprechende Versuche sind geplant.
Synthetics
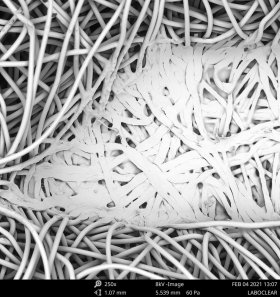
Etwa die Hälfte der z. B. bei den Reinraum- Betreibern eingesetzten Wischmittel müssen den Synthetics zugeordnet werden. Das sind solche Wischmittel, die aus den synthetischen Polymeren Polyester, Polyamid oder Polypropylen bestehen. Sie werden entweder als Spinnvlies, Spunlace-Vlies gefertigt oder aber als Multifilament-Garn zum Gestrick verar- beitet. Danach werden Gestricke im Spann- rahmen bei erhöhter Temperatur gereckt und fixiert. Anschließend müssen sie in speziellen Laser-Schneidmaschinen formatiert – also in ihre endliche Form und Abmessung – gebracht werden. Danach erfolgt im Reinraum ein mehr- stufiger Dekontaminations-Prozess bevor die Tücher mit einem nichtionischen Tensid ausgerüstet werden. Die Tensid-Ausrüstung wird notwendig, weil Polyester von Natur aus hydrophob ist – also für Wasser und wässrige Lösungsmittel abweisend. Danach erfolgen die stichprobenartigen Prozeduren der Quali- tätssicherung und ihre sorgfältige Dokumen- tation. Die so gewonnenen QS-Daten werden anschließend im Internet öffentlich gemacht. Zuguterletzt werden die Tücher gelegt oder geschüttet und verpackt. Synthetics-Wisch- mittel sind teuer in der Herstellung aber unver- zichtbar für die Fein- und Präzisions-Reinigung strukturierter Oberflächen wie feinmaschiger Siebe im Hybrischaltungsdruck.
Es ist angemessen in diesem Aufsatz die verrottbaren Synthetics nicht außer Acht zu lassen. Gibt es seitens der Polyester-Hersteller wie bspw. der BASF offenbar Pläne biologisch abbaubare Polyester zu entwickeln, aber bisher wissen wir über diese Entwicklungen lediglich, dass man seit 1998 im Rahmen eines sog. Ecoflex-Projekts mit zunehmendem Erfolg ver- sucht, aliphatische und aromatische Polyester zu copolymerisieren. Ein Granulat wird offen- bar auf einer 60-kg-Tonnen-Anlage erfolgreich eingesetzt. Das Material eignet sich gut für die Herstellung von Mikrofaser-Flächen und ist maschinell gut vervliesbar.
Polyester eignet sich aber auch bestens für die Garnherstellung. Dabei geht der Rein- technik-Bedarf in Richtung Multifilamentgarn. Diese Garne sind mit bis zu 175 Filamenten im Garnstrang lieferbar. Die Polyester-Garne werden mittels Rundstrick-Maschinen verstrickt, wobei dem Strickgut oftmals zur Beruhigung des Fadenlaufs so genanntes Stricköl zugesetzt wird. Zusammen mit dem bereits vom Spin- vorgang im Textilmaterial befindlichen Spinnöl mischen sich hier zwei Schmiermassen, die vor der Auslieferung an den Anwender unbedingt entfernt werden müssen um letztendlich Rei- nigungstücher hoher Oberflächen-Reinheit zu erhalten. Einer der großen Vorteile der Polyes- ter-Filamente zeigt sich in der vergleichsweise geringen Partikelfreisetzung sorgfältig dekon- taminierter Gestrick-Tücher oder auch der Vliesstoffe aus diesem Material.
PET Polyester
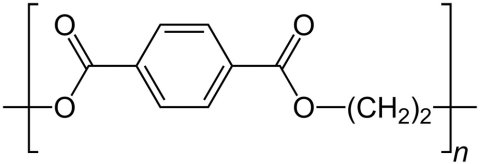
PET Polyester ist der Markenname eines durch Poly-Kondensation hergestellten thermoplastischen Kunststoffs. Er besteht aus den beiden Monomeren Ethylen-Glykol und Terephtalsäure. Die fachlich richtige Produktbezeichnung ist Polyethylenterephtalat C10H8O4. Das Material ist gegen viele Chemikalien beständig. Es ist zudem von hoher Festigkeit, hat einen Schmelzpunkt von 250 – 260 °C und nimmt praktisch kein Wasser auf. Diese Werte machen Polyethylenterephthalat für verschiedene Anwendungen geeignet. Ein großer Anwendungsbereich ist die Herstellung von Spinnvliesen aus Pellets. Das sind kleine tablettenähnliche Granulat-Körper, die den Transport und die Handhabung des Materials ermöglichen. Das Material eignet sich gut für die Herstellung von Mikrofaser Materialien und ist maschinell gut vervliesbar.
Polyester eignet sich aber auch bestens für die Garnherstellung. Dabei geht der Reintechnik-Bedarf in Richtung Multifilamentgarn. Diese Garne sind mit bis zu 175 Filamenten im Garnstrang lieferbar. Die Polyester-Garne werden mittels Rundstrick-Maschinen verstrickt, wobei dem Strickgut oftmals zur Beruhigung des Fadenlaufs so genanntes Stricköl zugesetzt wird. Zusammen mit dem bereits vom Spinvorgang im Textilmaterial befindlichen Spinnöl mischen sich hier zwei Schmiermassen, die vor der Auslieferung an den Anwender unbedingt entfernt werden müssen um letztendlich Reinigungstücher hoher Oberflächen-Reinheit zu erhalten. Einer der großen Vorteile der Polyester-Filamente zeigt sich in der vergleichsweise geringen Partikelfreisetzung sorgfältig dekontaminierter Gestrick-Tücher oder auch der Vliesstoffe aus diesem Material.
Polyamid
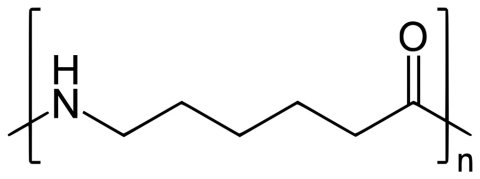
Polyamid ist in zwei von der Herstellung unterschiedlichen Gruppen bekannt geworden: PA 6 und PA 6.6. Diese beiden Gruppen ähneln sich in ihren physikalischen Eigenschaften: PA 6 entsteht durch Ringöffnungs-Polymerisation aus e-Caprolactam mit Wasserabspaltung. PA 6.6 hingegen wird aus Hexamethyldiamin und Adipinsäure hergestellt, wobei es unter Wasserabspaltung zu einer Polykondensation kommt. Unterschiede zwischen den Gruppen gibt es beim Schmelzpunkt. Der liegt bei 220 °C für PA 6 und bei 260 °C für PA 6.6 ist ein makromolekularer, teilkristalliner Thermoplast dessen mechanische Eigenschaften ganz wesentlich von der Kombination und Struktur seiner Molekülketten bestimmt werden. Polyamid ist als Polymerisat ein vielseitiger, hoch belastbarer „Technischer Kunststoff“, der in seiner Abriebfestigkeit dem Polyester vergleichbar und daher für die Herstellung von Wischmitteln der Reintechnik besonders gut geeignet ist. Polyamid-Garne gibt es in Filament-Durchmessern bis hinunter zu etwa 3 µm. Das ist deutlich unterhalb 1 dTex und man darf ein solches Garn daher der Gruppe der Mikrofilament-Garne zuordnen. Oftmals werden im Wischmittel-Bereich zu den Polyamid Garnen Polyester-Garne hinzugemischt. Dies ist ökonomisch sinnvoll weil Polyamid-Garne teurer sind als vergleichbare Polyester Garne. Technisch gesehen ergeben sich Vorteile aus der Feuchtigkeits-Aufnahme der Polyamid-Garne und der somit reduzierten elektrostatischen Aufladbarkeit der Garn-Kombination.
Composites
Composites haben für die Gruppe der HiTech- Wischmittel eine große technische und ökonomische Bedeutung. Insbesondere die Spunlace-Vliese aus Polyester-Holzschliff-Gemisch tragen schätzungsweise mit etwa 40 % zum Gesamt-Wischmittel-Bedarf der HiTech-Industrien bei. Das Material hat eine erfreulich hohe Festigkeit und ist noch ausreichend Wasseraufnahme-fähig und für viele Standard-Reinigungs-Aufgaben in der Industrie bestens geeignet. Betrachtet man diese Gruppe der Wischmittel unter Entsorgungs-Aspekten dann irritiert jedoch die Tatsache, dass das Material zu 50 % nicht biologisch aabbaubar ist. Das bedeutet die Polyester-Anteile verbleiben entweder in der Deponie-Masse oder müssen im Rahmen der Müllverbrennung entsorgt werden. Dieses Material ist Wasserstrahl-verfestigt. Das bedeutet: Prozessgemäß trifft eine große Anzahl sehr dünner Wasserstrahlen unter hohem Druck von einigen 100 bar auf den Holzschliff-Polyesterfaser-Mix der sich auf einem bewegten Sieb befindet, sodass fertigungsgemäß es im Rahmen der hohen hydrodynamischen Kräfte die zur Vliesbildung nötig sind, gleichzeitig zu einer partiellen Zerstörung der Holzschliff-Anteile kommt. Dabei werden unvermeidbar Partikel freigesetzt, die während der Reinigungs-Prozeduren aus dem Material austreten und den Reinigungsvorgang erschweren.
Eine andere Art von Composites besteht aus synthetischen Garnen für die Verstrickung deren Filamente, die zum Teil aus Polyester und zum anderen aus Polyamid bestehen. Diese Kombination kann aus mehreren Gründen vorteilhaft für das Endprodukt Reinraum-Wischmittel sein. In dieser Schrift bleiben die Garn-Composits aus Kostengründen jedoch unberücksichtigt.
Erkenntnisse
Verunreinigungs-Schichtdicke – als Maßgabe für die Wischmittel-Qualität. Stellen wir uns eine Oberfläche mit einer Rauigkeit von bspw. < Rz 3 µm vor und nehmen wir an, diese sei mit einer 1 mm dicken mittelviskosen Ölschicht belegt. Es sei die Aufgabe gestellt, diese Verunreinigung durch eine wischende Reinigungs-Prozedur um 90 % zu reduzie- ren. Der Instandhalter wird feststellen, dass sich diese Aufgabe mit nahezu jeder Art von Reinigungstuch und zwar auch ohne Zuhilfe- nahme eines Lösungsmittels bewältigen lässt. Bei gleicher Aufgabenstellung unter der Vor- aussetzung einer Ausgangs-Schichtdicke von 100 µm und einer Zielgröße von 10 µm wird die Reduzierung der Verunreinigungsschicht durch eine wischende Reinigungsprozedur
Unter der Voraussetzung einer Ausgangs-Schichtdicke von 10 µm und einer Zielgröße von 1 µm oder weniger ist die Reinigung falls überhaupt – nur mit speziellen Tüchern und evtl. unter Zuhilfenahme eines Lösungsmittels durchführbar. Wir lernen daraus:
Bei wischenden Reinigungs-Prozeduren ist der Reinigungsaufwand von einem in erster Näherung umgekehrten Verhältnis zur Material-Dicke und Oberflächenschicht und der Flächenhaftung der Verunreinigungs-Masse bestimmt. Im Rahmen unserer Wischmittelforschung haben wir Erkenntnisse gewonnen, die für Alle die mit den Prozeduren des wischenden Reini- gens befasst sind, von Interesse sein können und daher stellen wir sie hier zur Diskussion:
1. Erkenntnissatz
Mit abnehmender Dicke einer Verunreini- gungs-Schicht nimmt der monetäre Rei- nigungs-Aufwand überproportional zu. Im unteren Molekularbereich kann er für mehr- fach dekontaminierte, ultrareine Tücher hohe Beträge pro cm² erreichen.
2. Erkenntnissatz
Die Reinigungs-Effektivität wischender Reinigungs-Prozeduren steht in direkter Abhängigkeit von der Papillen-Zahl der Wischmittel-Oberfläche. Die Papillen-Obergrenze für HiTech-Reinigungs-Tücher liegt bei etwa 1.200 Papillen/cm².
(Als Papillen (lat. papillae) bezeichnen wir in Analogie zur Botanik die Topographie-bildenden aus der gemittelten Flächenebene eines textilen Flächengebildes (Gewebes, Gewirks, Gestricks etc) herausragenden Maschenteile auf seinen beiden Seiten. Bei Gestrick-Tüchern ist die Papillenzahl der Berührungsflächen identisch mit der Maschendichte in der Einheit:
n Maschen/cm²).
3. Erkenntnissatz
Mit zunehmender Rauigkeit Rz der Objekt- Oberfläche nimmt die Reinigungs-Effektivität einer wischenden Trocken-Reinigungs-Proze- dur stark, bei einer Feuchtreinigung mittelmäßig ab.
4. Erkenntnissatz
Für das wischende Entfernen einer Verunreini- gungs-Schicht der Dicke D bedarf es lediglich eines Wischmittels der Dicke von etwa D x 5. Das heißt: Wenn die Objekt-Oberfläche (z.B. aus Fensterglas) 10 µm dick verunreinigt ist, dann genügte ein Tuch von 50 µm Dicke zur Entfernung derselben.
Dies bedeutet für die Praxis, dass ein Groß- teil der Reinigungsaufgaben die z. Zt. mit Hilfe von hochpreisigen Gestrick-Tüchern durchge- führt werden genauso gut und kostensparend mit Hilfe dünner Langfaser-Vliese (Beispiel Drytech-Vlies) bewältigt werden könnten. Dies gilt jedoch lediglich für solche Applikationen, bei denen die Gebrauchs-induzierte Partikelfreisetzung aus den Langfaser-Vliesstoffen keine einschränkende Komponente ist.
Wir von Clear & Clean beschäftigen uns im Rahmen unserer Applikations-Forschung ausschließlich mit den Wischmittel-Anwendungen der HiTech-Industrien, der Medizin und der Raumfahrt. Aufgrund unserer konzeptuell begrenzten Unternehmensgröße sind uns daher für Forschungsaufgaben in anderen Gebieten Grenzen gesetzt.
Zusammenfassung für CELLULOSICS
VIiscose-Tücher gehören in die Gruppe der Cellulosics. Deren Schlüsselparameter ist eine hervorragende kapillarische Flüssigkeits-Aufnahme pro Zeiteinheit von 0,53 g/5 s/20 mm.
Wenn diese Tücher mechanisch nicht zu stark belastet werden, so hat man ein „gutwilliges, weichherziges“ Arbeitsmittel, das zudem durch seinen angenehmen „Griff“ bei den Anwendern seit 40 Jahren viele Freunde gefunden hat.
Das Tuch gehört allerdings bei einer Rauig- keit der Objekt-Oberfläche von Rz 0,5 trocken mit 5,4 kPart/cm² zu den Tüchern mit mittlerem bis hohem Partikelabrieb, der sich bei Rz 39 auf 8,6 kPart erhöht.
Vergleich der Abrieb-Daten:
Cellulosics auf unterschiedlich rauen Oberflächen (Angaben in Klammern). Datenangaben in kPart/cm²:
Composit-Tuch | 6,6 (Rz 5) | 0,9 (Rz 39 |
Cellulose-Tuch | 4.0 | 11,4 |
Viscose Tuch | 5,4 | 8,6 |
Cupro | in Vorbereitung |
Messung der LuftPartikelfreisetzung mittels Kleinwinkel-Agitation:
Bei ± 30° Winkelbewegung des Reinigungs-tuchs im Abstand von 4 cm oberhalb der Partikel-Sonde messen wir im Laminarstrom an Partikeln > 0,3 µm.
Vergleichsmessung beim Composit-Tuch
6 Winkel-Bew. von ± 30° = 0,3 Part.
60 Winkel-Bew. von ± 30° = 15,6 Part.
Vergleichsmessung beim Cellulose-Tuch
6 Winkel-Bew. von ± 30° = 6,8 Part.
60 Winkel-Bew. von ± 30° = 61,0 Part.
Vergleichsmessung beim Viscose-Tuch
6 Winkel-Bew. von ± 30° = 9,9 Part.
60 Winkel-Bew. von ± 30° = 43,8 Part.
Vergleichsmessung beim Cupro-Tuch
6 Winkel-Bew. von ± 30° = 19,2 Part.
60 Winkel-Bew. von ± 30° = 72,3 Part.
Fazit
Wir werden verstärkt daran arbeiten ein Rein- raumtuch mit Fasern von höherer Festigkeit bei gleich guter Saugfähigkeit vorzustellen und haben dafür bereits erste Schritte eingeleitet. Bis zum Erscheinen dieses Produkts empfehlen wir die folgenden Cellulosics bzw. Composits-Tüchern zu testen:
- Composit-Tücher aus PET und CE
- Tücher aus endlosen Cellulose-Filamenten
- dünnes Nassgelege-Vlies
- Viskose-Stapelfaser-Vlies
Es steht jedoch zu erwarten, dass alle Cellulosics-Tücher bei der Reinigung rauerer Oberflächen > Rz 10 zur erhöhten Partikel-Abgabe tendieren.
In diesem Fall bleiben dem Anwender zumin-dest aus dem Programm eines nord-deutschen Herstellers lediglich die Synthetics-Tücher: (je mehr Maschen desto teurer)
Tuch A | 170 Mesh PES-Gestrick |
Tuch B | 380 Mesh PES-Gestrick |
Tuch C | 400 Mesh PES/PA-Gestrick |
Tuch C | 540 Mesh PES-Gestrick |
Tuch D | 900 Mesh PES/PA-Gestrick |
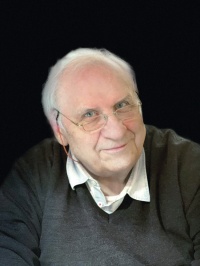
Win Labuda
Clear & Clean GmbH, Lübeck
© Clear & Clean
Widmung
Diese Schrift ist den Technologen Thomas Beck und Friedrich Reiff gewidmet, die bereits seit den 80er Jahren die Entsorgungs-Problematik von Polyester, Polyamid und Polypropylen bedacht hatten und sich als erste Reinraum-Beauftragte in Deutschland für den Einsatz von Spender-geeigneten Cellulosics-Wischmitteln entschieden.